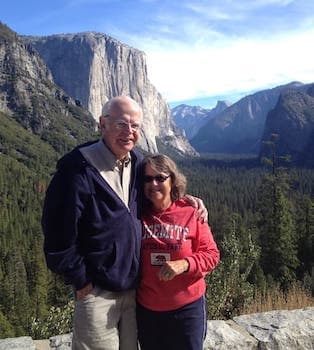
Curated with aloha by
Ted Mooney, P.E. RET
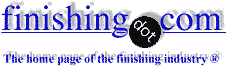
The authoritative public forum
for Metal Finishing 1989-2025
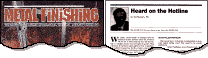
-----
Etched stainless steel surface for live bone removal.
January 2, 2011
What process can be used to produce an abrasive surface on one side of a polished stainless steel ribbon 2.5 mil thick X 0.200 inch wide X at least 12 inches long.
The material will have the hardness typical of commercially available shim stock.
It would be desirable to have an abrasive equivalent of a glass finger nail file as the purpose of the ribbon is to remove bone in a surgical setting.The side surfaces and non abrasive side of the ribbon will preferably Teflon coated prior to creating the abrasive surface.
Product Designer - Hollis, New Hampshire
January 4, 2011
Blasting or fine knurling,
Good luck,
G. Marrufo-Mexico
Monterrey, NL, Mexico
What about laser cut abrasive surface and then all together electropolished. Thus you will have one surface abrasive and all together corrosion protected. And no Teflon coated is required
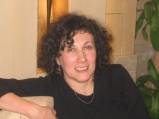
Anna Berkovich
Russamer Lab

Pittsburgh, Pennsylvania
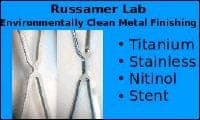
January 5, 2011
To:Guillermo Marrufo
Monterrey, NL, Mexico
Your suggestion of fine knurling makes sense to me. Can you tell me what the maximum surface hardness can be to produce the abrasive surface needed for bone removal. I am assuming that a spring temper of Rc 55 would be too hard.
Blasting would certainly be a less expensive process but I wonder how it can produce the uniformly structured surface for my application. What are your thoughts?
Thanks, Jim Healy
- Hollis, New Hampshire, USA
January 11, 2011
January 12, 2011
Knurling tools are often made of hardened steel like the one used for files rather than spring steel (it's even harder like 60-62 Rc). If you could find them of tungsten carbide it would be even better.
G. Marrufo
Monterrey, NL, Mexico
Q, A, or Comment on THIS thread -or- Start a NEW Thread