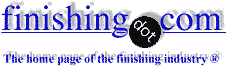
-----
Contact mark size limits for chromium plating
My question is: What is the nominal size of a contact mark for chromium plating. I have a drawing that allows a contact mark of 0.060 inch diameter. I asked the engineer if that was for one contact mark or three contact marks. He said that meant a combined area of three contacts marks, i.e., 0.020 inches diameter per contact mark.
Joseph MenkeChemist - Rock Island, Illinois
February 14, 2011
There is no nominal size. It has to be determined in terms of electric laws, process requirements and aesthetics or design guidelines (size of the parts, area to be plated, necessary current, conductivity of materials, allowable positioning, etc.). Then, it has to be agreed upon and put in the drawing, contract or PO. If the original spec violates these calculations, remember it's not "God's word". It may be wrong.
G. Marrufo-Monterrey, Mexico
Monterrey, NL, Mexico
February 26, 2011
Is there some formula for part size, area to be plated, current, conductivity, etc that can be used to to calculate/estimate what the contact size might be?
Joseph Menke- Rock Island, Illinois
March 1, 2011
I think that he is wrong! But it needs to be in the PO or similar document.
Actual size will be from experience. Location makes a huge difference and the amperage needed to plate the part is the main controlling factor.
You can approach it from a standpoint of the current capacity of the contact point. You would not use copper, but it would be 1,000 amps per sq inch of area and proportional down. 2 contacts would allow you to drop the number that you arrive at by dividing by 3. Since the solution will carry away most of the heat generated, you can probably drop that number in half. Now, it is trial and error on dummy parts.
- Navarre, Florida
First of two simultaneous responses -- March 3, 2011
The vastness of possible shapes and cross sections and difficulty to measure them, as well as the vastness of possible positioning of contact points, variations in effective conductivity, materials in contact and electrochemical process requirements make it simply too complicated to put in an equation. I don't know of a formula or program designed to do it for you. As far as I know, this is still a matter of good judgement by specialists finally verified by trial and error.
G. Marrufo-Mexico
Monterrey, NL, Mexico
Second of two simultaneous responses -- March 7, 2011
Q, A, or Comment on THIS thread -or- Start a NEW Thread