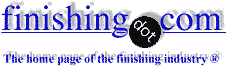
-----
Zinc cobalt plating failing salt spray test
Dear Sir,
We have problem of salt spray testing of zinc-cobalt plating. Generally we will get 240 hrs of passing over aluminium with mid phos E Nickel as undercoat. With cobalt 1.2 g/l.
But now we find that it will show white corrosion within 24 hrs. with same parameters, with oven test at 150 for 30 min.
But if we do not heat the component prior to testing it will pass 96 hrs. (till date o.k. component without white rust).
What is reason can you please explain?
Thanks,
Manager Plating - Pune, Maharastra, India
April 10, 2011
Hi, Khamlesh.
Mid-phos electroless nickel has excellent corrosion resistance, and all that you are actually testing here is the resistance to white rusting of the top layer of zinc-cobalt plating, not the electroless nickel.
Presumably the zinc-cobalt plating is chromate conversion coated, and the chromate will not withstand baking (is this 150° C or 150° F?)
If the salt spray resistance without baking has dropped from 240 hours to 96 hours, have you made any changes in the chromate conversion coating?
Regards,
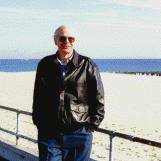
Ted Mooney, P.E.
Striving to live Aloha
finishing.com - Pine Beach, New Jersey
April , 2011
Hello Mr Bhat,
The Zinc Cobalt process - presumably you are using an Acid based process has very poor corrosion resistance to white rust but however works well on red rust. You would be better placed with an Alkaline Cobalt process.
Obviously the 150 Degree baking test is finishing off whatever chromate that is being used presently. You need to look for a better chromate that NEEDS baking to be the final step after passivation and is used Hot if you want to achieve more than 96 hours.
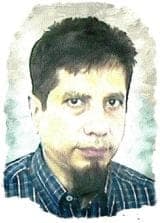
Khozem Vahaanwala
Saify Ind

Bengaluru, Karnataka, India
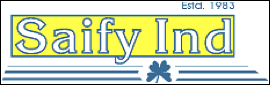
April 29, 2011
You can try out trivalent passivates with or without top coat if conductivity is not a issue for you.
S.V. Aurobindplating process supplier - Bangalore, India
May 17, 2011
July 9, 2011
Dear Mr Bhat,
there is a great possibility for your problem to come from the passivate or the Zn/Co because they always work "hand in hand". I would suggest some cross tests in making a new passivate (keeping the same Zn parameters) and see if you notice some improvement.
if so, which is likely what should be seen, it meant your passivate was polluted or needed to be dumped. on the other hand, if your corrosion result is always 24 hr, then take a look at the Zn/Co (check the Co%, metallic pollution or maybe some residual current at the end of the plating time which could change the structure and so the reactivity of the passivate...
good luck
- Normandy, France
Q, A, or Comment on THIS thread -or- Start a NEW Thread