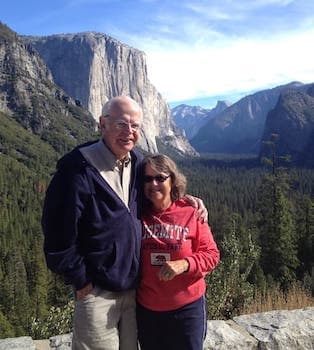
Curated with aloha by
Ted Mooney, P.E. RET
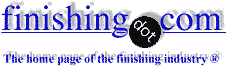
The authoritative public forum
for Metal Finishing 1989-2025
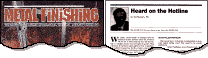
-----
Solutions to Problems With Passivation and Salt Spray Testing of 15-5 PH Stainless Steel
Current question and answers:
Q. Hello,
We have some 15-5 parts that are 50% grit blasted and 50% machined surfaces. We do AMS2700 Type 2 passivation with a dichromate dip. The parts pass water immersion test but about 50% fail Salt Spray test. Would anybody have any suggestions on why this is happening?
Thank You
- Thousand Oaks, California
January 29, 2021
A. On December 23, 2011 in topic 58121 Lee Gearhart wrote:
"The problem with salt spray on 17-4 is a risk of false positives. Even fully passivated, it can show rusting, although the 2 hours is a short amount of time. That's why our choice of standard procedure is the humidity test. It takes longer, but we don't get any false positives.
Yet if one of our vendors used salt spray to test passivation on our products, I wouldn't object."
In my experience I agree with Mr. Gearhart: salt spray test on PH steels is too sensitive. Use copper sulphate.
- Lod, Israel
January 31, 2021
A. The 15-5 or 17-4 material are not designed to pass a salt fog test and can give false positives and recommend immersion or humidity test for those material types. In some case I found passivating after blasting before laser marking and then passivating again after laser marking you will a better pass rate and wouldn't lift the laser marking
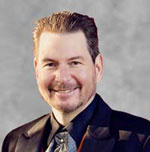
Mark Battles
Plymouth, Minnesota
February 1, 2021
⇩ Related postings, oldest first ⇩
June 11, 2011
I am a lab tech for a manufacturer of aerospace roller bearings with an in house plating shop. Some of our bearing components are 15-5 PH material for passivation. We use a passivation bath per AMS2700; Method 1, Type 2 and are required to salt spray, per ASTM B117, a sample of the passivated components for 2 hours.
Our problem is we are seeing spots of red corrosion after components have been salt spray tested.
Our process is as follows:
1. Alkaline soak clean to remove shop oils.
2. RO water spray rinse.
3. Compressed shop air to dry parts.
4. Glass bead blast using US Sieve 170-325 media.
5. Compressed shop air to remove excess glass bead.
6. Passivate for 30 minutes.
7. RO water spray rinse.
8. Compressed shop air to dry parts.
6. Salt spray test.
Thus far we have made up several new passivate baths and maintain bath chemistry per AMS2700. We have also cleaned out glass bead blast cabinet and replace media with new media. Problem still exists.
Could we be picking up iron particles at some point and passivate bath is not able to remove these particles?
Any thoughts on this would be appreciated.
Lab Tech - Downers Grove, Illinois, USA
A. Good day fellow lab tech. Sometimes problems are difficult, sometimes easy. I experienced similar issues. We checked our compressed air and it was a surprise to see what it actually contained. Good luck
Eric Bogner- Toronto Ontario Canada
June 17, 2011
Q, A, or Comment on THIS thread -or- Start a NEW Thread