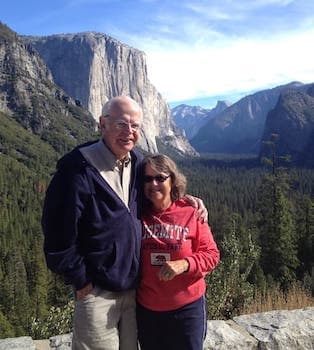
Curated with aloha by
Ted Mooney, P.E. RET
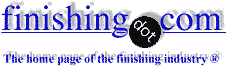
The authoritative public forum
for Metal Finishing 1989-2025
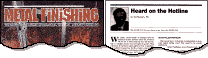
-----
Sulfamate Nickel pitting issue
July 28, 2011
Q. I work for a plating facility in WA state and do all the analysis and much of the upkeep on the electroplating tanks. I have been here only about 4 months and this is my first experience with electroplating so it has been a lot of learning.
I recently made up a new sulfamate nickel plating tank (50 gallon). First the sulfamate nickel, boric acid, nickel bromide and deionized water were added, then the tank was carbon polished for 4 hours. Brightener and anti-pit were then both added. I analyzed the tank for all these components (with the exception of the anti-pit for which there is no way for us to analyze) and they were all within the range of the producer's suggested concentrations. However, when a stainless steel bent panel was run in the tank it came out pitted pretty severely on the bottom of the bent part of the panel. The pitting was pretty much evenly spread throughout that portion of the panel. This pitting issue continues, no matter what we try and I cannot figure out what the issue is. Here is what we have tried so far:
-Carbon treating and re-adding the brightener and anti-pit
-adding additional nickel bromide
-dummy plating
-Adding extra anti-pit
The only one of these that seemed to decrease the pitting a bit was the extra nickel bromide, which caused the pitting to be isolated to just the outer edges of the bottom of the panel and along the bend in the panel.
Has anyone else had any experience with this?
chemist - Wenatchee Washington USA
A. Hi, Aileen.
Jumping to conclusions is dangerous, but based on the fact that you don't measure the effectiveness of the anti-pit, and the problem is pitting, I'm guessing that that's the problem :-)
Are the pits semi-hemispherical and bright? If so, they are probably "gas pits", caused by the generation of hydrogen bubbles which cannot detach soon enough because the surface tension is too high. Measuring the surface tension (that is, the effectiveness of the anti-pit) is relatively easy. You'll find many threads here on that topic, and hopefully one of our readers who does it frequently will give you a tip on that. You need to control the surface tension with the anti-pit, generally to about 30-32 dyne/cms, and to have good agitation to assist the process. Good luck.
Regards,
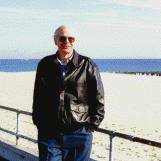
Ted Mooney, P.E.
Striving to live Aloha
finishing.com - Pine Beach, New Jersey
July 29, 2011
![]() |
A. Here are a couple "way out" thoughts that come to mind based on your info. (1) Low Boric Acid will cause pitting at the bottom of the rack. (2) tiny tiny air bubbles sucking through a loose filter hose clamp or fitting, will cause pitting. This is not the large air bubble from your agitation blower, this is a tiny bubble sucking through a loose connection. Go tighten all connections, then, as Ted says, add some surfactant. ![]() Robert H Probert Robert H Probert Technical Services ![]() Garner, North Carolina ![]() July 29, 2011 A. First, the anti pit can be tested and should be. It can be tested with a special glass tube called a stalagmometer. - Navarre, Florida July 29, 2011 |
Q. Yes, I believe the pitting is caused by air bubbles. The bottom of the panel is covered in tiny bubbles when we pull it out of the plating tank and the pits are very symmetrical and perfectly round. I have had several people confirm that they are most likely caused by air bubbles. Any suggestions for the best anti-pit out there for our application?
Aileen Helsel [returning]Electroplating - Wenatchee Washington USA
August 1, 2011
August 4, 2011
A. In most cases, pitting is not a result of lack of anti-pitting.
Pitting that is a result of low anti pitting, is mainly on the high current density areas.
You mentioned that you observe the pitting on the lower part of a bent panel. Let me understand, is it on the inner part of the L shape or on the outer part?
If it is on the inner part, it is what we call - shelf pitting and it is a result of small particles in the solution.
You did not mention filtration. I hope that you have continuous carbon filtration in the tank.
I hope the air pipe is not on the bottom of the tank because if it is, it will bring up the particles from the bottom
If pitting occurs on the outer part of the L shape, something is wrong with the air supply. Maybe it is too strong.
Last but not least, the anode must be shorter than the cathode.


Sara Michaeli
Tel-Aviv-Yafo, Israel
A. Let us assume that your bath has the correct composition. If that is the case, the causes of the pitting must be something else. Firstly, what is the bath pH - nickel sulphamate is pretty amenable, but likes to work at about pH= 3.6-4.5. I prefer to keep it at about 3.8-4.2. Secondly, what is the operating temperature? The higher the temperature (up to about 70 °C), the higher the applied current can be. Try doing a test at about 25 ASF at a temperature between 40-65 °C. Thirdly, is the bath and workpiece being agitated enough? If they are not, you can easily get gas bubbles on the cathode. Fourthly, have you done a Hull Cell test? If so, what does that show? If the Hull cell doesn't have pits, the cause is in the way the tank is being operated and the solution is OK; if you do get pits in the Hull cell, it is the solution that is at fault. Let us know the test results and the process information and maybe we can solve your problem.
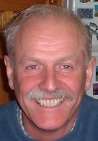
Trevor Crichton
R&D practical scientist
Chesham, Bucks, UK
October 5, 2011
adv.
"The Sulfamate Nickel How-To Guide"
by David Crotty, PhD
& Robert Probert
published Oct. 2018
$89 plus shipping
Q, A, or Comment on THIS thread -or- Start a NEW Thread