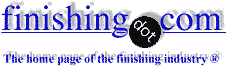
-----
Cost of automated plating tank covers
Hello,
I'm writing a thesis on tank cover alternatives for electroplating and am looking for some idea costs to retrofit automated tank covers for an automated nickel chrome electroplating line, assuming that the surface around the tank is already clear and ready to for installation of covers
Realising that there are a lot of factors/options involved, and also at the end of the day there's probably nothing too special about fabricating it, but just trying to get a feel for the costs.
Thinking about a cantilever 'french door' type cover, but any other ideas would be appreciated... all sources referenced in the report!
Thanks (also thanks to Finishing.com resources in general which have helped immensely),
Student - Melbourne, Australia
November 30, 2010
November 30, 2010
Hi, Benjamin
Although french doors are relatively simple, I'm not sure that they are ideal for an automated line. You might want to consider roll-top covers, as in a roll-top desk, as an alternative.
It is important to state up front exactly what you think the covers will accomplish, as their purpose guides their ideal implementation. For example: do you want the covers to cover the tank only when work is not in it, or when work is in the tank as well? Covering the tank only when empty is easier, but does it do enough good? The chrome tank is only occupied 30 seconds out of say every 5 minutes, but those 30 seconds are when all of the hydrogen gas is evolving and most of the mists are generated.
Faking up a material balance and energy balance with and without covers may not be completely accurate but it is the driver and a starting point towards the design.
As for the costs, you have to assume materials of construction to make progress there. Again I don't think accuracy is as important as a systematic approach. Good luck.
Regards,
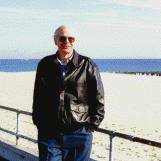
Ted Mooney, P.E.
Striving to live Aloha
finishing.com - Pine Beach, New Jersey
December 5, 2010
Hi Ted,
Thanks for the response.
I think my question was a little vague. The covers are intended to cut energy consumption - the report is really a cost benefit of various cover alternatives - automated covers able to cover tanks during and out of production hours, chroffles, and static covers that cover the tanks outside of production hours.
I saw the french door idea in Finishing Magazine - article from 2005 by a company that manufactures them. They were automated so that they opened and closed as needed.
The roll-top is a great idea! I think it really needs a robust solution like that to be practical and stay in use - from speaking to some plating contacts, removable covers seem to get used for a while and then end up in storage.
Doesn't seem to be a heap of material readily available on the subject of covers, so thought it might be useful to work on. Also it seems covers are not really used much in this part of the world...
Best regards,
- Melbourne, Australia
Hi, Benjamin. In addition to reducing heat losses, some covers may reduce the emission of toxic or corrosive fumes, and help keep contaminants out of the tanks. The disadvantages, in addition to capital and maintenance costs, can include general messiness (the need for some place to put them, and dripping onto the floor as they are opened or removed).
One way of approaching the project would be to keep it simple but try to arrive at a guideline or three dimensional graph showing the energy saving of tank covers vs. the operating temperature and number of hours of production or other similar factors.
Or, you could look at a graph of surface losses vs. temperature, and decide that the hottest tanks are the best candidates, and restrict your study to one particular process step that most plating shops would have (including your nickel-chrome plating line), like a soak cleaning tank operating at approximately 185° F. Pick a representative size, say 8 foot x 3 foot x 4 foot deep, or use the actual size from a shop you know, and calculate where the heat energy goes (surface losses, wall losses, losses to cold work entering the tank, drag-out losses) and then predict the savings based on different production rates and different hours of production. Maybe you'll stumble on a serendipitous fact like "covering tanks during off hours doesn't save much energy for one shift operations, but is valuable for two-shift operation", or vice versa. Or, "the key to energy savings is closing the top while the work is being processed", or while the shop is open but the tank is empty, or during hours when the shop is closed. Good luck.
Regards,
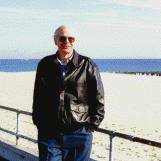
Ted Mooney, P.E.
Striving to live Aloha
finishing.com - Pine Beach, New Jersey
December 6, 2010
Q, A, or Comment on THIS thread -or- Start a NEW Thread