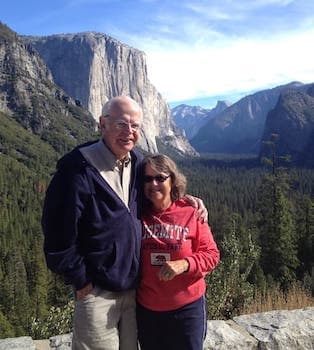
Curated with aloha by
Ted Mooney, P.E. RET
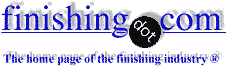
The authoritative public forum
for Metal Finishing 1989-2025
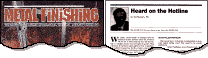
-----
Stainless steel passivation problem: color inconsistent

this text gets replaced with bannerText
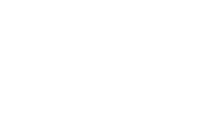
Q. We have stainless steel, passivated screws that have visible discoloration and texture differences.
We're thinking one, or both have missed a step in the process. Would anyone know what would cause this discoloration and texture differences?
CM EvansQuality Engineer - Michigan
June 15, 2022
CM,
It could be anything from a different acid being used to one was in the acid bath longer than the other.
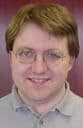
Ray Kremer
Stellar Solutions, Inc.

McHenry, Illinois
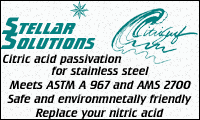
Thank you very much, Ray. I greatly appreciate it. CE
- Grand Rapids, MI
⇩ Related postings, oldest first ⇩
Q. Dear Sirs,
We are a precision tooling manufacturer, I have came across this problem with passivation. Recently, we have our tools sent for passivation process.The material is 440C, the different between this tool is one of them had heat-treated to HRC 56-58, the result we got after the passivation process is the one without heat-treat have a darker colour "black",the other which heat-treated came out with brighter colour "silver".
We were wondering what have happen in the passivation process.We hope that you have the answer for us.
Thanking you in advance.
Tai Mai- Georgetown, Penang, Malaysia
2003
A. What you are seeing is the carbon on the surface of what is affectionately called a "burned" product. This is not untypical with 440C and some other grades of high carbon, high sulfur stainless steels. it can be caused by a number of conditions in the bath. With using the correct pretreatment to remove some of the carbon and sulfur with alkaline (high pH) products you usually can eliminate this problem. If you are using nitric acid you need to have sodium dichromate or equivalent in the bath (caution: hexavalent chromium). If you use the correct citric acid based products that are on the market you will not have this problem and get consistent high quality parts.
Let us know if we can help.
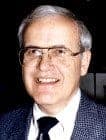

Lee Kremer
Stellar Solutions, Inc.

McHenry, Illinois
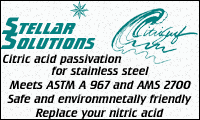
Q. I am the Quality Control Supervisor for a FAA Repair Station. We do some passivation in house, however, the results are not very consistent. Sometimes while performing this process on Stainless Steel parts the result is a clear and shiny color while in some other cases the outcome is a dull and darker color. Are the different results due to the dipping time, contaminants, temperature and/or humidity? or simply because there is a range like in any other coating or plating process. Thanks in advance for your cooperation
Gino FarandaQuality Control Supervisor - Miami, Florida, USA
November 23, 2010
![]() |
A. Check the chemical makeup of each lot of SS. - Navarre, Florida A. Gino, Aerospace - Yeovil, Somerset, UK |
A. This does depend on factors such as the grade of stainless, type of passivation bath used, temperature and immersion time.
Generally, when you see a "color change" in a metal surface, it is due to the surface finish. A smooth, shiny surface that is chemically etched will appear darker to the naked eye.
If you are having etching problems with some of your parts, you may need to reduce the immersion time or find a more appropriate bath. The passivation standards have charts that describe what nitric baths are best for which grades, or switch to citric acid which if done right will not etch the parts at all.
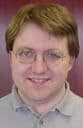
Ray Kremer
Stellar Solutions, Inc.

McHenry, Illinois
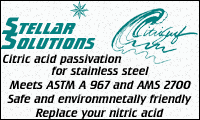
Q. Currently I'm facing a problem with my supplier related to the finishing of the color surface after the passivation process. Some parts looks shiny and other ones look like gray color, not shiny color. So, during this process, is it normal to have this difference between parts? Just to clarify, these parts were not processed at the same time.
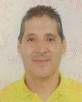
Ruben Alvarado
L3 comunications - Chihuahua.Chih. Mexico
August 25, 2017
![]() |
A. Ruben could you share the alloy of the parts and the type of passivation used? KAT aerospace - Chihuahua, Mexico A. Ruben, ![]() Ray Kremer Stellar Solutions, Inc. ![]() McHenry, Illinois ![]() |
Q. Sure Yohands the alloy is AMS5517.
Thanks Ray I appreciate your valuable help and comments
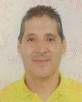
Ruben Alvarado [returning]
L3 comunications - Chihuahua.Chih. Mexico
Q. We are processing passivation for 440c stainless (nitric acid,Ty-II). After processing, part become black in color.
We are wondering what has happened after passivation process. I hope that I can get answer for this.
R
Aerospace - Tamilnadu, India
June 11, 2019
A. Naveetha,
The two more common causes is the parts weren't properly heat treated to full hardness, or the higher amount of elemental carbon in the alloy is collecting on the surface and it needs alkaline precleaning to prevent it.
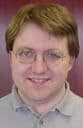
Ray Kremer
Stellar Solutions, Inc.

