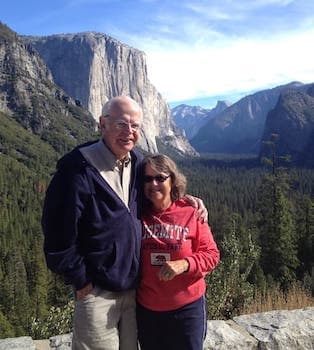
Curated with aloha by
Ted Mooney, P.E. RET
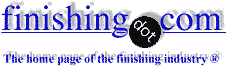
The authoritative public forum
for Metal Finishing 1989-2025
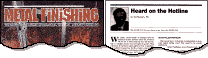
-----
No ID coverage in Zinc nickel plating
May 4, 2011
Q. Dear sir,
We are doing zinc nickel plating and maintaining Ni%10-15 and thk 8-15 microns and we are using Growel chemical for top up (Zincalume NiZ 551,552,553,554,555) recently we are facing problem that our component ID (Inside dia) is not plating properly ID size is 2 mm to 5 mm. I want to know reasons for ID not plating.
Some details below for reference
1) Type of plating ; Barrel
2) Current; 20-25 Amps
3) Volts ;5-6 Volts
4) Barrel capacity; 9 Kgs
5) Loading weight; 7 Kgs
6) Loading time ; 3 Hrs
7) Caustic ; 120-140 maintaining
8) Zinc metal; 8-14 maintaining
plating shop employee - Bangalore, India
A. Hi,
I guess the plating load is more as compared to the current you are passing is low, so either you reduce the loading or increase the current.
Before shuffling the chemicals look into the mechanical arrangements.
Regards
Praveen
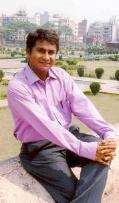
Praveen Kumar
plating process supplier
Mumbai, India
May 5, 2011
May 6, 2011
A. Hi,
You did not mention RPM of the barrel.
Keep it 5 or less than 5 RPM.
Regards
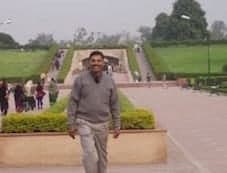
T.K. Mohan
plating process supplier - Mumbai, India
A. Gentlemen,
I feel 3 hours is a very high time for a barrel for Zn Ni. Also are you sure about the current and voltage? If you still feel you need a faster rate of deposition ask your supplier. Barrel as such is a extremely LCD plating and your chemical supply competitors has an additive for extreme LCD which can help you .
plating process supplier - Bangalore, India
May 17, 2011
May 18, 2011
A. Dear Darsan
Please check the temperature and maintain within 25 °C and also the additives plays important role to get better throw inside. Also try to maintain always around 10 to 12 gm/l by hanging Zinc anodes side of the tank with anode bag.
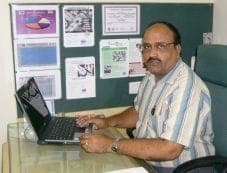
P. Gurumoorthi
electroplating process chemicals - Chennai, Tamilnadu, India
Optimising Zinc Nickel Throw Into Holes
Q. My company is looking to introduce a thin zinc nickel finish on some of our components. In order to optimise the plating process I am working with the platers to establish the best way to plate small housings which include recessed features (4x10 mm blind holes & 10x20 mm slots).
The challenge we face is we require 'some' plating within these features but at the same time must limit the thickness and HCD build-up on the same face. My question is by altering physical properties of the bath (i.e., part location/orientation, racking setup, agitation, current vs. time etc.) can we improve the throw of plating into the recessed features without experiencing excessive HCD build-up? Also if we introduced a 0.5 mm chamfer to the face & features would this reduce HCD build-up effecting tolerances on the face?
design engineer - UK
June 16, 2017
Zn-Ni thickness increased in only one of two locations
Q. A supplier is Zn-Ni rack plating a 280 g 1018 steel part for us (a housing for a automotive sensor)
In measurement location 1 which is at a thin section of the part we get the highest plating thickness.
In measurement location 2 which is at a relatively thick section of the part we get the lowest plating thickness.
In order to increase the plating thickness (overall) by about 1 µm the supplier increased the current from 200A to 260A and also increased the time from 45 min to 55 min.
The result of this was that only in measurement location 1 the plating thickness was increased by 1 µm and in measurement location 2 nothing happened.
Any idea why this is and how we can increase the thickness in measurement location 2? We care less about measurement location 1 as the plating thickness is already the highest there.
