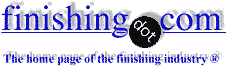
-----
Material handling in Galvanizing
We galvanize steel frames (transmission towers) in batches of 20-30 pieces. During the processes like degreasing, pickling, fluxing we use small steel chains to separate the pieces, so that the process chemicals are passing through every piece. We don't use these steel chains for any other purpose and it is found that it is costly for us to use such a material. Is there any alternate. The purpose the alternative should serve is to separate the pieces in the batch for effective degreasing, pickling and rinsing. We load the piece in a bin like tray.
Thanks in Advance
University student - Ahmedabad
May 3, 2011
May 3, 2011
Sir:
Steel Wire.
Regards,
Galvanizing Consultant - Hot Springs, South Dakota, USA
First of two simultaneous responses -- May 4, 2011
You imply (but don't state) that you suspend materials in degreaser, acid etc. differently than in molten zinc.
If that is true, why do you do that?
This creates extra work arranging material to be dipped in tanks in 2 different ways.
Why not hang it once, and take it through all dip processes to the end?
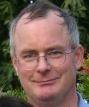
Geoff Crowley
Crithwood Ltd.
Westfield, Scotland, UK
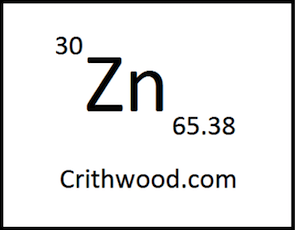
Second of two simultaneous responses -- May 5, 2011
Thanks for giving a reply so quickly
We believe that we have a huge opportunity in cost saving in the non value adding indirect material. Hence I want to know more in detail Sir.
What is the thickness of steel wire would you recommend?
The reason we use steel chains over steel wires are because if the higher thickness of chains. they facilitate the movement of process chemical between the pieces in a batch of 20-30. Thanks in advance
- Ahmedabad, Gujarat, India
First of two simultaneous responses -- May 6, 2011
Hand each piece on a wire tied to a crane carried lifting beam and other end to the piece of work. If hung vertically, one wire per piece, if hung horizontally (about 30 degrees to horizontal due to being longer than the zinc is deep), then a wire each end.
Wire size depends on weight of steel piece, use normal engineering principles to calculate wire diameter.
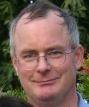
Geoff Crowley
Crithwood Ltd.
Westfield, Scotland, UK
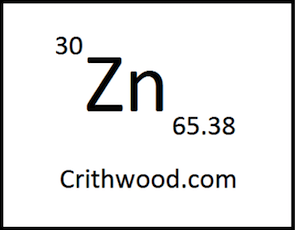
Hi Geoff
What you have said is true that it increase material handling and also lead time but the reason we do that is
1) the hanger used in the zinc kettle stage is costlier and the life of it drastically reduces when you pass it through the process chemicals like pickling etc.
2) the consumption of zinc increases because there is repeated coating of zinc in the hanger if it is passed through process chemicals.
Anyway, we are planning to shift back to what you said (using same hanger for both the stages) but before that we want to find out of the trade off in terms of monetary value between using chain (or substitutes) and same hanger for both stages.
- Ahmedabad
Second of two simultaneous responses -- May 7, 2011
May 10, 2011
Dear Raghul,
The hanger does not go into the chemicals, only the steel wire does. Steel wires are used to hang your item from the hanger, and they are spaced appropriately to avoid items sticking to each other. Be careful when selecting wire sizes, as the wires might be weakened during processes.
You can do your own monetary value comparison by comparing the zinc pick up on chains, wires and your tray. Wires should have the least surface area and therefore the least zinc pick up. You should also take into account the extra manpower needed and the cost of material. In my case, wire gives the best result, giving a 50% savings when compared with tray.
Regards,
- Selangor, Malaysia
May 19, 2011
Dear sir,
In India people generally are not using Dryer for drying the materials, they are using a kind of hot plate where they have to spread the materials to dry. . . and on dryness it hangs to another frame for dipping.
If they use same jigs from start to finish they have to hang the materials in drier or they have to heat up flux up to 65 to 70 deg. C. so when they take out the materials from flux tank, it will dry and then they dip the materials in Galva. tank.
Cost of heating of flux as well as consumption of flux will increase if they heat it up .. that's why they are adopting system like up to hot plate area they dip the materials in bunch and then spread it on hot plate and hang it again in separate jig for dipping into kettle.. cost of wire if they use will cost them more and margin of profit is very less to maintain such a cost.
Gunatit Builders

Manjalpur, Vadodara, Gujarat
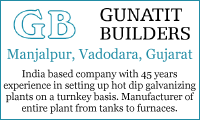
May 19, 2011
Sir:
I do not like a hot plate. It costs just as much to heat a hot plate as it does a flux tank that has a suds layer to retain heat.
The flux usage is lower for a hot flux solution than for a cold flux and hot plate.
Regards,
Galvanizing Consultant - Hot Springs, South Dakota, USA
Q, A, or Comment on THIS thread -or- Start a NEW Thread