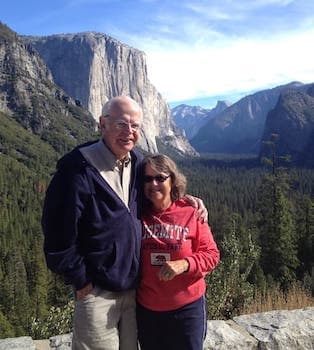
Curated with aloha by
Ted Mooney, P.E. RET
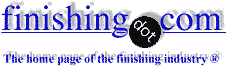
The authoritative public forum
for Metal Finishing 1989-2025
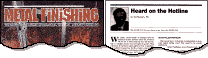
-----
Gold Plating Thickness Recommendation for Electrical Cspeconnection
December 17, 2010
Issue: We had a stainless spring gold plated and ended up paying a fortune ($1.71 each) for plating on a very small coil spring (dia=.13", length=.63"). The thickness for the gold plating was likely overkill for the application. We specified a thickness for a disposable (single use) device the same as a reusable device (25-50 uses). I need recommendation for an appropriate plating thickness.
Product: Electrical contact spring is used to carry a 1.0 A current in a disposable medical device. The device is for one-time use, so there is little opportunity for wear of the plated surface. The device is shipped clean and sterile so there is no opportunity for build-up of contaminants that might compromise the surface resistance. The connection is not stationary. The spring rotates under light tension against a tin plated copper beryllium ring perhaps 10-15 turns over the product life.
Current specification:
Base material: Stainless spring steel, nickel plated.
Surface treatment: Clean per ASTM B254: Sulfamate Nickel, 0.00005 minimum per AMSC26074B
Finish: Gold plate, Nickel Hardened Gold, Type II, Grade C, Class 2.5, 0.0001 minimum per ASTM B488.
Question: What thickness of gold plating would be appropriate for this application?
Question: We have over $36,000 invested in 21,000 springs that are likely plated too thick. Is there any way to strip the gold off these springs, have them re-plated to a reduced thickness, and recoup some of the cost?
Note: One possibility is that the plater did not have good control over the process and ended up over-plating, and thus over-charging us. Another possibility is that the vendor did not accurately account for the surface area of a coil spring.
Thanks for any feedback!
Mechanical Engineer - Boulder, Colorado, USA
I am a bit lost. Are you paying for weight added in plating, or why do you think that the plater put too much on. The price was agreed to before you shipped the parts, so what is the complaint. Ship a few parts to a very reputable analytical facility and they can tell you the actual gold thickness without destroying the plating or the part in most cases. If you want it to include the ID, then it will be necessary to cut the part.
Microscopic evaluation is destructive, but it is the referee method in most cases. Again, this requires a good facility as it can be messed up and read low.
- Navarre, Florida
December 23, 2010
December 28, 2010
Just a couple of points.
Your contact appears to be gold against tin. What is underneath is only there to provide contact pressure.
This looks like a complete waste of gold. Unplated stainless would probably perform as well. To improve the reliability , I would consider putting the gold on the beryllium copper rather than on the spring.
And why use beryllium copper if is not the spring element. Brass would be cheaper, easer to plate and avoid beryllium in a medical application. Electroless nickel would be worth considering as a non corroding hard contact surface without the dermatalogical problems of pure nickel.
Secondly you have specified a minimum thickness of gold. Plating thickness has a natural variation depending on the shape of the part (among other things) To achieve your specification, it is therefore necessary for the plater to plate an AVERAGE thickness which significantly exceeds the required MINIMUM. In some cases, this can be several times the minimum stated. The cost of the part is calculated on the total weight of gold used i.e. average thickness x total area.
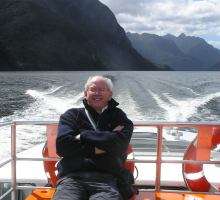
Geoff Smith
Hampshire, England
Q, A, or Comment on THIS thread -or- Start a NEW Thread