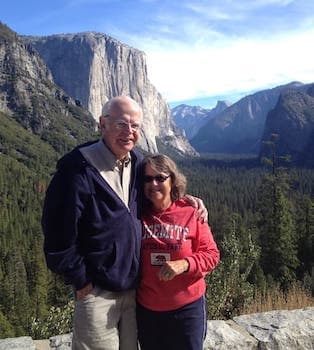
Curated with aloha by
Ted Mooney, P.E. RET
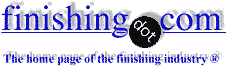
The authoritative public forum
for Metal Finishing 1989-2025
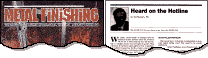
-----
Leak test in Nickel plating
Q. Is anyone who can provide me the leak test procedure and cause of leaks in Nickel plated parts?
Thanks
R&D - Edison, New Jersey New Jersey
November 30, 2010
A. Do you mean vacuum leak testing? We vacuum leak test products before the nickel plate as we find that the nickel plating interferes with the test.
Mark McKinnon- Rugby, United Kingdom
January 21, 2011
A. Hi, Jawed. You are referring to nickel electroformed components that must be tested. Please research "helium leak testing". The cause of the leaks would be improper electroforming conditions.But I know that your company has been successfully electroforming and helium leak testing those components for decades. If the knowledge has been lost, you can contact Berl Stein at NiCoForm [a finishing.com supporting advertiser] for help because I know the parts were passing when he was employed there. Or please get back to us with more info. Good luck.
Regards,
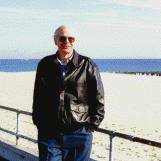
Ted Mooney, P.E.
Striving to live Aloha
finishing.com - Pine Beach, New Jersey
Q. Thanks for your answer. Its been long time I posted this question but had no knowledge how to get back to the answer. Our company is doing for long time electroforming and problem was there for long time also.
We are not getting 100 % leak test pass. Chemical composition is as per specs and I am doing regular analysis, filtration, carbon filtration and peroxide treatment once a year. Proper pre-plating procedure and doing zincating aluminum mandrels. But still some times bellows failed in helium leak test.
Any idea what area need improvement?
- Cedar Grove, New Jersey
June 27, 2013
June 27, 2013
Q. We are plating nickel over Aluminum Mandrels and after leaching bellows get inspected for Leak test. Most of the times helium leak test failed due to the microscopic holes in it.
We have Nickel sulfamate baths:
Specs are:
Sulfamate: 11oz/gal
Boric: 5 oz/gal
Chloride: 0.8 oz/gal
Wetter:Regularly checked
Brightener: Regularly checked.
Temp: 40 °C
Mechanical agitation:
24 hours 10 Micron filter and Carbon filter.
Anyone can help me to find the problem?
Chemist - Edison, New Jersey
A. I few suggestions
1. ensure that the al mandrel and zincate are as smooth as you can obtain. Lowering the temp of zincate solution helps make zincate more dense.
2. Lower concentration of boric acid to 4 oz/gal. this ensures that boric acid does not crystallize out on cold mandrel.
3. check that there is not too much wetting agent in the bath. Hold a beaker of solution up to the light. You should only see 1 phase - not any bubbles.
4. pulse plate the nickel to reduce grain size and decrease porosity.
5. rotate mandrel if you are not already doing so.
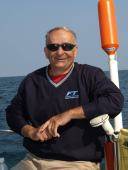
Pat Mentone
St Paul, Minnesota
June 29, 2013
Q. Thanks for your suggestions but we already tried all these suggested points except to lower Boric acid. Lowering boric acid causes pits so I have to maintain 5 oz/gal.
I tried double zincate also, but not good result.
Peroxide treatment improves it a little but not significant change.
Any other idea?
- Cedar Grove, New Jersey
July 1, 2013
Q, A, or Comment on THIS thread -or- Start a NEW Thread