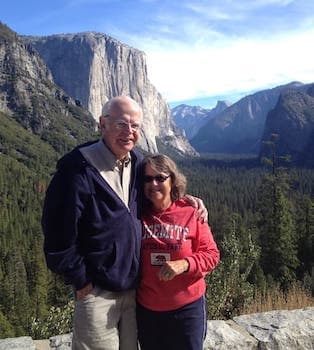
Curated with aloha by
Ted Mooney, P.E. RET
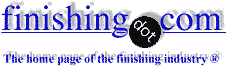
The authoritative public forum
for Metal Finishing 1989-2025
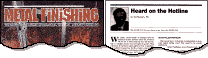
-----
Criteria to decide if component passed or failed Salt Spray Test
Q. I am having some difficulties in determining the conclusion from a salt spray test.
Is there any guideline to determine the acceptance of the rusty area? Such as location of the rusty area from edges or holes. Also have a hard time to determine the acceptance criteria for screw where the area is very small and there is much knurling and threading at screw.
Please help
QA Manager - Bayan Lepas, Penang, Malaysia
April 11, 2011
A. Hi, Husri.
Usually components are plated or processed per a recognized specification and that specification often contains its own rules for how to determine whether a component passed the salt spray test. Look at the specification you are plating this hardware to -- that is the first place to look for the acceptance criteria. Good luck.
Regards,
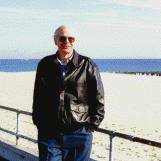
Ted Mooney, P.E.
Striving to live Aloha
finishing.com - Pine Beach, New Jersey
April 12, 2011
April 12, 2011
Q. Thanks Ted.
I am looking more on the guideline to determine if the rust occurs. Has there be a guideline which is widely used to determine which surface to be look at and which should not when looking at the rust area.
Example:
Rust to be inspected 1 mm from the cutting edges
Not to check on the hole area
Not to check at indentation area
Not to check at groove area
I am also in particularly looking on how to inspect the bolt, nut and screw for rust. Any idea what surface/area that one needs to look at. Thanks.
- Penang, Malaysia
A. Hi again Husri. Tell us the plating specification please! You continue with the assumption that all plating and metal finishing salt spray performance is evaluated per some non-specified but generally accepted parameters; you might be correct, but I do not think so.
Regards,
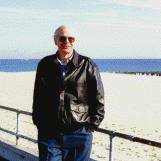
Ted Mooney, P.E.
Striving to live Aloha
finishing.com - Pine Beach, New Jersey
A. Dear Husri,
Maybe you can refer to ASTM B117 and ISO 9227.
Regards,
- Selangor, Malaysia
April 12, 2011
A. Hi CS. I don't think so. ASTM B117 tells you how to run a salt spray test, but not how to evaluate the result.
Regards,
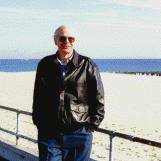
Ted Mooney, P.E.
Striving to live Aloha
finishing.com - Pine Beach, New Jersey
October 2016
Q. Dear
We have observed problem of black spots on threaded portion of bolt after 36 hours of salt spray testing. Is this a failure? What exactly can be considered as a failed fastener (bolt) as far as salt spray is considered?
Engineer - Noida, U.P., India
November 5, 2011
A. Hi, Rajesh.
Although the salt-spray testing specification doesn't describe what constitutes passing or failing, the bolts were presumably plated to some particular plating specification. That specification often includes the evaluation criteria to decide whether the parts passed testing or not. We appended your posting to a similar thread, so please look at the previous answers. Good luck.
Regards,
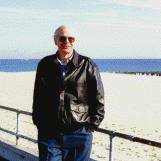
Ted Mooney, P.E.
Striving to live Aloha
finishing.com - Pine Beach, New Jersey
November 8, 2011
Q. Hi,I want to know about acceptance criteria used in Salt spray test. Whether red rust & white rust considered in welding area of coated part?
