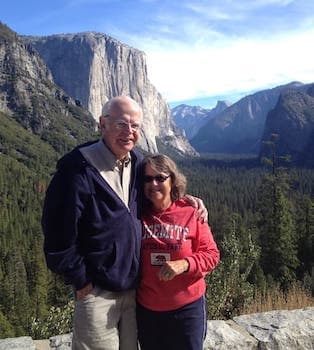
Curated with aloha by
Ted Mooney, P.E. RET
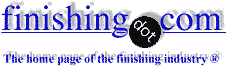
The authoritative public forum
for Metal Finishing 1989-2025
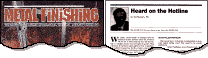
-----
Copper flash directly on 302 Stainless?
March 29, 2011
We make an electrically conductive product made from UNS 30200 stainless steel spring wire, cold drawn, Class 1, bright finish, type 302 to ASTM A313. It is used as a lamp contact.
Customer specifies the following plating:
Electrodeposited Copper flash per MIL-C-14550 (is now ASTM B734), followed by
Electrodeposited Nickel flash per QQ-N-290 (is now AMSQQN290), followed by
Electrodeposited Siver plating, Type II, Grade A per QQ-A-365 (is now ASTM B700) 200 - 300 microinches thick, followed by
Electrodeposited Gold plating, Type I, Grade C, Class I (50 microinches thick) per MIL-G-45204.
Our plating vendor - who has plated these springs numerous times in the past - deviated from the customer process by always beginning with a Wood's Nickel strike prior to the Copper flash, and omits the Nickel flash between the Copper flash and Silver plate. Their explanation for the deviation goes like this --
"The Wood's Nickel strike is necessary for optimum (or 'best practice') Copper adhesion. The Nickel flash is omitted between the Copper flash and Silver plate because it is unnecessary" -- (the inference being that it is not a value-added process) though they will do it if we squawk.
Given all this, I have a 2-part question:
1. Is the Woods Nickel strike prior to Copper flash necessary (i.e. essential) or is it an industry preference? and
2. Is the Nickel flash between Copper flash and Silver plate purposeful and, if so, what is the purpose?
Thank you immensely for insights...
Quality Manager - Tualatin, Oregon
Hi, Kelly. Generally no one should deviate from a specification, both because they do not know why the design team specified what they specified, and because such practice makes it impossible to properly track performance in the field. Suppose you start having 20% field failures; nobody can even guess why if we don't know which parts were plated with what. On the other hand, a plating shop frequently knows things that the design team doesn't know, and they should not apply a plating sequence which they feel will not work.
So, to the extent that the answers are used to get the spec changed, your technical questions are valid ones. But answers to your questions that justify the plating shop not following specs won't do anyone any good :-)
That said, the wood's nickel strike will probably prove necessary for proper adhesion because few other platings will adhere to stainless; and the nickel between the copper and silver is probably not necessary because it's most likely function is as a diffusion barrier; and if the temperature and time frame allow problematic diffusion, it will probably occur between the gold and the silver as much as between the silver and the copper. Just an opinion -- hopefully your question will draw additional ones.
Regards,
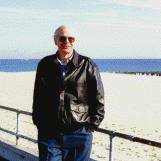
Ted Mooney, P.E.
Striving to live Aloha
finishing.com - Pine Beach, New Jersey
March 31, 2011
Thanks Ted, your points regarding our vendor deviating from specs are valid. We (they and I) have already gone around and around about that.
I'm trying to educate myself for the sole intent of going back to our Customer to present a case for having their spec changed IF WARRANTED. It's that huge 'IF WARRANTED' grey area about which I'm seeking information (even if informed opinions) from plating experts--the people who have the knowledge, training and hands-on experience doing this stuff.
Being mostly ignorant about plating, I'm in the information-gathering stage. Given that, your opinions are encouraged and welcomed. Anything I can use persuasively with Customer.
Thank you
- Tualatin, Oregon
April 1, 2011
Hi Kelly,
Aside from following customer's spec to the letter, there are times where the customer may need a little education. In my opinion, your plater has his pulse on the plating industries ' best practices '.
- Penang, Malaysia
April 4, 2011
Thank you SK, I appreciate your input!
If you don't mind, may I ask, is it possible to be more specific as to why you feel this way? Or is it just years of experience speaking?
Can you give an example or cite a similar issue in which you have been involved or know about? Can you point me toward any reference material that might elaborate?
- Tualatin, Oregon, USA
April 5, 2011
Kelly, hi.
Through the years, I've had my fair share of adhesion problems when plating on SUS. Activation of SUS by the Wood's nickel strike is essential prior to performing any type of plating. ASTM B254 ( Standard practice for preparation of and electroplating on stainless steel ) is a good reference document to start with. For SUS 302, for a high degree of adhesion, it specifically recommends a cathodic treatment in Sulfuric acid followed by a wood's nickel strike prior to plating. You can thank your plater for using the nickel strike.
As for the nickel plate between the copper and silver, ASTM B700 ( Standard specification for electrodeposited coatings of silver for engineering use ),6.3.4, state " A nickel or nickel alloy intermediate layer, at least 1 micron thick, shall be applied before the silver electroplate when the product being plated is made from copper or copper alloy. Nickel under plate are also applied for other reasons." Apparently, your substrate is SUS 302 and do not fall into this clause , although, you have a copper flash layer and the nickel flash may beneficially act as a diffusion layer as Ted suggests. On this matter, I have the same opinion as your plater, that is, I will do it if you insist (squawk). Good Luck.
- Penang, Malaysia
April 6, 2011
Thank you once again SK, your reply is enlightening. I appreciate your time in helping me understand this process.
So far Ted and SK have presented good references and experience-based conclusions. Does anyone else have differing opinions or experiences?
- Tualatin, Oregon, USA
April 7, 2011
Q, A, or Comment on THIS thread -or- Start a NEW Thread