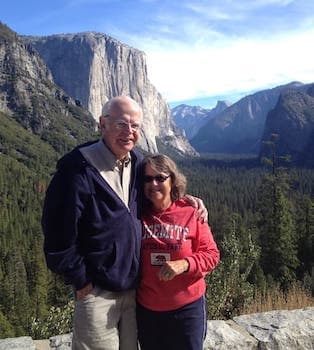
Curated with aloha by
Ted Mooney, P.E. RET
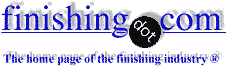
The authoritative public forum
for Metal Finishing 1989-2025
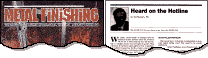
-----
Guidelines for acceptable rack marks and other non anodized areas
Q. What percentage of an anodized part is allowed to have rack marks or air bubbles on a blind hole? What is the largest tapped hole not required to be anodized?
Hector NevarezMachinist - Hesperia, California, USA
November 30, 2010
![]() |
A. There's no fixed answer. Every buyer must understand that some rack marks are inevitable, and every anodizer must try to minimize them. After that it's a matter of negotiation between purchaser and supplier to find a size and location both can live with. ![]() Jeffrey Holmes, CEF Spartanburg, South Carolina December 2, 2010 A. There are no "guidelines" per se, although any anodizer with his salt will try to keep the rack marks to a minimum, keeping in mind that he must be able to hold the part securely, and make good electrical contact throughout the anodizing process. If you are the customer, you should be able to work with your coater on an acceptable size, and location of the rack marks. ![]() Marc Green anodizer - Boise, Idaho December 2, 2010 A. Hector - Colorado Springs, Colorado December 2, 2010 |
Q.
I am doing oil rubbed bronze plating on aluminum extruded 3 ft strips which are 1 mm in thickness and 1.3 inches in width. We are getting jigging spots that is no or very less copper at the place where the jig touches the job. The problem is not on all the pieces. The rate of rejection is around 25%. If somebody could give us an solution we would really appreciate it.
Regards,
- Agra, India
August 25, 2012
How to avoid tool marks when anodizing
Q. I have one kind of cover needs to be anodized, but there is no holes on the cover. So on anodizing, the tool has to lock on the two sides. While it leaves the two sides obvious marks on the lock position. Could someone help to advise how to avoid it?
Jenny Cheung- Shenzhen
June 15, 2017
A. Hi Jenny. Rack marks are an unavoidable part of anodizing. However, skillful rack design can make them smaller or in a less conspicuous spot. After that, your options are (with your customer's permission), simply apply a magic marker for cosmetic purposes (no corrosion resistance) or preferably a chromate conversion coating to offer reasonable corrosion resistance. If this is spec work you might look at MIL-A-8625 / MIL-PRF-8625 [⇦ this spec on DLA] for the anodizing and MIL-DTL-5541 [⇦ this spec on DLA] for the chromate conversion coating touchup.
Regards,
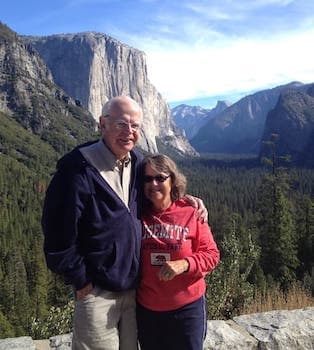
Ted Mooney, P.E. RET
Striving to live Aloha
finishing.com - Pine Beach, New Jersey
June 2017
A. Please share the pic of that cover ... then we can remark.
alaattin tuna- TURKEY sakarya
August 26, 2017
Q, A, or Comment on THIS thread -or- Start a NEW Thread