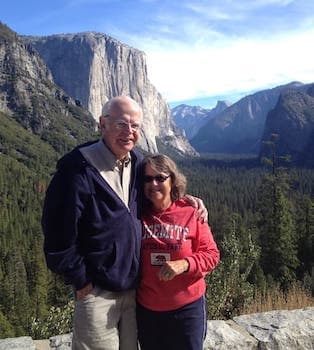
Curated with aloha by
Ted Mooney, P.E. RET
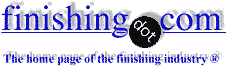
The authoritative public forum
for Metal Finishing 1989-2025
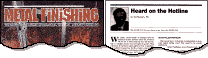
-----
MIL-DTL-5541F Conversion Coating of Aluminum for EMI/EMC needs
June 21, 2011
Hi:
I am in the electronics packaging business for military aircraft and Navy applications. Most of the computer chassis we design are made from 6061T651 or 5052-H32 grade aluminums. One of the key concerns in this industry is EMI/EMC compatibility. Basically don't radiate, conduct, or be a conducted or radiated victim of stray electromagnetic energy, it throws a wrench in the works. This is the classic, 'Please turn off all electronic equipment while the pilot lands' except in my case it is while the pilot is landing on a carrier deck. In order to limit the EMI a computer or piece of Avionics is subjected to, we typically specify a clear conversion coating. This coating has significantly less surface electrical resistance, thereby limiting radiation and improving conduction. This is all good via clear hexavalent chromate conversion coatings. Specifically, MIL-DTL-5541F, Type I, Class 3.
From the MIL spec.
"1.2 Classification. The chemical conversion coatings are of the following types and classes.
1.2.1 Types. The chemical conversion coatings are of the following types (see 3.1):
Type I 'Compositions containing hexavalent chromium. Type II 'Compositions containing no hexavalent chromium.
1.2.2 Classes. The materials, which form protective coatings by chemical reaction with aluminum and aluminum alloys, are of the following classes (see 6.1 and 6.4).
Class 1A - For maximum protection against corrosion, painted or unpainted.
Class 3 - For protection against corrosion where low electrical resistance is required."
With the push toward trivalent chromate coatings (MIL-DTL-5541F, Type II, Class 3), has a definitive study been performed on the differences between type 1 and type 2? Who is certified to perform this process (I am in the Midwest) and is anyone doing this as an electronics specialty? You mentioned in one of your postings that there is significant variation between vendor X, Y, Z, etc for these coating because they are proprietary. What feature or function makes them proprietary? I run enough parts through the factory I might be able to justify the cost of a trivalent line, any suggestions other than think twice?
Respectfully,
VP Engineering, computer manufacturer - Hiawatha, Iowa, USA
Q, A, or Comment on THIS thread -or- Start a NEW Thread