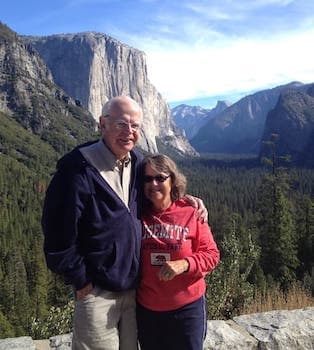
Curated with aloha by
Ted Mooney, P.E. RET
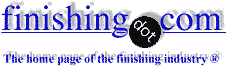
The authoritative public forum
for Metal Finishing 1989-2025
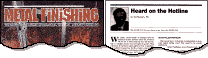
-----
Best Finish For Cast Aluminum Mailboxes and Posts in Florida Climate
June 2, 2011
Hello,
I own a small mailbox manufacturing and installation business in SW Florida. I am currently powder coating my mailbox components individually and then assembling the components using a variety of stainless steel hardware.
I have been talking to an owner of a sandblasting company in Naples, and he is trying to convince me that there is a more durable paint application than my current method of acid-washing my cast aluminum parts, then powdercoating them with a primer and then a finish coat of powdercoat.....
He said that the powdercoat is actually too hard and that it becomes brittle and that once it fails the oxidation process will spread rapidly. He is saying that sandblasting and then applying a self-etching primer and then an automotive paint will outlast my method.
Any opinions?
PS: How much do I have to worry about the interaction between my stainless steel hardware and my powdercoated aluminum? Should I be using nylon washers to keep the different metals from coming into contact, even though the cast aluminum has a primer and powdercoat finish?
Thanks for any unbiased feedback you can offer.
Business Owner - Lehigh Acres, Florida
June 2, 2011
Hi, John.
I'm unbiased, but that doesn't mean I'm right. Only testing will produce a sure answer.
But my opinion is that going to sandblasting would be taking a step backwards. There is substantial corrosion-fighting value imparted by a chromate conversion pretreatment, and at least some value if the pretreatment is phosphatizing. Of course, it's mix and match -- you could apply wet paint after these chemical pretreatments or powder coating after sandblasting.
But don't assign mystique to "automotive paint". The reason automobiles resist corrosion so well is not magic paint, it's the systematic multistep approach to corrosion fighting: engineering for no exposed seams or welds or crevices, mechanical preparation, galvanneal for cathodic protection, followed by phosphatization to prevent undercutting corrosion, then electrocoating for guaranteed 100% coverage, before painting in cleanrooms so there are no entrapped particles, and final clearcoating.
Dissimilar metals always present the opportunity for galvanic corrosion when they are in electrical contact, so nylon insulators would be best. But this application doesn't sound critical and I suspect it would actually be okay without them. Good luck.
Regards,
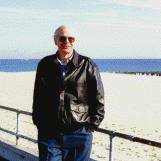
Ted Mooney, P.E.
Striving to live Aloha
finishing.com - Pine Beach, New Jersey
June 3, 2011
I agree with Ted.
There are a great many powder formulations available today. Any of the larger powder material vendors would be happy to make recommendations for a very good one for the area and for the UV exposure that it will get.
Stainless and aluminum are not bad choices for your product. I do not think that the nylon washers will help that much as you still have a SS/Al contact in the threads. Paint will help.
- Navarre, Florida
Hi John,
I also spent much time at solving the bad corrosion of cast aluminum motor parts.
In my opinion the hard powder coating is not the root cause of corrosion fail.
Can you show me a picture of actual cast aluminum part that less anti-corrosion?
I will offer the countermeasure to you after viewing the sample pictures.
Thanks & best regards!
- Hanoi, Vietnam
June 9, 2011
Q, A, or Comment on THIS thread -or- Start a NEW Thread