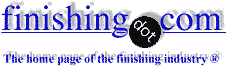
-----
PolyPro Tanks vs Stainless for a new Anodizing Line
I have seen you post many replies on finishing.com and thought I would ask for some advice from you. We are looking to install a new automated anodizing line and we are currently evaluating Polypropylene tanks versus Stainless Steel. We will have bright dip as that is a current option we offer and we will also have a high performance seal and color options. We have been told that there is a Euro Grey Polypro tank that can withstand constant 230 degree temps with no degradation. I know that Stainless is more expensive but we are looking for a system that will last 15+ years.
Any insight you can offer would be very helpful. Another item we are considering is 26 foot long tanks to handle long parts. Would this have any effect on the polypro tanks? Also, do you recommend having covers over the tanks to retain heat?
engineer - Nashville, Tennessee
February 10, 2011
Hi, Bryant. With the exception of the bright dip tank, polypropylene should be fine. Remember that it is flammable, and take every precaution against fire. I was an insurance company investigator for plating shop fires and I'm having trouble thinking of a single fire that did not start in a polypropylene tank. 26 foot long tanks should be no problem as long as they are properly braced (usually with stainless steel tubing, or steel tubing enclosed in poly).
I am not personally familiar with that brand or type of polypropylene, though, and I am not familiar with the use of any other tank material than 316L for bright dip solutions (and strongly recommend double wall tanks if you use 316L). If a high temperature polypropylene would work, that sounds like a great alternative though. Bright dip solutions are very powerful oxidizers, so I doubt that polypropylene could last 15 years even if successful at first. But you could probably build 3 or 4 single wall polypropylene replacement tanks for the cost of one double-wall 316L tank :-)
Good luck.
Regards,
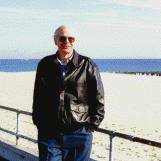
Ted Mooney, P.E.
Striving to live Aloha
finishing.com - Pine Beach, New Jersey
February 9, 2011
Hello, Bryant. You have received some incorrect information. Euro grey polypropylene is not any more resistant to heat than white, natural or black polypropylene and should not normally be considered for hot solutions above 180 F. Euro gray just has a pigment to give it that particular color. A modern and complete anodizing line will likely have both polyproplyene and stainless tanks. Careful consideration must be given on a tank-by-tank basis. As to your second question about tank length, polypropylene does not pose any particular problems as long as it is structurally engineered with proper external support. As to your third question, tank covers can be a significant front-end investment but can have very favorable payback periods in energy savings. We crunch the numbers for our customers in order to help them decide which way to go. Let me know if we can be of any assistance.
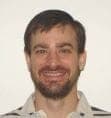
Jon Barrows, MSF, EHSSC
Kansas City
February 14, 2011
Hi Bryant.
That's true; polypropylene is the better solution for process tank but as I know maximum withstand temp capacity of polypropylene is not more then 110° C. Pl. check with polypropylene sheet manufacturer and then you decide for the same.
Gunatit Builders

Manjalpur, Vadodara, Gujarat
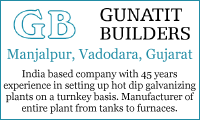
March 21, 2011
As a correction/addendum to my previous post, there is one polypropylene sheet manufacturer that has a modified euro grey PP with a proprietary temperature resistant additive. The manufacturer rates the material at 230° F rather than the typical 180° F. As a caution though, these ratings are just for the sheet and do not take into account that the end use is a welded rectangular tank that will contain hot chemicals under hydrostatic pressure. A good tank designer needs to make the necessary temperature corrections for the permissible stress and the creep modulus. In the final analysis, a high-temp polypropylene tank might be possible, but it may not be the best choice.
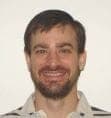
Jon Barrows, MSF, EHSSC
Kansas City
March 21, 2011
I like Jon's revision. I would question if that material is available as weld rod and what certification is required of the welding operator to assure that the weld is as good as the parent material. It will obviously take a higher temperature and heat for a good weld. I will speculate that it will be quite possible to use too much heat/temp.
I did a good bit of plastic welding in the distant past and thought that I was a good welder. BUT, there were some jobs that were not as good as most.
- Navarre, Florida
March 22, 2011
I am with Jon's idea.. and in India, we are using P.P. sheet Pickling tanks and especially for flux heating tank where we are going up to 70° C. temp maximum; and manufacturer confident with sheet that it will withstand up to 110 ° C or 230 ° F. And we have same welding rod to weld the materials.
I think P.P is the best solution for Chemical process tanks.
Gunatit Builders

Manjalpur, Vadodara, Gujarat
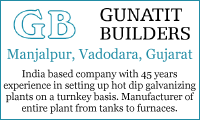
March 31, 2011
How do you plan to brace a tank that is 26' long. It has a coefficient of expansion that is about 10 times that of steel. Properly braced for the high temp will have virtually no support for a cold tank. That is a lot to risk. Thick material and PP bracing (lots of it) may work.
James Watts- Navarre, Florida
March 31, 2011
Hi, again.
Although I'm not as concerned as James about bracing the tank, I am concerned about "high temperature additives" to the polypropylene. I was involved in the design of a set of polypropylene tanks once where he had brominated fire retardants added to the resin as a guard against fire. While we were able to successfully leach most of the tanks for their low temperature and low concentration use, the electroless nickel tank actually had to be thrown away. I'm not saying that the situation is the same, just that caution is needed when dealing with miracle ingredients.
Regards,
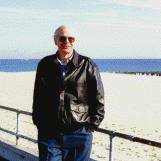
Ted Mooney, P.E.
Striving to live Aloha
finishing.com - Pine Beach, New Jersey
April 1, 2011
I just wanted to say thanks to everyone that has supplied feedback. We are still working on this project and have changed the design to 10' long tank. I still have concerns over the longevity of PP for the high temp tanks and think that even though it is a higher up front cost, the higher temp tanks only comprise about 1/3 of the total number of tanks and believe eliminating the risk by using Stainless is the best option for these high temp tanks.
If anyone else has further suggestions or comments I appreciate hearing them.
- Murfreesboro, Tennessee, USA
November 21, 2011
Q, A, or Comment on THIS thread -or- Start a NEW Thread