Design Engineer - Hengelo, The Netherlands
June 16, 2017
A. Hi Lewis; hi Jaap. Hopefully someone with specific experience on a similar problem with Zn-Ni plating will reply, but in the meantime: the plating tends to deposit in proportion to the ampere-minutes supplied, as described by Faraday's Law of Electrolysis, but the current tends to follow the path of least resistance.
For Jaap's problem, it may be possible to rack the parts in a better orientation so the electricity is better distributed. Sometimes, you can rotate parts on the plating racks such that the HCD [high current density] areas are sort of face-to-face, stealing current from each other. It's more complicated to "shield" areas of the parts with plastic flats, blocking the straight path of field & ions such that the formerly HCD areas are no longer HCD areas, but it can be done. If improved racking and/or shielding are prohibitive you are restricted to chemistry, temperature, agitation, and brightener adjustments which the solution vendor will probably have to help the plating shop with.
Lewis's problem is a tough one. Getting coverage in blind holes is difficult: everything is conspiring against you from very low current density to depleted plating solution to air or solution entrapment. It may be necessary to rotate the parts during plating. Theoretically you could put auxiliary anodes made of stainless steel or platinum clad titanium wire into those blind holes, but it's usually not very practical for production work. Again, a big part of the answer may be to make sure that those plating shops are taking full advantage of the solution supplier's knowledge base.
Regards,
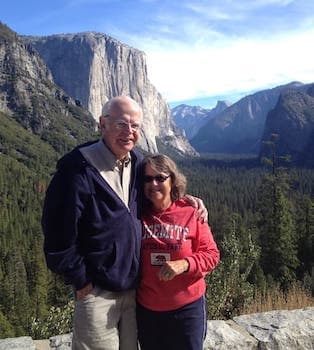
Ted Mooney, P.E. RET
Striving to live Aloha
finishing.com - Pine Beach, New Jersey
June 2017
![]() |
Q. Thanks for your response Ted! As you mentioned, auxiliary anodes just wouldn't be practical but designing a rack to rotate parts and avoid entrapment may be feasible. - Aberdeen, Aberdeenshire, Scotland June 22, 2017 June 22, 2017 A. Hello Jaap and Lewis! TEL - N FERRARIS - Cañuelas, Buenos Aires, Argentina |
Q. Ted and Daniel thank you very much for your responses!
Some follow up questions for Daniel:
- What would be a normal and excessive potential value?
- The supplier is varying the Soda (the same as carbonate?) concentration between 100 and 150 mg/l in order to get better results. Is the mg a typo of the supplier and should it be g/l? Why should the supplier lower it by refrigeration why is lowering to concentration by adding less soda not possible?
- I looked up "Hull Cell" but how can the supplier use this to level the bath?
Best regards,
- Hengelo, The Netherlands
June 30, 2017
Hello again, Jaap.
1. Potential: An experienced plater might recognize that the required plating voltage is higher than he is familiar with. This might indicate a faulty power supply or something wrong with the solution. But it is difficult if not impossible for a buyer to fix a plating shop's problems from a distance via book knowledge :-)
2. Carbonate in this context is not something which you add to a plating solution, but a contaminant which builds up over time. When it becomes excessive, it may be possible to temporarily drastically lower the temperature so the carbonate precipitates and can be filtered/decanted out.
3. For your purposes, a Hull Cell is a test plating cell which has the test panel cathode running at an angle to the anode, such that the test panel is close to the anode at one end of the cell and far from the anode at the other end. The result of this is that the current density is very high at one end of the test panel, and gradually declines to very low at the other end. By taking a bit of solution from your plating tank to fill the cell, then plating test panels and examining them, we learn about the condition of the plating solution: does high current density [HCF] burning occur at two low a value; does the panel fail to plate at the low current density end; what is the "bright plating range" (the maximum & minimum current density at which the plating is considered satisfactory); what if any plating problems are apparent?
Luck and Regards,
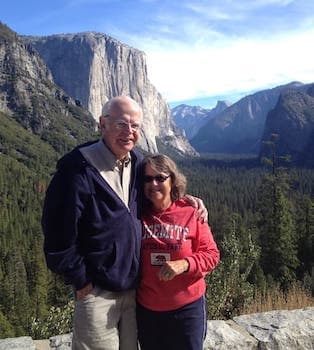
Ted Mooney, P.E. RET
Striving to live Aloha
finishing.com - Pine Beach, New Jersey
June 2017
Q, A, or Comment on THIS thread -or- Start a NEW Thread