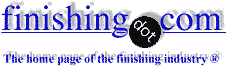
-----
Anodizing results suddenly gone south
March 3, 2011
Hello,
We have been successfully anodizing at our machine shop with great results for the past two years. All of a sudden as if someone flipped a light switch our results went down the drain. Everything we pull out of the dye tank is blotchy and light colored.
We are running:
Type II
10% sulfiric by volume
68 degree F
15 ASF
45 min ano time
The way the parts look I would suspect either small pore size, but I can't figure what is causing it, or low growth, we are getting a reading of .9 mil build. We have already replaced all of our tanks, including dye, but still yielding the same results. There has to be something that we are over looking, if anyone has any ideas on what to check it would be greatly appreciated.
Machine Shop - Janesville, Wisconsin
March 8, 2011
Wow, that's a helluva switch somebody flipped.
Things that come to mind to check:
If you've changed out all your baths trying to correct the issue, and the coating thickness is in spec... one would almost have to assume that the problem is in the dye bath, even though you've changed it.
Most dye companies will offer free analysis of your bath, send one out ASAP. Secondly, verify that all your instruments that you use for checking all bath parameters are working correctly, pH meters, temperature gauges, scales for weighing dye additions, etc...verify each one with a second, if possible.
How do the racks look that you are using to coat the parts? Are they nice and black, or are they coming out the same way? Is it just a particular part that you are having issues with? If so, verify the material certs, or run some different aluminum through there just to make sure it's not an aluminum issue.
Lastly, I'd check your make-up water...hopefully your using de-ionized water for bath make-up. Make sure your water supply is functioning adequately.
For this significant of a change, I'm really leaning towards a dye-bath issue, or faulty equipment reading issue on this..when you re-built the bath, did you use the same lot of dye? Is it, perhaps, past it's shelf life? Are all your pH calibration standards up to par, and not outdated?
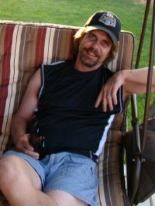
Marc Green
anodizer - Boise, Idaho
I'm using Titanium racking so I can't really judge anything based off the coloring/lack there of from that.....or can I?
We've only been running 6061, and having problems with all the part we are running.
I did forget to mention in my previous post that these parts are being run in a vibratory tub prior to anodizing. We sent a handful of parts out to another anodizing company and they said they had a hard time getting a deep black on them. Has anyone ever run into an issue with tumbled parts? We have run several hundred tumbled parts prior without issue.
As far as the dye bath, I guess I don't know for sure if it came from the same lot at they suppliers end, I ordered new when re-building. We had been using a cheap hand-held pH meter, but purchased a lower end (but still expensive for us) three point calibration meter just to verify we are within range on the pH.
Machine Shop - Janesville, Wisconsin
March 9, 2011
Dan
The appearance of the part suggests that the dyeing step is suspect as opposed to the anodize. Check your rinse tanks as well as having the dye evaluated by the mfg. If a/the rinse is contaminated, a good dye bath still won't work. Could a siphon be at work from other (rinse) tanks?
- Colorado Springs, Colorado
March 10, 2011
Be reminded that the vibratory media has to be DESIGNATED ALUMINUM ONLY, otherwise you will pound iron into the soft "Kleenex-like" aluminum and that will smear the final result. Also know that if you are racked on titanium and the dye tank is stainless you have an interfering galvanic current.
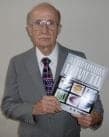
Robert H Probert
Robert H Probert Technical Services

Garner, North Carolina
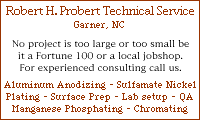
First of two simultaneous responses -- March 11, 2011
Second of two simultaneous responses -- March 11, 2011
I guess the way I'd approach this issue is as follows:
1. If you suspect it could be tumbling related, it's simple enough to anodize a non-tumbled part and compare the results.
2. Do you do other dyed work (different colors) and is that work coming out acceptable? If so, it's obviously a black dye problem.
3. Willie brings up a good point about the quality of rinse prior to dyeing, albeit it would really have to be a poor rinse to see such a dramatic change. I've always been a staunch supporter of a good DI spray rinse after a good soak rinse prior to dying. I also can't help but note that you didn't address my question as to whether you are using DI water for your bath make-up. City water can fluctuate quite a bit, especially at this time of year when a lot of cities flush their lines. If you're using regular tap water for bath make-up , that very well could be a problem.
4. How were the results from your 2nd source anodizer? I noted you said they weren't able to get a "deep black"..but obviously they weren't as poor as the results you're getting in house?
5, Being a machine shop, I would think you'd have plenty of access to multiple lots of aluminum, and could produce multiple finishes (with, and w/o tumbling). Try a bunch of different experiments (finishes/alloys/lots) in the same load, and compare results...that should point you in the right direction by using a simple process of elimination.
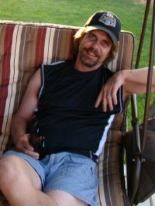
Marc Green
anodizer - Boise, Idaho
March 14, 2011
Thank you for the ideas thus far, it is greatly appreciated.
