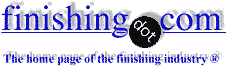
-----
Electroless nickel on opposing surfaces
May 31, 2011
Hello,
Background: I am a scientist/engineer who often encounters plating issues/failures on hardware manufactured by others. I have a reasonable amount of "book knowledge" on plating, but very little hands-on experience. I currently have a nonstandard usage of electroless nickel that I am considering as a research tool, and I thought I'd ping the experts on this site for their experience.
Essentially, I am looking to use an electroless nickel plating process in order to bond two opposing surfaces to one another. Electroless nickel is certainly a great process for achieving uniform thickness on complex or even interior surfaces. However, if two surfaces were brought close to one another (say, a thousandth or two) in a bath, what would happen? My gut tells me that those surfaces would become starved of solution, and the plating would either be of poor quality (due to compositional, pH, etc. variations) or would cease altogether.
What if techniques were used to retain liquid at the interface (e.g. pressure, seals, geometry)? Does anyone have any thoughts or experience with something similar? I considered that the behavior of this plating solution with deep, high aspect ratio crevices might provide some insight. Does anyone have any experience with electroless nickel in coating parts such as that?
I appreciate any feedback. I should mention that though this is my first post here, I do often use and appreciate this site as an invaluable tool for '*real world*' experience in plating operations.
Best regards,
Pete
Researcher - El Segundo, California, USA
Hi, Pete.
If at least one, preferably both, of the plates were highly perforated like swiss cheese, I think I'd see some hope of achieving this with careful fixturing. If they were not perforated that way, I can't imagine the plated interface layer itself looking different than swiss cheese -- but, sorry, no practical experience.
I have installed electrolytic nickel plating lines in steel mills for the purpose of plating steel and stainless steel sheets for subsequent bonding together to make laminated plates with thin but expensive stainless steel linings bonded onto inexpensive and thick structural steel plates.
Regards,
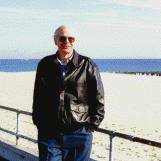
Ted Mooney, P.E.
Striving to live Aloha
finishing.com - Pine Beach, New Jersey
May 2011
EN requires solution flow to plate properly. There is no practical way to overcome this. If you pumped it, you would require some picky and expensive fixturing. You could certainly experiment if it were a single part.
James Watts- Navarre, Florida
June 1, 2011
It would be for a specific specimen configuration, so common fixturing could be used. I'm sure I could play around with it for a while if I had a bath handy, but it your comments confirm my suspicion that the likelihood of success would be low. Thank you for the responses.
Peter Hess- El Segundo, California, USA
June 2, 2011
It seems to be a brazing application. Under vacuum capillary action takes care of this situation very well. There are numerous metals and alloys that can be melted at different temperatures, some of them with properties very similar to electroless nickel.
G. Marrufo-Mexico
Monterrey, NL, Mexico
June 8, 2011
Q, A, or Comment on THIS thread -or- Start a NEW Thread