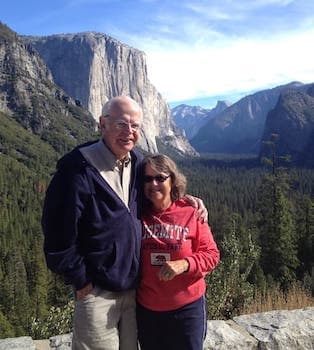
Curated with aloha by
Ted Mooney, P.E. RET
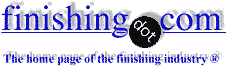
The authoritative public forum
for Metal Finishing 1989-2025
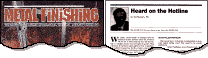
-----
How to Passivate Invar-36 Alloy
The Invar-36 alloy is a low-thermal coefficient of expansion alloy of steel with small amounts of Selenium and Silicon. The drawing specifies citric acid I (7.1.1.1) passivate per ASTM A967, but that turns the parts dark grey to black. We tried Nitric (6.1.1.1) and that made the appearance even worse. They also failed the standard copper sulphate ⇦ this on eBay or Amazon [affil links] drop test following processing. Our bath concentrations and temps are in specification. Anyone have any successful experience on this?
Mike PalatasAerospace Metal Finishing Shop Manager - Gardena, California, USA
January 26, 2011
Mike
A quick search suggests Invar is absent of chromium. Stainless steels have a minimum of 10.5%. The specification and process are for stainless steel. It sounds like an engineer or 2 erred in calling out passivation for that material.
- Colorado Springs, Colorado
January 26, 2011
Invar-36 cannot be passivated by Nitric acid, because this alloy dissolve on Nitric, also there is no reason to passivate in citric acid - it will not make the surface passive. Usually for such special alloy types we develop special passivating liquids or gels. If you need help - contact us. We need samples of this alloy and the testing procedure you prefer.
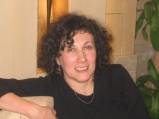
Anna Berkovich
Russamer Lab

Pittsburgh, Pennsylvania
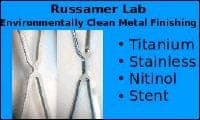
February 1, 2011
36% nickel, most of the balance iron? It's difficult to say if that can be passivated in the sense that stainless steel can. No chromium, true, but the nickel can serve a similar purpose (austenitic stainless grades have good amounts of both chromium and nickel, in 316 for instance the sum of the two is about 30%).
We've found that high nickel (non-stainless) alloys do get darkened in straight citric solutions, but a citric solution raised to a higher pH (3 or 4) works better. Try a bath like that for about 20 minutes and see what the results are like. Only way to find out is to test it.
Also I'm not sure copper sulphate would be a reliable indicator for this type of alloy, just as it's not recommended for most martensitic stainless grades.
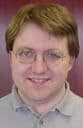
Ray Kremer
Stellar Solutions, Inc.

McHenry, Illinois
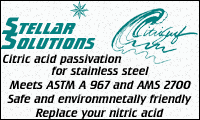
March 1, 2011
Q, A, or Comment on THIS thread -or- Start a NEW Thread