Manoj Jadhav- Pune, Maharashtra, India
October 16, 2016
? Hi Manoj,
Difficult to answer your question as you have not given us enough details. Are you a specifier (deciding what you want for a pass/fail criterion) or a supplier of plated products or maybe a customer of plated parts that are illustrating corrosion issues?
I would guess you are a zinc plater or specifying zinc plate and want to understand the validity of corrosion appearing on plated welded joints. Of course this is purely conjecture as more detail is needed.
Aerospace - Yeovil, Somerset, UK
October 17, 2016
October 21, 2016
A. Salutations,
This is regarding the usage of ASTM standards for evaluation of corrosion resistance.
ASTM B117 is a common standard to perform the test, but the evaluation of plating normally requires another ASTM standard.
For example, ASTM F1941/F1941M-16 helps specify where you should evaluate white / red rust (such as the top of a bolt, side of a nut, etc) after a set number of hours based on the coating type (zinc, zinc nickel, etc) and thickness.
Another example would be ASTM B633 which describes how electrodeposited zinc on iron / steel should last based on thickness of zinc (i.e. service condition) and type of supplemental coating and is generally used for things larger than fasteners such as brackets or sheets. (There are other standards for Zinc - Nickel, Electroplated Nickel, and would recommend consulting your supplier)
Will do what I can to answer any follow up questions regarding validation of plating / organic coatings using ASTM B117.
Cheers
- Buffalo Grove, Illinois, USA
Q. According to ASTM B633, part is deemed acceptable if the white rust is 6mm or less from the edges from the edges of the specimen at the end of salt spray testing. But, my specimen is a M6 X 12 mm flange bolt. Looking at the specimen after testing, the white rust is less than 6 mm from the edges. Can the part be accepted?
Al Fauzi- Johor, Malaysia
November 29, 2018
A. Hi Al,
You should talk with your client so he (with some technical basis) can say what is acceptable. We had some clients who didn't accept any rust after the SST, and some who accepted up to 5% rust (but no more) at the end of the test.
In small parts it is difficult to make an acceptance criteria, but it should be written in some technical document.
Best of luck!
TEL - N FERRARIS - Cañuelas, Buenos Aires, Argentina
December 4, 2018
A. Hello,
On my opinion we should have two different approaches: one for standard test specimens/panels and another for any particular part/detail we want to test.
Generally speaking, the type and number of test specimens to be used, as well as the criteria for the evaluation of the test results, shall be defined in the specification covering the plating process or shall be agreed upon between the purchaser and the finisher.
If you use panels as test specimens, as requested in most specs, the cut edges/holes/etc. should be masked. The panels usually are 100 mm x 150 mm or 75 mm x 250 mm, so masking of 6 mm from the edges should not be a problem.
If your customer want you to use actual parts as test specimens, he must to define how to prepare the part for the test (mask or not, position of the part during the test, etc.) and how to evaluate the test results.
Also see ASTM D1654 Standard Test Method for Evaluation of Painted or Coated Specimens Subjected to Corrosive Environments.
- Lod, Israel
December 26, 2018
A. Recently we had some powdered metal parts the were impregnated with plastic (the powdered metal is very porous). The suppliers plating vendor is supposedly an expert at plating powdered metal parts. After 96 hours of salt spray, we specify zinc and a yellow Trivalent conversion coating to ASTM B633 Type II. The samples came back from Salt Spray and were covered with white corrosion. I asked the lab that ran the tests what the pass/fail criteria was. They explained that most customers have their own criteria, of course we do not. I went back to ASTM B633 and found this:
"7.4 Corrosion Resistance—Zinc coatings with Types II and III treatments shall show neither corrosion products of zinc nor basis metal corrosion products at the end of the test period, as shown below, when tested by continuous exposure to salt spray in accordance with 10.3. The appearance of corrosion products visible to the unaided eye at normal reading distance shall be cause for rejection except that white corrosion products at the edges of specimens shall not constitute failure.
Corrosion Resistance Requirements
Types Test Period, hr
II 96
III 12"
- Weymouth, Massachusetts
June 27, 2019
Q, A, or Comment on THIS thread -or- Start a NEW Thread