McHenry, Illinois
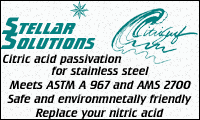
A. The darkened surface of the passivated surface may be due to a phenomena known as "flash attack", which is usually caused by a passivating solution that is contaminated or compromised to such an extent that it no longer is "passivating" the surface but rather corroding the surface instead. I have cut & pasted several paragraphs from literature below that help explain the situation below.
"Basic procedure in passivating consists of cleaning the work with a commercial degreaser or cleanser, immersing it in a solution containing nitric acid, rinsing and drying it. The importance of cleaning prior to acid bath immersion cannot be over-emphasized. In some instances, this step is omitted, assuming the acid bath will give the necessary cleanness. Cleaning should not be skipped because the acid might not remove all of the residual cutting fluid, resulting in possible chemical reactions with the residual cutting fluid known as 'flash attack'. These unwanted reactions may cause serious deterioration of the surfaces that passivation is designed to protect.
Even worse, contamination of the passivating solution, sometimes with high levels of chlorides, can cause 'flash attack'. Instead of obtaining the desired oxide film with a shiny, clean corrosion-resisting surface, the flash attack produces a heavily etched or darkened surface. This is a deterioration of the very surface that passivation is designed to optimize.
Contamination in either nitric or citric acid chemistry can be detrimental to the passivation process. This is especially true of chloride which can lead to flash-attack or etching of the surface of the parts being passivated. Instead of achieving the desired oxide film with a clean and corrosion-resisting surface, flash attack will produce a heavy etched or darkened surface. A common chloride contamination limit is no greater than 60 mg/litter in either citric or nitric acid passivation chemistries."
Other Important Considerations
Maintain an effective passivating solution to prevent localized attack. Tap water is usually adequate for diluting the acid, although high chloride contents (greater than several hundred ppm) could be deleterious in a borderline situation. Nitric acid concentration should be checked periodically using a simple titration procedure, which can be provided upon request.
When high production rates cause a heavy flow of material through a passivating bath, it is probably best to maintain a definite schedule for replacing the bath to avoid a significant decrease in the 'passivating potential', which can result in corrosive attack of the work piece. You should also use a control sample of the same composition as the material to be passivated to test the bath. If the sample is attacked, it is time to change the bath before additional parts are passivated.
The temperature of the bath should be within the specified temperature range. A room temperature bath has a lower 'passivating potential' than a warm bath and is, therefore, more likely to cause local attack.
It is good practice to passivate only one grade of stainless steel at a time. Not only can mix-ups be prevented but you can avoid galvanic reactions.
Parts that were improperly heat-treated may lead to attack in a passivating bath. Furthermore, high-carbon, high-chromium grades must be hardened to render them corrosion resistant. Stainless steel parts that have been carburized or nitrided should never be passivated. These surface treatments lower the corrosion resistance of stainless steel, thus opening the way to attack in the passivating tank.
Naval Air Warfare Center (NAVAIR) - Lakehurst, New Jersey USA
Q. Thanks Ray and Rade for your Comments. But the actual condition is we have processed 400 Nos of stainless steel (440C) Parts. After Processing, 250 Nos were found Ok, remaining 100 Nos got etched (black color) on both sides and remaining 50 nos got etched on one side but another side were found okay.
After that we discussed the root cause how it happened?
The Root cause are given below:
1)Material Composition were Checked
2)Material Weight were Checked
3)Bath Contamination were Checked
4)Concentration were Checked
5)Iron Content were Checked
6)temperature were Checked
Everything is within the limit. That's Why we are surprised what happened.
Can you please let me know solution for this.
Aerospace - Chennai, Tamilnadu, India
A. Hi Naveetha,
One of the most frustrating things about processing 440C steel is the apparent random appearance of etching, as you have observed, even within the same batch. I'm sure there is a PhD out there for someone who actually nails the root cause! However, as will see in this thread and numerous others on passivation of 440C, several potential causes are considered and solution to prevent it recurring are suggested.
Potential causes include (but is not restricted to) chrome carbide enrichment of the steel, which is then preferentially attacked by the acid, possible residual surface contamination, bath contamination, aged baths and probably many other reasons.
Suggested solutions include (but are not restricted to) strong alkaline cleaning prior to passivation, using only new passivation solutions or using citric acid based chemistry rather than nitric acid based solutions. Personally, I try to avoid passivation of 440C if I can, therefore removing the potential problem altogether.
Aerospace - Yeovil, Somerset, UK
Q. We are using a 302 stainless steel spring in an assembly and are now starting to see rust, the passivation is using citric acid . The parts rust after 12 hrs in contact with DI water. We have not found a root cause yet, but have noticed that the ones that are rusting have a darker hue. Is this related?
Engineering Manager - Irving, Texas
July 26, 2021
![]() |
A. Zeeshan, ![]() Mark Battles Plymouth, Minnesota A. There's plenty of potential issues which could cause this, but if there a definite darker hue to the ones that are rusting, they might not be properly descaled before passivation. William Hogan- Sidney [New York] |
A. Zeeshan,
Just to spitball a theory here, darker color after passivation implies surface etching. Surface etching on austenitic stainless from citric acid is pretty much unheard of, which implies something like surface iron contamination or cold-work transformation into non-austenite. Non-austenite is going to be less corrosion resistant than austenite.
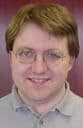
Ray Kremer
Stellar Solutions, Inc.

McHenry, Illinois
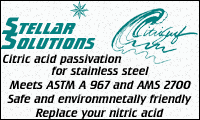
Q, A, or Comment on THIS thread -or- Start a NEW Thread