We have tried different finishes, extruded stock, freshly milled, blasted, and tumbled. All with the same results.
We have also tired different colors, black, red, olive, all with the same results.
The other source we used was able to produce a finish that was acceptable by our customer, but not ideal. If all of the parts of the assembly had been done by this company it would be fine (if they didn't leave obvious rack marks). But putting them together with the parts of the assembly we had already done, they didn't seem to look as dark.
Tumbling media is not new, but it has only seen 6061 aluminum.
I think Marc is on the right track with it being a water related issue. We are using an RO system. After talking to a maintenance worker at another company in town, he informed us that in most cases, when an RO system meets its life expectancy it's done, no warning to gradual decline in performance it's just done. That being said, we do not have any sort of monitory in place. We are looking for a new system that has monitory capabilities.
I know that this is not the "proper" way of doing things, but we have found with the process of trial and error that we can get a very nice looking finish with running at 30 asf for duration of 45 minutes. This is giving us a build layer of 1.9 mil. Like I said I know this is not the proper way of processing type II, I'm just offering this information hoping it helps uncover our issue.
- Janesville, Wiscosnin
March 15, 2011
That last post was pretty informative. Definitely eliminated several potential issues (black dye, Al stock, finish).
Obviously, however, you should not need to have almost 2 mils of coating thickness in order to get a nice black color, especially at such a high current density for a type 2 coating.
I'm now of the opinion that with that high of a current density, at 68° F, you are creating some very large pores which are able to accept the dye. Are you sure the temperature of your anodizing bath is accurate?
Also, anodizing baths with a very high dissolved aluminum content produces a product that can be difficult to rinse, which will in turn will definitely give you dyeing problems. I know you said you changed out all baths, so I'm assuming that included the anodizing tank. What is the dissolved aluminum content?
If it is indeed a high dissolved Al content, or a small pore size problem employ a dilute nitric acid soak (10% vol for 5 min or so, with a rinse afterward) prior to dying. See if that helps. If it does, I'd lean to a small pore size, or high dissolved Al content being your problem.
While not ideal, RO water should be adequate enough to produce a solid product, however I'd strongly suggest going to a DI water system, the unibeds can be adapted with meg ohm monitoring lights that let you know when they need to be changed out.
There's not a whole lot than go wrong with an RO system, especially if you employ correct pre-filtering. I've had my latest one in place for almost 8 years, and the only problem I've had was a leaking membrane canister. Ideally your incoming water flow should go as follows:
Tap water
Softener (if needed)
Carbon filter
Sediment filters
RO Treatment
DI unibeds
Storage tank that constantly recirculates through another unibed. Also employing a UV light in the loop to kill bacteria.
Water pumped from storage tank to anodizing line.
Granted, this is quite the expense, but that's how it should be done.
Ha! Now, with all that being said, and with the info provided in your latest post... I'm not convinced your issue is water related. Even if one were to make a complete anodizing line with nothing but crappy city tap water, I would STILL think you could get a lot of runs through with decent results until the contaminants in the tap water began to affect the baths.
It sounds as if that you are able to get good/acceptable results by enlarging your pore size (which you mentioned as a concern, originally)by changing your process parameters. Which, by the way, is not a good practice. If the water was a problem, I don't think that enlarging the pore size would solve the issue.
Now, what affects pore size?
Electrolyte concentration (higher concentration = larger pore size)
Electrolyte temperature (Higher temperature - larger pore size
Current density (Lower current density = larger pore size)
So I guess what I'm saying now is, that it appears to me that it could be something screwy in your anodizing tank. Either inaccurate temperature monitoring, inaccurate current control, or inaccurate bath concentration monitoring, or too much dissolved aluminum in the bath.
Problem solving is fun, is it not? :)
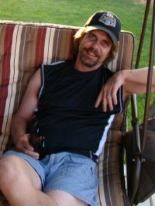
Marc Green
anodizer - Boise, Idaho
Well, problem solving can be fun, but it's less fun out on the shop floor than from a backyard lawn swing with a beer in your hand :-)
Thanks Marc.
Regards,
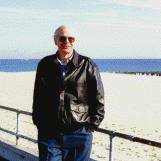
Ted Mooney, P.E.
Striving to live Aloha
finishing.com - Pine Beach, New Jersey
March 16, 2011
I've said it more than once on this forum and I'll say it again; walk the process. Start at the beginning, i.e. the purchase of the raw materials, follow the process through all of the manufacturing stages, right to the final product, make copious notes and compare the process to the original process when you were still getting good product.
It is surprising what you'll find out, from changes in cutting fluids to even slight variations in chemistry of the anodising solutions.
From the information you can garner from walking the line you can now start to eliminate potential causes of the change in the appearance of your anodising.
Aerospace - Yeovil, Somerset, UK
March 17, 2011
Q, A, or Comment on THIS thread -or- Start a NEW Thread