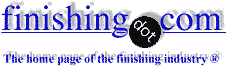
-----
Treatment for a Carbon Steel bolt in acid service
I have an application that uses a 1/2-13 x 4.5" flat head socket cap screw. Because it screws into a stainless steel fixture and is exposed to some heat (212F max), we use a carbon steel bolt and apply never seize to the threaded portion of the screw to prevent galling. The head and non-threaded shaft portion of the bolt are exposed to the process side which includes some material containing a nitric acid solution. Also, the fixture rotates such that the head of the bolt with the socket is exposed to abrasive material for extended periods. We typically leave the bolts in place for 1-2 weeks, during which corrosion can occur and start to eat away at the head of the bolt depending on the acid concentration in the material. We then discard the bolt and replace with a new one. When we do not stay on top of it, we have broken the heads on the screws due during removal attempts. When the acid concentration is high, we have seen significant corrosion in <24 hours.
My question is if you think chrome plating (or any other treatment) may be a good choice for this application. A thin coating (flash chrome?) would probably be better but I am concerned about it wearing off on the head that is exposed to the abrasive material. So some experimentation may be needed. I am also wondering if just chroming the unthreaded portion of the bolt is an option since the never seize protects the threaded part.
R&D Engineer - Mobile, Alabama, USA
February 3, 2011
Have you tried titanium bolts?
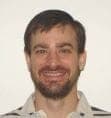
Jon Barrows, MSF, EHSSC
Kansas City
First of three simultaneous responses -- February 4, 2011
Have you considered a stainless steel screw? There are little chances any conventional (inexpensive) coating or plating will survive in such environment. Remember that not only is the fixture in risk. Also the substance in contact with the screw is getting contaminated with dissolved iron. G. Marrufo-Mexico
Guillermo MarrufoMonterrey, NL, Mexico
Second of three simultaneous responses -- February 4, 2011
Is there a reason why you are not using a stainless steel fastener? Chrome plating is not going to fix the problem of exposing a carbon steel fastener to nitric acid.
Toby PadfieldAutomotive component & module supplier - Michigan, USA
Third of three simultaneous responses -- February 5, 2011
Thanks for the responses. We are using a carbon steel bolt at the request of the person who made the stainless fixture that is in contact with the dilute acid solution. His background is as a tool and die maker and he indicated that galling would likely result if we used a stainless screw. His instructions were to discard the screw and replace with a new one on a routine basis which we follow but I was thinking we could get some more assurance if we flash chromed the part. I wanted to stay away from using a hard to source screw. Basically, I'm not looking for the coating to last for a long time (maybe 1 week) but just want some insurance. If the prevailing belief is that galling will not be an issue then I am willing to try a stainless screw as well.
Alan Bussard- Mobile, Alabama, USA
February 10, 2011
My opinion is that stainless with an anti galling or antiseize would be far less of a problem than trying to remove a badly corroded bolt. I know, he is worried about the part, not the screw/bolt. Just do not use a 400 series bolt.
A chrome flash will extend the bolt fail rate some- on most but not all bolts.
Titanium bolts as Jon suggested are not that hard to source.
- Navarre, Florida
February 11, 2011
Chromium plating has pores and cracks and will not provide protection. Titanium is an excellent suggestion, But I would recommend a stainless bolt of a different alloy than the fixture. For example, if the fixture is 304, you could use a bolt made of 316SS or alloy 20.
Lyle Kirman
consultant - Cleveland Heights, Ohio
First of two simultaneous responses -- February 14, 2011
Galling is always a concern when using stainless steel fasteners, but it can be mitigated. There are a number of thread lubricants specifically formulated for stainless steel fasteners, e.g. FASTORQ°Š A/G, which should allow satisfactory tightening of the joint given good quality threads (low surface roughness, accurate thread pitch, etc.), good dimensional control of the mating members, and a suitable tightening procedure. Google "stainless steel thread lubricant" for some additional information. Using a coated carbon steel bolt is not an appropriate solution, in my opinion.
Toby PadfieldAutomotive component & module supplier - Michigan, USA
Second of two simultaneous responses -- February 14, 2011
Have you considered using a stainless steel bolt with a zirconium nitride (ZrN) PVD coating? The coating will prevent galling. ZrN is much like titanium nitride (TiN), but a bit harder and more chemical resistant.
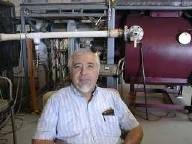
Jim Treglio - scwineryreview.com
PVD Consultant & Wine Lover
San Diego, California
February 16, 2011
Q, A, or Comment on THIS thread -or- Start a NEW Thread