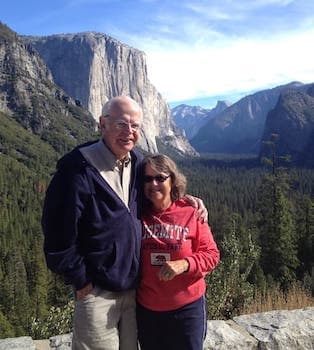
Curated with aloha by
Ted Mooney, P.E. RET
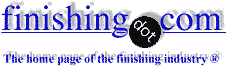
The authoritative public forum
for Metal Finishing 1989-2025
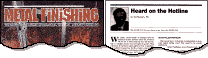
-----
QA Practices for Chrome Plating
Hi, I am an engineer working for a company which looks at corrosion issues. We are having some issues with corrosion of chrome plated hydraulic cylinders which appear to be the result of porosity in the chrome plating and would like to come up with some standards and testing procedures to apply to the cylinders and hopefully mitigate the corrosion issues.
Currently, the cylinders lack exact specifications and have no QA testing requirements. Would it be useful to look at using a nickel plating on the steel before chrome plating and changing the thickness of the chrome plating as possible steps to take to solve the porosity issues?
I am also interested in what type of QA practices manufacturers generally use, or should use, for chrome plating operations. I read that surface roughness and cleanliness, gas agitation, and mechanical finishing after plating seem to be major factors in the efficacy of the plating. It seems that those factors should all be closely monitored, but are there others that are crucial to the porosity of the final product?
Finally, we have been using the ferroxyl test to determine the porosity of the plating, but are interested in looking into other effective tests that can be used in the field and do not require highly specialized equipment or extended periods of time (e.g. SEM, spray cabinet, etc). If there are any other thoughts or suggestions on any of these topics, I would love to hear them. This site has been a great resource for me, so thanks for your help.
Corrosion Engineer - Reston, Virginia, USA
November 30, 2010
Nickel underplating would certainly help. Truck bumpers would normally use two different types of nickel for even greater protection. Plating thickness is certainly going to have an effect.
Ferroxyl is an extremely sensitive test. copper sulphate
⇦ this on
eBay or
Amazon [affil links] is a less sensitive test that works for many applications , has a longer shelf life and is a bit safer to use.
- Navarre, Florida
December 2, 2010
Thanks for the response, James.
Can you provide any insight into how plating thickness affects porosity? For example, if you were having porosity issues, would you start by increasing or decreasing the plating thickness? It would seem to me that a thicker coating would reduce porosity, but that cracking and other defects might become an issue.
- Reston, Virginia, USA
December 9, 2010
December 10, 2010
All chrome is cracked or micro cracked which is far better.This may be giving you the porosity indication.
Grinding is hard on chrome, and most grinding shops push for production rather than quality by using the wrong feeds and speeds, excessive depth of cut and the wrong resin/grit in the wheel. This cracks the chrome even more and when taken a bit further, causes delamination.
Normally, more chrome is better for pores, but if the pore is really a pit, then nothing will help. Pits have many sources from inadequate cleaning. grit imbedded in the part and trash floating around in the chrome tank.
- Navarre, Florida
Q, A, or Comment on THIS thread -or- Start a NEW Thread