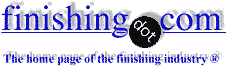
-----
Titanium Nitride coating warps small diameter gauge pins
I recently had .020" and .021 (L=2") class Z gauge plugs coated in titanium nitride and they came back warped. I need a hard coating on these pins. Can the warping be avoided, or is this going to happen on small diameter pins?
Rudy MorenoDesigner - Pearlan, Texas
December 1, 2010
The warping is due to overheating of the parts. Your coating services provider should be able to get you a good coating without any warpage. If the TiN does not adhere well or work well after deposition at the lower temperature, consider CrN.
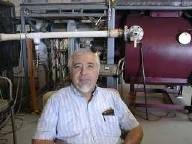
Jim Treglio - scwineryreview.com
PVD Consultant & Wine Lover
San Diego, California
First of two simultaneous responses -- December 3, 2010
Second of two simultaneous responses -- December 4, 2010
The small pins get heated fast resulting in warping. One has to reduce the input power. The pins are heated by several processes during coating:
1. Radiant heaters
2. Ion etching / discharge cleaning.
3. TiN coating.
It also depends on the coating technology being used namely cathodic arc, unbalanced magnetron sputtering, balanced magnetron sputtering or electron beam techniques.
Operating parameters like rate of deposition, etching and bias voltages also control rate of heating.
If you are coating objects of different dimensions they are likely to get heated to different temperatures with smaller ones getting over heated.
Following could be tried:
1. Run a coating cycle exclusively for pins and control temperature.
2. If you are using cathodic arc keep the arc current to a minimum and maximize the distance of the pins from the arc.
Keep the ion current and energy minimum while etching. Same applies to the case of unbalanced magnetron sputtering.
3. It would perhaps be better to use balanced sputtering technique if you do not have problems of adhesion.
4. The pins should be properly fixed and manipulated while coating. Non uniform heating could be a source of the problem.
Good luck!
Bangalore Plasmatek - Bangalore Karnataka India
Q, A, or Comment on THIS thread -or- Start a NEW Thread