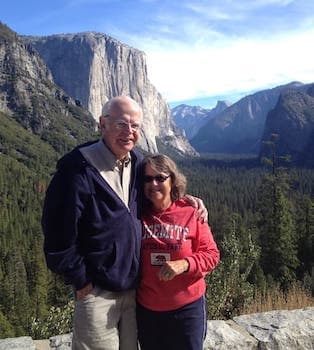
Curated with aloha by
Ted Mooney, P.E. RET
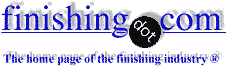
The authoritative public forum
for Metal Finishing 1989-2025
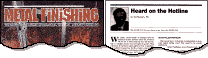
-----
Spinning large galvanised bolts.
June 30, 2011
Hi I need to partly galvanise long (1000+ mm) bolts 25 to 50 mm in dia.
Can anyone recommend the rpm each bolt needs to spin at after dip?
And does it go in the water first after the kettle and then spin, or spin after the kettle and then to the water?
Thank you
Engineer - South Africa
First of two simultaneous responses -- July 1, 2011
Sir:
Spin-a-batch in indexed racks, with partial immersion and spin upon withdrawal from the zinc is the easy way to do this. Alternatively two saddles, one high and one low (in the zinc) with an inclined plane down the side of the kettle to roll the bolts and a quench tank at the end of the inclined plane is another way.
It is not a good idea to galvanize the bolts (again with partial immersion) and then later to put the threads into an oven and brush the threads. Overheating the steel can weaken the steel and have the bolt break in service.
Regards,
Galvanizing Consultant - Hot Springs, South Dakota, USA
Second of two simultaneous responses -- July 4, 2011
About 600 rpm seems suitable, but some run 720 rpm.
The objective is to centrifuge off surplus zinc, so that zinc must be molten, so quenching before spinning would be pointless.
It is important to get the material spinning as soon as possible after coming out of the zinc, in order not to loose too much tmeperature.
Normal galvanizing might have a crane speed of say 1m/min (3 ft/min) in raise out of the zinc kettle, but in order to save time, that slow withdrawl is best omitted. get it out and spinning as quickly as is safe.
Spinning doesn't need to be long - as long as it takes to get to full rpm, then slow and then quench.
Given the right equipment, items of 100 mm dia x 1m can be quite successfully spun, but care is required to have a centralised load to avoid vibration.
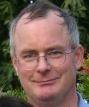
Geoff Crowley
Crithwood Ltd.
Westfield, Scotland, UK
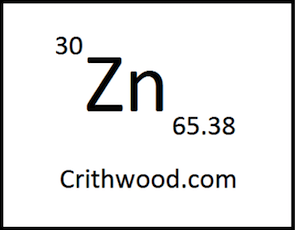
A good way to protect threaded fasteners, particularly long ones is by Thermal Diffusion Zinc (TDZ). There is a company doing this in Johanesburg.
It is done at temperatures far below the melting point of zinc. It is does not create Hydrogen Embrittlement and is uniform and controllable.
- Boston, Massachusetts, U.S.A
July 27, 2011
There is a special technique to do the Hot Dip Galvanizing of Threaded items.
1. Thread on job to be Galvanized is done under size say 0.1to 0.15 mm.
2. Job is Galvanized as usual.
3. If it Galvanized partially it is difficult to put on centrifuging. Normally in this type of cases the work is quenched in a very hot passivation Solution or Air quenched.
4. Now you can re thread the threaded part as nut or re-heat the threaded part, clean the extra Zinc with wire brush and put the nut in hot.
Hope this will meet your needs.
- Mumbai, Maharashtra, India
July 31, 2011
Q, A, or Comment on THIS thread -or- Start a NEW Thread