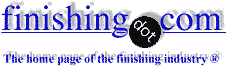
-----
Thickness of nickel plating^Substrategrows during drying
Hello, my name is Gabriel Perez, I am working as a Quality Engineer, I am new on my current company and I am focusing on a defect that has repetitive customer returns; a Copper Beryllium part plated with Nickel is being rejected for thickness out of spec.
This particular product family is processed first reducing the thickness at an acid tank from 0.0035" to 0.0020" in order to improve spring properties of the part, then is nickel plated with a thickness range of 0.0001" to 0.0003". I checked the variation at the plated parts since in the past they where measuring only after acid reduction and then adding the Nickel thickness reading to assume a total part thickness (ie: 0.0022" + 0.0003 = 0.0025"). In reality the plated part goes up to 0.0040"; when the maximum is 0.0028"; Based on this I've checked a rack without oven drying and the range at all parts, all three areas measured was: 0.0021" - 0.0025".
Based on this I am planning a trial based on the time / temperatures parameters of the oven to verify the theory. Drying process consists of air pressure application after last rinsing and then stored for something around 5 minutes at oven temperature set up of 220° F / 104° C.
As Metal Finishing experts could you please advise if I am on the right track?
Plating Quality Engineer - REYNOSA, Tamaulipas, México
March 4, 2011
Hi, Gabriel.
Sorry, but I think you are on the wrong track. The thickness of nickel plating does not grow during drying. I believe that the thickness-reducing step is not working consistently. I suggest that you cross-section one of the parts that is 0.0040 thick after plating and see how thick the substrate is versus how thick the plating is.
Plating thickness is directly proportional to the product of plating current and plating time and it cannot spontaneously quadruple in the plating tank or in the dryer. If cross-sectioning reveals that the plating thickness has quadrupled, I suspect that your plating line was stopped with current flowing to the nickel plating tank such that the plating time had quadrupled. Good luck.
Regards,
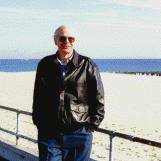
Ted Mooney, P.E.
Striving to live Aloha
finishing.com - Pine Beach, New Jersey
March 8, 2011
Thanks Mr. Mooney, but I think that the title of my inquiry did not explain correctly the problem; what I was trying to say is that the copper substrate could be the material that is being affecting due the high temperature of the oven drying; which is 220° F; I know the nickel layer has nothing to do with the increase of the thickness at the part; as a matter of fact this is one reason I believe it was not detected: thickness of part was not measured before; only the Ni thickness
Gabriel PérezPlating Quality Engineer - Reynosa, Tamaulipas, México
First of two simultaneous responses -- March 8, 2011
Hi Gabriel
How are you measuring these parts. A micrometer may indicate to tenths of a thou but the jaws will measure any peaks and/or the inevitable build up at the edges.
Also remember that the nickel plates on both sides so the increase in thickness will be twice the plating thickness.
It may help you to work in microns. All those zeros are easily confused.
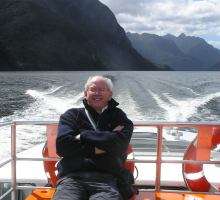
Geoff Smith
Hampshire, England
Second of two simultaneous responses -- March 9, 2011
A lot of metals will have a different size after being heat treated at a high temperature, but normally not at the temp that you are talking about. If in doubt, heat treat an unplated part in a stainless steel baggie to prevent oxidation. See how the final measurement compares to the first. Obviously, they need to be at the same temperature for the measurement.
James Watts- Navarre, Florida
First of two simultaneous responses -- March 9, 2011
Hello Mr. Smith,
I am using a micrometer and having the average after measuring at three areas, I will try to send you a picture of a bad and acceptable part with the micrometer reading; I agree that the English system is confuse; I am used to work with the metric but our drawings have those units. For reference: the thickness difference at the process variation can even seen and feel between opposite parts, therefore I dismissed a measuring system error, also in the first claim I received, what the customer reported was the same I measure when I receive the part; of course I need to explain them that thickness is not homogeneous at the whole part, but I need data and process optimization first. My first trials of a DOE shows less part thickness at less temperature at drying (with less thickness I mean inside customer specification). I am consulting the Heat and Thermodynamics theory on copper to verify if matches with this, at my first consulting I've already found the copper coefficient when is heated but I have not been able to read the whole theory to see if the coefficient is related only to the length and/or what would be the correlation with the wide (or the thickness in this case)
Thanks and my Best Regards,
Gabriel
Laird - Reynosa, Tamaulipas, México
Second of two simultaneous responses -- March 9, 2011
Q, A, or Comment on THIS thread -or- Start a NEW Thread