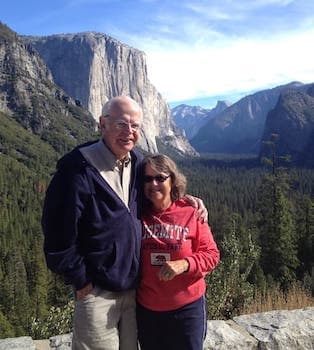
Curated with aloha by
Ted Mooney, P.E. RET
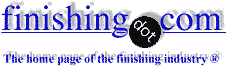
The authoritative public forum
for Metal Finishing 1989-2025
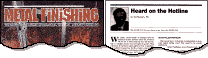
-----
Lab tech has Anodizing 101 questions
December 22, 2010
Good day.
My name is Eric Bogner and I am the lab tech. I have been in the plating industry since 1973. Presently, my duties require me to analyze various solutions, with the anodizing solutions not being my forte. the chromic/sulfuric analysis are straight forward for me, my weakness is understanding impurities, as limits, and their effects. I have found Cu via AA @ 230 ppm in the hard anodize, only because I noticed the SS anodes were RED. I need to know how much is acceptable, and what are effects [we use 2024 alloy=4.9% Cu]. My process indicates max. Al 8.0 gm/l, NaCl 0.2 gm/l and I would like to understand why. Also, I found 100 ppm Cr, as the anodizer reversed the tank polarity to "dummy" out the Cu. I indicated to insert a smaller anode over the existing anode and remove this anode as req'd. to strip Cu. I would like to make up a new sol'n. @ 240 gm/l H2SO4, do I need to add Al? Hoping you can help with this, as I think I need anodizing 101. I am looking for info as a TDS, if that is A) plausible B) possible.
Regards Eric Bogner.
Happy Holidays.
Industrialist - Toronto Ontario Canada
December 23, 2010
Sheasby/Pinner and Brace say to limit copper at 50 ppm, but if you are running 2000's alloys there is no way you can hold it that low. I have never been able to document any evidence that 230 ppm will harm anything. You need about 5 gm/L dissolved aluminum,. In my book I preach to hold it between 8 and 12 gm/L - decant and add back when you pass 12. Boeing preaches stay below 21 ppm, but Boeing is never dyeing. It is not clear what you mean by the chromium, dummying, etc. A new solution should be about 180 gm/L unless you are hard coating heat treated 2000's, in which case 230 is my recommended limit, 240 is too high - makes the pore too large. Be reminded that most commercial grade aluminum sulphate is used for water treatment, therefore is filthy - either use reagent grade or just run enough scrap to get up to 4 or 5 gm/L.
Come back with more data and let's kick this around some more.
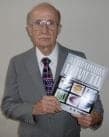
Robert H Probert
Robert H Probert Technical Services

Garner, North Carolina
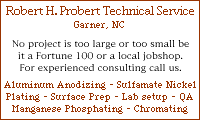
Thank you for your reply re; 230 g/l H2SO4. The anodizer reversed the tank polarity as a plating cell in an effort to plate out the copper. Therefore, the normal SS cathodes during anodizing now became anodes(+), and I believe the chrome from the SS went into solution during the plate-out phase to remove copper.I detected 100 ppm chrome, and am thinking this solution needs to be replaced.What is the limit for chrome(does it need to be reduced to trivalent?).I would like to know the effects that various impurities have on this solution and their limits.
Regards
Industrialist - Toronto, Ont, Canada
December 29, 2010
Hello Robert. Thank you again for your reply. I would like to be clear on your recommendations. We have sulfuric Anodize Max Al @ 20 g/litre. Total H2SO4 220 g/litre. Free H2SO4 180 g/litre. We also have Hard Anodize whose specs are as follows, Total sulfuric 280 g/litre, Free 230-260 g/litre and AL Max of 8.0 g/litre. I am making up a new hard anodize solution to primarily anodize 2024 material at 230 g/litre sulfuric. Am I correct in interpreting your response that you recommend AL@ 5g/litre in this situation? Or was the recommendation for sulfuric Anodizing makeup? My hard anodizing tank is 560 US Gallons, which would mean using reagent grade aluminum sulphate @ 8.1% AL, that I would require 287 pounds of Aluminum Sulphate for bath makeup. Presently our hard anodizing bath for 2024 material is maintained at 3.5 g/l AL.
Eric Bogner- Toronto, Ontario, Canada
January 5, 2011
For regular anodizing the industry standard used to be 20 gm/L of dissolved aluminum and some Boeing specs still recognize that number, however, those who are dyeing prefer to limit the alum to 15 gm/L, and I prefer hold it between 8 and 12.
Regarding the hard coat on 2000's, you know that the higher the free acid the larger the pore. I have not seen any 2000 alloy that I could not do at 230 gm/L free acid. Your 260 number is making a larger pore - hence "softer" or less abrasion resistance.
Regarding dissolved aluminum in hard coat, it is difficult to get started, I like to try for 4 or 5 gm/L to start, then hold between 8 and 12 gm/L. The 3.5 is "marginal", let's try that and observe the quality, if needed, then just run scrap until you get up to 4 or 4.5, then it should be OK. Surely we can avoid buying 287 pounds of reagent aluminum sulphate, let's run some scrap.
If the regular anodize is up to 20 gm/L aluminum, then let's pour some in the hard coat tank, stick in some heat and evaporate it down.
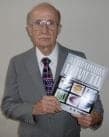
Robert H Probert
Robert H Probert Technical Services

Garner, North Carolina
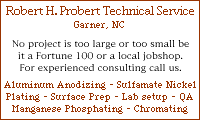
January 6, 2011
Thank you for the information on the numbers for makeup Robert. I have the solution @ 230 g/l sulfuric and @4.5 g/l Al. We are running @ 21-24 degrees F. for the 2024 alloy. I think our problems are rectification issues, as voltage is rising after reducing. I do have a lot more questions, and I will learn more ins and outs once I have finished reading your book which just arrived.
Eric Bogner- Toronto Ontario Canada
January 13, 2011
If you're anodizing by current density (i.e. ASF) your voltage should rise as your current remains steady through out the cycle time.
I would look into pulse rectification if I were you, assuming you're going to be hardcoating a lot of 2000 series work. This would reduce the amount of cooling you need, as a tank temperature of 21-24 F sounds awful cold, and expensive to me.
Bottom line, in my opinion, 2000 series Al is just about the worst choice of wrought alloys for hard anodizing. If your customer is not bound by this choice, I would advise them to select another alloy.
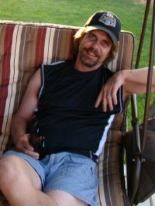
Marc Green
anodizer - Boise, Idaho
January 14, 2011
Q, A, or Comment on THIS thread -or- Start a NEW Thread