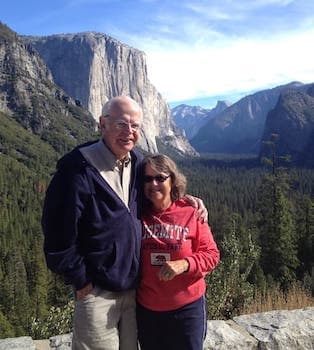
Curated with aloha by
Ted Mooney, P.E. RET
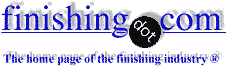
The authoritative public forum
for Metal Finishing 1989-2025
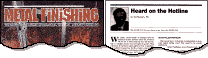
-----
White rust in zinc plating on forged steel
Dear folks,
We got a new part for zinc plating, but this part is forged steel. After we kept the part for several days there is some white rust appearing, but if we wipe the white powder the chromate is still OK only one small spot is left.
Our customer's flow process are forging, shot blasting, machining. Our process is first barrel cleaning (degreasing, pickling, anti rust by degreasing) than rack plating (degreasing, anodic cleaning 3 A/dm2, cathodic cleaning 3 A/dm2, pickling, anodic cleaning 3 A/dm2, activation, alkaline zinc plating, activation, black chromating, spraying, drying).
When we check the part under cross section microscopy we found some holes/pits in material under the rust. What is possible cause of this white rust?
And how can we get good result for carburized ones with the plating sequence as above?
Thanks for your kind reply.
plating shop employee - Bekasi, West Java, Indonesia
February 5, 2011
Hi, Mr. Joko,
I think the pin hole from your parts is trapping chemicals.
So you need good pretreatment and correct flow of processes to get rid of the trapped chemicals that causing white rust on your parts.
Please contact your plating chemicals expert and have some trial with them.
Good luck.
Best regards,
- Jakarta, Indonesia
February 21, 2011
February 26, 2011
Dear Joko,
I believe you are doing alkaline Zinc plating on casting. It is advisable to plate acid chloride Zinc plating. This is because of the unique leveling property of this bath. Zinc ions from this high efficiency bath, in the first few moments of plating 'jump over' and try to cover maximum smaller pores.Then gradually plates all over.
Take care in the pre- treatment cycle. Dip more time in the pre plating dip tank. If possible have powerful air agitation applied in this tank with an intention that this will facilitate to drain whatever solution is trapped in the pore.
Best of luck.
Regards
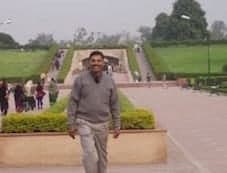
T.K. Mohan
plating process supplier - Mumbai, India
Q, A, or Comment on THIS thread -or- Start a NEW Thread