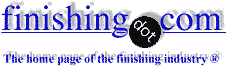
-----
Test Method to Test Electroless Nickel and Zinc with Chromate Passivation Corrosion Resistance
We currently use both EN and Zinc with Clear and Yellow Chromate Passivation to plate our steel parts. There have been questions posed to me on which provides the better corrosion resistance - our products are used indoors in a controlled atmosphere, but some see "high humidity" due to cooling and heating resulting in the machine sweating. I'm at a loss to provide an answer as both provide corrosion protection plus other benefits from the plating in the application used.
Is there data that is available without reinventing the wheel to compare EN and Zn+CRIII passivation for corrosion resistance based on test criteria? If both where put through salt spray for 100 hours, would the zinc fare better or the EN? The plating thicknesses and passivation thickness are driving forces in how well the plate would perform during testing, but I can spend the rest of my career doing testing to provide an answer, but I'm hoping the experts can guide me to an applicable test for testing both materials under the same/appropriate conditions to provide a response.
Thank-you for your assistance.
Manufacturing Eng., working on a plating project - Ann Arbor, Michigan, USA
February 1, 2011
Hi, Janice. The electroless nickel will win the salt spray contest and will cost much more, but that's not really the answer. The difference is that electroless nickel plating is "barrier layer" plating whereas the zinc plating is "sacrificial" plating.
If nothing will wear away or scratch through the electroless plating, so that the "barrier" is unbroken, it is fine. But once the underlying steel is exposed, the EN does nothing to protect it; in fact, it actually accelerates the corrosion of the steel.
The zinc plating is sacrificial. Even if scratched, it protects the underlying steel the same way that zinc anodes protect the steel hull of a ship. Good luck.
Regards,
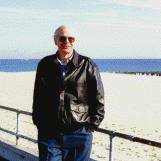
Ted Mooney, P.E.
Striving to live Aloha
finishing.com - Pine Beach, New Jersey
February 2, 2011
Hi Janice,
Further to Ted's comments, the problem with salt spray is that it is not a "real time" comparison of properties. In a low/no salt environment both nickel and zinc will perform well. Zinc is particularly bad for marine environments (which is essentially what a salt spray is trying to emulate) and so any testing using a salt spray will adversely reflect on the zinc.
Maybe a more realistic test would be a cyclic humidity test. The programme could be designed to reflect more closely the length of time of exposure to high humidity.
To be honest I suspect a good quality electroless nickel will outperform zinc, then again if you went from electroplated zinc with tri-passivate to zinc galvanising with passivate then I guess it could be the other way round.
All part of the fun of trying to predict how coatings will perform!
Aerospace - Yeovil, Somerset, UK
February 3, 2011
Q, A, or Comment on THIS thread -or- Start a NEW Thread