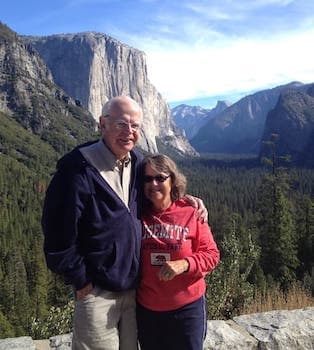
Curated with aloha by
Ted Mooney, P.E. RET
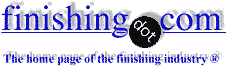
The authoritative public forum
for Metal Finishing 1989-2025
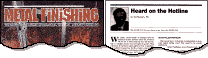
-----
Etching aluminium prior to sulfuric acid anodising
December 14, 2010
My company has been supplying spun aluminium alloy products to the Aerospace industry. These have been successfully anodised to MIL-A-8625F Type I (chromic acid). This produces a dull olive coloured finish and disguises unwanted blemishes created at the spinning stage. We have now changed one of our products to MIL-A-8625F Type II (sulfuric acid). This has surprised us in that there is no masking of surface blemishes; you can see through to the untreated surface where there are 'rings of Saturn' from the spinning process. Where there has been corrective burnishing, you can also see these marks which is unacceptable.
A colour dye at the moment is not a customer option, although this would seem to solve the aesthetics problem. I am looking for a pre-treatment which will enhance the finished look of the product. The process shop we use are utilising an alkaline etch solution prior to treatment. Can the etch time be extended to give a more uniform finish, or is an acid etch more effective, or is there a 'light' dye that can be used rather than a solid colour?
Thanks in anticipation.
Project Engineer - Fareham Hants United Kingdom
A heavy caustic etch MIGHT might work, but it will be a complete trial and error method of checking to find the right time/temperature/concentration. Another option might be to try in the lab with sections of a scrap part using a nitric acid solution with about 1 lb per gal of ammonium bifluoride added. This will provide a fine etch that will be brighter. You may want to try using some combination of both. Note that the bifluoride is a far safer chemical than hydrofluoric acid and does nearly the same thing. Avoid 70% and 50% HF. It is nasty!
James Watts- Navarre, Florida
December 14, 2010
Q, A, or Comment on THIS thread -or- Start a NEW Thread