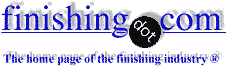
-----
Painting/Powder coating cast iron: gassing problem
Q. I am looking for any suggestions to increase the adhesion performance of direct to metal (DTM) coatings for large cast iron and cast steel parts that also have machined surfaces with surface roughness of approximately 30 Ra. We are currently using a DTM two component coating [(2 (base) : 1 (catalyst) ratio] and all of the parts go through a phosphatizing pretreatment/cleaning operation prior to paint. I am having the most trouble on the MACHINED SURFACES. I would appreciate any suggestions regarding adhesion promoters, etching, cleaning, etc. to get better coating adhesion on the parts. I do not have ovens to preheat the parts or cure the coating.
Thanks in advance.
Jeff Thompson- Mayfield, Kentucky
1999
A. For getting better performance you need to perform the following necessary stage:
ALKALI PERMANGANATE SOLUTION CONSIST OF
100 GRAMS PER LITER Sodium Hydroxide
100 GRAMS PER LITER potassium permanganate ⇦ on eBay or Amazon [affil links]
Temperature = 90 °C
Note : Dipping time approximately 30 minutes , then rinse and dip in some acidic solution
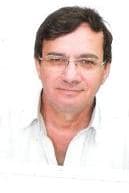
Yehuda Blau
YB Plating Engineering and Quality - Haifa Israel
1999
A. I suspect that you are using a lightweight iron phosphate treatment (cleaner coater). I suggest that you consider a calcium modified zinc phosphate process which with the addition of suitable detergents can be used as a "cleaner-coater". Even better will be a Class 1 massive iron phosphate used after a micronised manganese phosphate pre-dip. 60 secs pre-dip cold followed by 5-10 mins Class 1 iron at 90 °C and 30 pts. Water wash and dry.
Roger Bridger- Croydon, Surrey, UK
2000
A. Jeff
Look at the pH of your last stage sealer (final rinse) and see if keeping the pH between 8.2-8.8 and a total or "M" alkalinity part per million range of 350-600 ppm In working at similar process as your doing I have observed a DEA or MEA ( amine type alkaline final sealer ) to improve adhesion on machine surface sides of cast iron product. Air-knife off excess water and consider heating part to help outgas off any acidic residue in the porous cast surface.
Brian Lamphron- Sioux Falls, South Dakota
2000
Multiple threads merged: please forgive chronology errors and repetition 🙂
Powdercoat outgassing on cast iron
Q. I have a cast iron sink that I had the porcelain sand blasted off, sanded the metal smooth and had it powdercoated. My powdercoater experienced outgassing in the bottom of the sink bowl and after a number of attempts at heating it higher than the powdercoat temp,and other tricks,the outgassing still occurred. I am convinced it is a casting problem. Does anyone know of a way to seal bare cast iron to prevent this? Would Lab-metal ⇦ on eBay or Amazon [affil links] thinned down and brushed on work for this problem?
Rod Waltershobbyist - Des Moines, Iowa
2005
A. Maybe a different coating system that doesn't require heat, it's the heat of the curing process that's causing the problem, and I've seen castings that outgas no matter what tricks you try on them. There are powders that have a longer gel time in order to give you a better chance at eliminating the outgassing if your married to the powder coating. Your coater should be able to get it from one of his paint suppliers and maybe try that if he hasn't already.
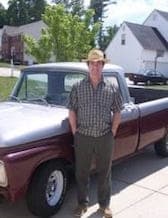
Sheldon Taylor
supply chain electronics
Wake Forest, North Carolina
2005
Powder coating over cast iron
Q. Good morning:
Our plant wants to apply powder paint over Cast Iron. My question is which it's the best process to do that?
I have reading that to outgassing this material type we need to preheat two hours.
And the best pretreatment process is the zinc phosphate..
Regards from Mexico
Paint process Eng. - H. Matamoros; Tamaulipas, Mexico
April 26, 2010
Q. How do we prevent the carbon present in cast iron from adversely affecting the powder coating process. The components are fully machined but require painting
MARTIN WALKERENGINEER - UNITED KINGDOM
May 25, 2011
A. I've not noticed carbon being a problem in powdercoating cast iron.
What problem symptoms are you experiencing?
