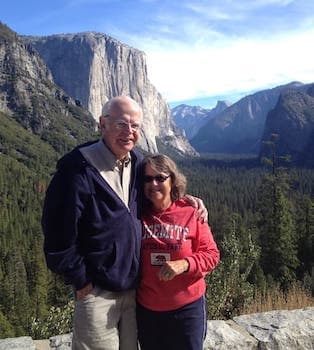
Curated with aloha by
Ted Mooney, P.E. RET
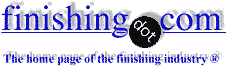
The authoritative public forum
for Metal Finishing 1989-2025
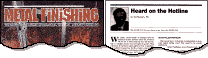
-----
Powder coating over anodising - results in pin-holes
March 21, 2011
We are a company trying to work out the best coating solution for a new sensor we are making that has to survive outside weathering including salt spray.
The basic component of the sensor is an aluminum tube with a lens at one end, electronics and wiring inside at the other with a sealing plate at the end. There is an aluminum mounting arm that is glued into the side of the tube.
For optical reasons we need the inside of the tube to be as black as possible and the outside and mounting arm preferably white and weatherproof.
One solution we have been trying is to have the entire main tube hard anodized using a black dye, then masking the inside of the tube prior to polyester powder coating the outside. Three different powder coaters have attempted this several times but the powder coating invariably is uneven and has small pinholes in the surface. They blame the anodizing finish.
So far we have tried both a standard hot water seal for the anodizing and also a nickel based seal and both are as bad. Generally the powder coaters have put the part through their standard cleaning process and then through a chromate conversion treatment as the arm is not coated at all.
We are at a loss of how to proceed. We have read anodizing is OK as an undersurface treatment for powder coating but we cannot get a good finish. From what he have read the problem is either due to the poor dispersal of charge across the insulated layer of anodizing or due to some outgassing issue. All we are left with at present is to try to mask off the entire outside surface prior to anodizing, so the powder coating goes on bare metal.
We have considered switching to a multi-stage paint process but due to the complexity and relative low volume nobody wants to do the job.
Product Designer - Loughborough, Leicestershire, United Kingdom
I would think that the sealing process is interfering with the powder coating process. Typically anodized parts to be powder coated are left unsealed. However, that may lead to degradation of the dye on the internal sections, especially if it's exposed to light.
I do think though, that your best bet is to mask the part to be powder coated from the anodizing surface, or perhaps instead of a chemical pre-treatment prior to anodizing, the powder coater could remove the anodizing by bead/sand blasting.
Also, it sounds like hard anodizing might be an overkill for this process, as it appears that there are no wear properties needed for the internal section of the tube. A thinner coat Type II anodizing would be easier to remove by a bead/sandblasting prep prior to powder coating.
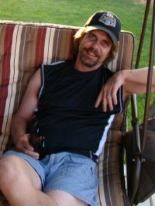
Marc Green
anodizer - Boise, Idaho
March 24, 2011
Q, A, or Comment on THIS thread -or- Start a NEW Thread