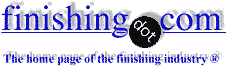
-----
Inconsistent Powder Coating - Perforated Material
January 28, 2011
We operate a custom-coating shop, and have run into a problem with a perforated steel sheet metal part. The part is used as a diffuser for commercial light fixtures, and shows an inconsistent coating when placed over a light source. This inconsistency is not noticeable without light passing through it. The material is 1.86 mm thick, and the perforation holes are 1.36 mm diameter. The perforations are separated by 1.15 mm of material. The part is approximately 4 FT. L X 6 IN. W.
The technical description of the perf-pattern given by our customer is:
20ga X 1/16" ON 3/32" STG 41%
When viewed under a microscope, the problem appears to be edge coverage. The edges of the individual perforations show a ring of incomplete coverage in the areas that appear 'light'. In places that don't have the 'light' look, the edges of the perforation are partially covered, or the exposed metal edge is noticeably smaller.
These parts come oiled from the perforating process, and our painter thinks this could have something to do with the problem. We run a 2-stage wash for this part with Iron Phosphate wash with a surfactant additive and an RO rinse. Another theory was bad part-grounding. With such a tight perforation pattern, the faraday-cage effect takes on variables I can't even begin to understand, and imagine there would be some electricity setting that would be the best solution to this.
The powder being used is a DuPont polyester, high-reflective white.
Has anyone out there seen a similar problem with perforated parts, or similar edge coverage problem? any and all help would be appreciated.
Custom Coater - Houston, Texas, United States
The following is a personal theory with no practical experience of this problem. However, it may get the ball rolling until someone comes up with a more likely solution to the problem.
I don't think tour problem is to do with gun settings, earthing or faraday cage affect--it's a defect phenomena associated with powder coating materials. Initially, powder will in the first stages of deposition head for the area of least resistance-- the edges. However, as the powder film becomes fluid during the baking cycle a change takes place at the peripheries of the applied powder--. changing from what may appear to be a 45 degree edge of the powder/substrate into one that produces a semi-curvature (think of a rain drop). The degree of this depends upon the powder formulation--. pigment, extender and flow additive content.
I'm not sure how your current powder performs apart from the defect you mention?
Does it have excellent flow with no orange peel? Also, some chemists in an effort to cut costs will reduce the amount of titanium pigment, reliant upon the substrate to give the appearance of good coverage. On a four sided powder coated item this works but on your fixture apparently not.
Try a powder with less flow additive or more pigment. Unfortunately, only your powder mf can supply this or alternatively, try another supplier.
Birmingham, United Kingdom
February 2, 2011
February 3, 2011
It sounds like you have a problem with earthing or with gun performance.
Isolate both, by preheating your work pieces.
Cut down your gun Voltages and spray.
By doing this you are bypassing the electrostatic effect and relying upon contact fusion and subsequent flow-out.
This should eliminate any problems with Earth or Gun set.
If it is successful you know exactly what to concentrate on.
Hope this helps,
Regards,
Bill
Trainer - Salamander Bay, Australia
Q, A, or Comment on THIS thread -or- Start a NEW Thread