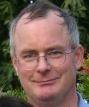
Geoff Crowley
Crithwood Ltd.
Westfield, Scotland, UK
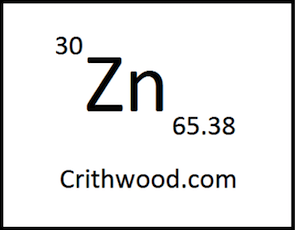
May 27, 2011
June 1, 2011
A. I suspect that the problem you seek to avoid is more to do with gas entrapped in the casting than Carbon content.
My experience with CI parts is to treat them pretty much the same way as with HDG parts.
De-gas the parts by exposing them to a temperature ~20-30 °C metal temperature above powder cure temp for ~20-30 mins.
Then make sure you are using a de-gas powder (often referred to as casting grade).
The object is to drive out as much gas as possible before pre-treatment and then to extend the Gel time of the powder during the cure cycle to allow any residual gas to escape.
Hope this helps.
Regards,
Bill
Trainer - Salamander Bay, Australia
June 3, 2011
A. The issue of "gassing" is an interesting one. Seems to occur almost exclusively on casting (both iron and aluminium) and HDG.
We are embarking on a research project soon to try to get to the bottom of this phenomenon.
There are many opinions as to what causes it, what gas it really is, how to avoid it, or to cause it to evolve prior to curing.
"Ant-gassing" powders gel slower, allowing time for evolved gas to escape and the coating to reform smoothly after a bubble pops though. They have (I understand) more wax in their formulation.
The common "cures" for gassing are not foolproof.
Anti-gassing powder sometimes don't cope.
"de-gassing" doesn't always work.
These factors seem to have some influence:
steel chemistry; In HDG, the thickness of zinc; The hanging orientation; the colour; the metal thickness; The pretreatment route.
I'm keen to get as many opinions as possible on this phenomenon.
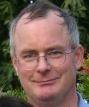
Geoff Crowley
Crithwood Ltd.
Westfield, Scotland, UK
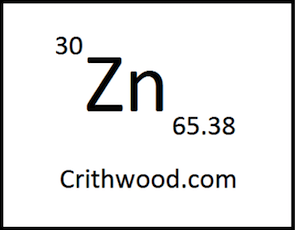
Dear Geoff,
Yes we would be very pleased to get involved with your company and local university in an endeavour to discover how and why gassing occurs during the baking of a powder coating film when applied to a galvanized substrate. By including waterborne primer into the University program we may obtain some answers to why it seems no longer necessary to pre-heat or T-wash a galvanized substrate prior to powder coating.
I believe getting involved with this exercise will help us to understand why/how a waterborne primer works in this application. Could it be that the wetting agents in the formula (included to wet a metal substrate and help with pigment dispersion) allows the waterborne primer to apply evenly over a metal substrate but also allows the primer to sink into the galvanized coating and displace any air/gas that may be en-trapped within?
I understand that you will be contacting us for samples when the University is ready to begin its investigatory exercise.
Terry
Birmingham, United Kingdom
June 8, 2011
June 9, 2011
A. The problem with castings is relatively easily explained, i.e., porosity.
The problem with HDG is a little more interesting.
I observe that BS 6497 calls for air quench.
I always thought this was more to do with Sodium Dichromate used in the water quench to delay White rust onset and which interferes with Powder adhesion.
Maybe air quench also allows entrapped gases to escape?
I wonder what comparative results would be achieved if the metal was IR heated rather than convection heated at the de-gassing phase?
This subject should be attracting a wider audience to provide as much independent input as possible.
The recognised contributing factors might be more fully elaborated on to assist us all as well.
For Example: how does hanging orientation affect the phenomenon?
Let's get together on this one for everyone's benefit.
Regards,
Bill
Trainer - Salamander Bay, Australia
Multiple threads merged: please forgive chronology errors and repetition 🙂
Q. I would be interested in any insight into the outgassing of gray cast iron during powder coating. The occurrence is sporadic, but apparently far more frequent in gray iron than in nodular iron. Our process is to shot blast the surface, then pre-heat to 220-280 °F prior to painting, then curing that 310 °F.
