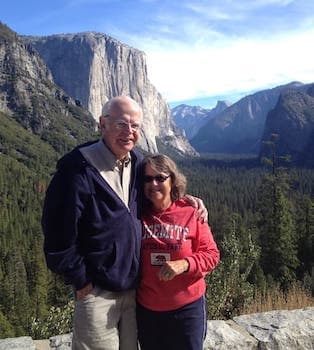
Curated with aloha by
Ted Mooney, P.E. RET
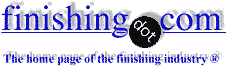
The authoritative public forum
for Metal Finishing 1989-2025
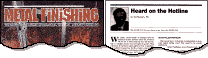
-----
Painted parts no longer offer enough corrosion prevention
May 2, 2011
Dear all
I am a painting shop technical supervisor. We specialize in producing Aluminum motorcycle parts. Now we have a problem of bad salt spray test results and I need help from all of you.
I can summarize the production process as follow :
1 - Pre painting treatment process: Spraying systems
Aluminum Parts (die cast) => buffing => Degreasing => Rinse =>
Non-Chromated conversion =>Rinse => final rinse (Hot DI Water ) => Drying
( 120'C x 30min)
2 - Painting process:
Non-chromated parts => Black color Painting (Alkyd Melamine type)
=> Baking ( 150'C x 30 min) => Finished
3- Salt spraying test process:
Painted parts => setting 24 hours => Cross cut => put in
Salt spray test machine 48 hours => Adhesion test =>Max corrosion
length check >2.0 mm = > Evaluation NG
NaCl solution :5% ; Test chamber temp : 35'C ;
Air saturator temp : 48'C ; Volume of spray solution : 2ml/ h for 80cm2
; pH : 6.5 - 7.2
Previously when we used the Chromate Cr 6+ for pretreatment , the SST
result is OK ( Max corrosion length is 1.0 mm)
Now we have to change the Non-chromate for pretreatment due to the
environment rule requirement.
So the SST result become worse.
I know that apply more wash primer prior to Black paint can improve the
Salt spraying test . But we cannot use due to the cost increase & spraying
booth design is not available for primer spraying.
I hope to receive the good recommendation from all of you.
Thanks & Best regards!
Car restorer, painting shop - Hanoi, Vietnam
May 6, 2011
Dear Sir,
What were the specifics of your original Cr6 System?
Did you use hot DI final rinse and Hi Temp dry-off?
I ask these questions to eliminate possible extraneous problems from the very real probability that your replacement pre-treat simply does not "cut the mustard" performance-wise against Cr6.
Please advise.
Regards,
Bill
Trainer - Salamander Bay, Australia
I think William is correct in his analysis that the new pretreatment is not working. Try evaluating zirconium phosphate or a dipping version of a wash primer (one pack).
Formulation almost the same as a two pack but the zinc chromate is substituted by zinc phosphate and the phos acid is incorporated into the material at mf stage. Solvent blend try 4/1 butanol/Xylene
⇦ this on
eBay
or
Amazon [affil links] . If you require more salt resistance later on you may need a better black coating - say a water based black polyester.
Birmingham, United Kingdom
May 6, 2011
May 9, 2011
Dear Mr. William Doherty,
Thank you for spending your time to my issues.
Now I would like to answer your questions as follow :
1 - We are still using the Chromate Cr 6+ of Parkerizing chemical
We apply the final rinse of hot DI water (60° C) & dry off at 120 °C x 30 minutes before painting
2 - I understand that you are afraid of contamination come from Chromate Cr 6+ to Non-chromate new build up system due to tank cleaning is not so carefully.
I think that you should ignore this situation because of we are now on Non-chromate testing process and we did not decide for mass production
The bad SST result of Non-chromate chemical is the laboratory testing results and all the parameter we keep in specification very carefully.
Please let me know if you have any question for helping me to solve this issues
Thanks & Best regards!
- Hanoi, Vietnam
May 11, 2011
I guess my questions were related to whether your process may be not allowing your Pre-treat to operate as it should.
Personally I would think that a heated DI rinse would tend to wash off the pre-treat more than may be desirable. After all, a typical Cr6 pretreat would still be gelatinous when removed from that process.
Also a dry time and temperature of 30 mins at 120 degrees C could destroy the pre-treat film of a typical Cr6 Pre-treat.
Why do you not try a cold or ambient DI final rinse and then a low temp <60 degrees C dry off with high air flow.
In other words give the pre-treat a fighting chance of survival.
That said, I have yet to see a pre-treat other than Cr6 which will survive a scribe followed by salt spray.
It is the "self healing" property of Cr6 that everything else seems to miss out on.
Hope this helps and I would be delighted to be corrected.
Regards,
Bill
Trainer - Salamander Bay, Australia
May 12, 2011
Dear Mr. Terry Hickling,
Thank you for your consideration for my problem
As your suggestion, we have already check the Zirconium content of Non chromate treated Aluminum part.
Zr content on Al test panel : 45 mg/m2
Zr content on Al parts : 50 - 60 mg/m2
Zr content Standard : min 30 mg/m2
Now we only concentrate on finding out the good Non-chromate chemical in order to solve the worse salt spray test with out primer paint more.
We will consider to apply primer only if the Non chromate chemical is impossible for good 48 hours SST
Thanks & Best regards!
- Hanoi, Vietnam
May 13, 2011
Dear Mr. William Doherty,
I will try follow your recommendation with our Non chromate chemical :
1 - Final rinse : DI Water at room temp (~30'C)
2 - Dry off : Down to 60'C x 30 min
Through your letter, I understand that we now face the very difficult issues of improving the SST result with only Non chromate conversion chemicals.
(With Cr6+ chemical the SST result is OK ).
Is that right. Sir?
Thanks & Best regards!
- Hanoi, Vietnam
May 17, 2011
Dear Thang,
My experience is that the non Cr6 alternatives can provide very good results provided that the surface is intact.
Cr6 has the advantage that it performs far better than the Non Chrome alternatives when the product is damaged.
Your SST has, of course, an initial scribe which essentially duplicates damage.
I would approach your Chemical supplier and ask for a direct comparison of SST performance.
That said, I would be very interested to hear how your process performs with cool DI and low temp dry-off.
Hope this helps
Bill
Trainer - Salamander Bay, Australia
Q, A, or Comment on THIS thread -or- Start a NEW Thread