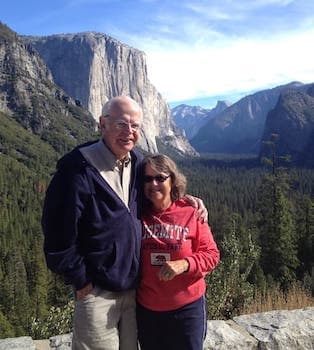
Curated with aloha by
Ted Mooney, P.E. RET
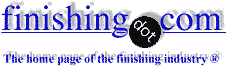
The authoritative public forum
for Metal Finishing 1989-2025
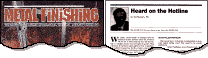
-----
Anodizing watermarks?
Q. I'm having a supplier issue where the parts we are sending them are coming back water marked. We are using a "AL-6060-T5" material and have seen color differences from this supplier in the first batch that prompted us to return the material initially, now we are seeing water marks. We have linished the material and re-anodized and are awaiting results.
From first go through, we are hearing it could be an issue with the material from the extruder. We have backtracked and verified the material used was correct. However, the issue of "watermarks" only started being noticeable after we sent back the batch for color and now are ending up with all these other issues which points me to a process problem.
Any input is appreciated
project manager - Australia
July 19, 2011
A. Send us some digital pictures of what you call "watermarks", meanwhile, try another anodizer.
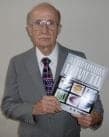
Robert H Probert
Robert H Probert Technical Services

Garner, North Carolina
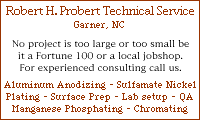
July 21, 2011
July 27, 2011
A. If your material is converted from silver anodised to color anodised finish, the anodiser first removed the silver anodic film in a caustic solution.
Then there are two possibilities:
1- Removal of anodic film may not be uniform all over the surface. Old residue of anodic film may result in such water mark appearance.
2- The "water marks" may be result of insufficient rinsing after caustic treatment or slow transfer from caustic tank to the rinse tank. If caustic solution residue is not removed from surface quick enough, caustic continues to etch "eat" the surface resulting in irregular appearance after anodising.
Hot rinsing instead of room temp rinse after caustic tank is also helpful to clean the surface.
Good maintained bath composition and proper rinsing between each process tank is important to have good quality anodized finish.
I also strongly recommend anodiser colleagues to use wire brushing machine prior to anodising to have decorative matt smooth surface after anodising.
- Istanbul, Turkey
We found that the anodizer did not linish the parts, but instead used scotch brite which has at least "masked" the water marks from showing up.
As most would guess, we are going with another anodizer for future products and will be able to verify if the process or material was the issue.
- Australia
August 2, 2011
Q. Hello, I started anodizing aluminium parts I machine. For electrolyte I use a 16% sulfuric acid agitated with aquarium air pump. I degrease parts in a degreaser for 5 min, rinse them in water, then put them in 8% nitric acid tank for 1 min, then rinse them and then put them in anodizing tank. I use 720 calculator to calculate a current for anodizing using a 6 amp/square foot current density. After anodizing I seal the parts in boiling water mixed with [brand name deleted by editor] anodizing sealant.
The parts are small sheet metal lids, I use a titanium rack and anodize 30 lids at a time for 35 min to get a 0,25 mil thick anodic layer.
The problem is that I am not getting a stable process and most of the parts have white/slight yellow stains on a surface. I would appreciate some guidance in solving this problem.
Photo with a staining attached. If the part is wet, the staining is not visible, but when dried, it is pretty visible.
- Lithuania, Kaunas, Europe
March 9, 2020
----
Sorry, no pics rec'd, Naglis. Attach them in an e-mail to mooney@finishing.com please.
A. 1- Did you measure coating thickness of lids by machine? Might be that 0,25 mil is not enough for these lids.
2- hot sealing duration may not be enough for proper sealing (normally it should be at least 3 min per micron)
3- Did you check hot sealing temperature by glass thermometer? (normally it should be over 98 °C)
Please check all three subjects ... Actually, I suspect hot sealing process. If I were you I would do some testing during production. For example you would skip hot sealing bath for one bar testing. If you don't see any defects which you mention then you would find source of problem.
Good Luck.
- TURKEY,sakarya
March 18, 2020
A. 1. Tell us the alloy. 2. Look for water breaks after "degreasing". 3. Raise the Nitric Acid to 30%. 4 Disregard the 720, increase the agitation, use 21 volts on 2000 alloys and 16 on all others. 5. Get the pH of the seal between 5.0 and 6.0.
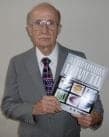
Robert H Probert
Robert H Probert Technical Services

Garner, North Carolina
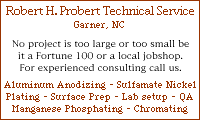
March 22, 2020
Q, A, or Comment on THIS thread -or- Start a NEW Thread