Simply allowing more time after casting prior to painting has not had an effect. We are about to try an extended, higher temperature pre-heat, but then we need to allow the casting to cool to an appropriate temperature for painting. Any thoughts on the actual mechanism of outgassing? What is the role of the graphite flake?
- Chattanooga, Tennessee, USA
January 31, 2012
! I've recently started working with Geoff Crowley at his Galvanising and Powdercoating shop in tandem with a local University and I'm looking into the Pinholing/ Gassing issues associated with powdercoating metals.
From early studies of examples coming through, metal thickness and steel chemistry seem to be contributing factors; thick cold rolled structural steel is a substrate seen in recurring incidences perhaps more so than other components (although I'm completely open minded to the possibility of other contributing factors being more important)
I'd be really interested to hear if other powdercoaters see any trends in where pinholing/gassing occurs or whether they consider it a more random issue than that.

Rikki Speakman
- Cumbernauld, Strathclyde, Scotland
February 3, 2012
February 12, 2012
A. Hi Rikki,
You must be feeling a little let down by the lack of replies?
Trust me, it is not because of a lack of interest.
This is one of the two major bugbears confronting the Powdercoat Industry.
Geoff suggested in an earlier post that he had identified a number of influencing factors.
Perhaps if you were to enumerate those it will inspire more robust contributions.
Many of us have theories but have not had the luxury of a purely scientific and analytical program to test these.
Regards,
Bill Doherty
Trainer - Salamander Bay, Australia
February 17, 2012
Hi Bill,
I think the issues Geoff talked about on June the 3rd last year on this thread sum up many of the potential causal effects, maybe the original steel processing (will tie up with the original cast issue of the thread) and stand down times between parts of the process are a couple of possibilities worth adding to the list.
We don't have a huge amount of quantification just now on the impact of these individually, hopefully we can develop that over time. Certainly though the vast majority of pinholing in my first few weeks has been seen on thick metal parts and structural steels, so hopefully get my teeth stuck into those swiftly,
Regards,
Rikki

Rikki Speakman [returning]
- Cumbernauld, North Lanarkshire, Scotland
Outgassing from Cast iron panel causing cratering on baked finish
Q. When a solvent based alkyd low bake coating applied to a rotor or other cast iron smooth parts we get fine finish. How ever the same paint on ACT ground cast iron panel, the finish is not fine. It bubbles and or creators. Why?
Raman Patel- Detroit, Michigan
August 24, 2015
A. My Dear,
You pre-heat the substrate at about 80 °C, allow to cool to 45/50 °C, then start coating.
Minol Coating Pvt Ltd - Sachin, Surat, Gujarat, India
October 25, 2015
Q. I was wondering how to determine how much higher do you outgas bullets at than paint them at (we outgassed at 495 degrees for 3 feet, then we paint at 475 3 feet they stay in the oven for 15 min but they scuff when we put them in a bag. Thank you
kelly noton- pleasant hill Missouri
September 30, 2015
A. Hi Kelly. Are these bullets made of cast iron or have we crossed threads a bit? What are the bullets made of? What are you "painting" them with. I doubt that slightly improper outgassing protocol accounts for softness of the paint.
Regards,
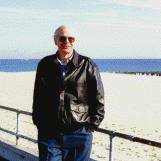
Ted Mooney, P.E.
Striving to live Aloha
finishing.com - Pine Beach, New Jersey
October 2015
Pretreatment for SG CAST IRON PARTS
Q. What is recommended pretreatment for SG [Spheroidal Graphite] Iron casting parts before doing powder coating or painting? Some areas of the parts are machined.
Abhijit bapat- Pune, India
February 26, 2016
Hi Abhijit. We appended your inquiry to a long and very informative thread on the subject. You may wish to review it, and then re-cast your questions in terms of what has been said. Good luck.
Regards,
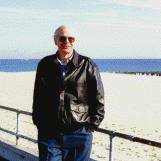
Ted Mooney, P.E.
Striving to live Aloha
finishing.com - Pine Beach, New Jersey
February 2016
Q, A, or Comment on THIS thread -or- Start a NEW Thread