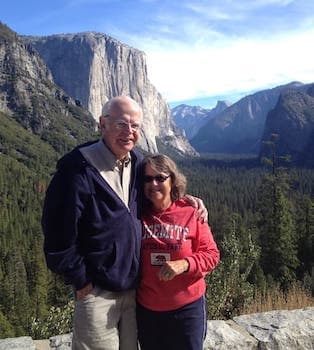
Curated with aloha by
Ted Mooney, P.E. RET
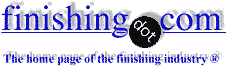
The authoritative public forum
for Metal Finishing 1989-2025
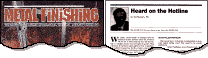
-----
Unsealed anodized aluminum corrosion resistance
Q. Good day. We produce a honeycomb core panel with an anodized frame that is bonded to a plastic skin; after much trial and error we now specify unsealed anodizing which was necessary to improve the bondline. This was a panel that was intended for indoor use, but now we are looking at outdoor applications as well. My question is if the unsealed anodized part will provide equivalent corrosion resistance as a sealed anodized part? This part is cut and machined in several locations, and our extruded implied that our corrosion resistance shouldn't suffer much in these areas because it is the sealant which is the primary corrosion inhibitor.
Best Regards
Product Design Engineer - New Hope, Minnesota
November 23, 2010
? Rob,
Which anodising are we talking about? Type I or II. The corrosion resistance will be a fraction of the sealed coating, especially if it is a Type I coating.
Aerospace - Yeovil, Somerset, UK
November 29, 2010
Q. Brian,
The anodizing is specified as Mil A-8625 type II, class 1, unsealed.
- New Hope, Minnesota
November 29, 2010
![]() |
A. Rob, Aerospace - Yeovil, Somerset, UK December 1, 2010 A. You normally will get better bonding with unsealed anodize than you will with sealed anodize. There are probably a few, but not many , exceptions. Unsealed is not a problem when it is painted or bonded. James Watts- Navarre, Florida December 1, 2010 |
Q. Brian - That confirms the suspicion that we will have little or no resistance to corrosion effects before cutting the panel. Obviously, we'd like to stay away from any type of secondary coating for cost purposes, but we may have to investigate it. I am going to get some samples going in our salt spray chamber to see what happens.
James - We learned that lesson the hard way with some early production runs. Quite a bit of delamination.
Any idea on a durable clear lacquer that can be hand-applied?
- New Hope, Minnesota
December 6, 2010
A. Rob,
I have had experience with clear lacquers from PPG, Akzo-Nobel and Indestructible. I can't really recommend one over the others as these have all been clear lacquers for use in Aerospace with consequent increase in lacquer costs, as we are paying for release against certain specifications. It is worth talking to these companies as they also supply commercial lacquers as well. There are quite a number of paint manufacturers so you may also want to consider companies such as Deft and Randolph as well.
Aerospace - Yeovil, Somerset, UK
December 8, 2010
Brian,
Thanks for the leads. You've been a great help!
- New Hope, Minnesota
December 13, 2010
Rob,
No problem, just glad I could point you in the right direction.
Aerospace - Yeovil, Somerset, UK
December 15, 2010
Gluing to anodized aluminum
Q. I need to glue foam to color anodized alum 6063 for outdoor furniture. My questions are, is there a method of sealing the anodize that best allows epoxy adhesion? If not, does the unsealed anodized alum 6063 offer good corrosion resistance? Are there alternatives that would be better choices of alum, 6061? There will be several pieces glued on each article, so spot surface prep is not an option with our volume.
I appreciate any guidance.
Matt
Product Design - Manahawkin, New Jersey
May 25, 2016
A. Hi Matt. Can you selectively seal the rest of the furniture except the bond line? If so, as James implies above, the adhesive will protect the aluminum in the unsealed area.
Regards,
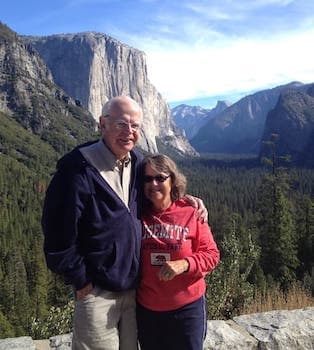
Ted Mooney, P.E. RET
Striving to live Aloha
finishing.com - Pine Beach, New Jersey
May 2016
Q. Thanks Ted,
We have 12 different bond points on each, unfortunately not a straight bond line. I'm afraid in volume this is likely not feasible. There will be very little stress(pull) against the bond, it's primarily just to keep foam applied to a seat. I know this is vague, but can even a marginally strong bond be created on sealed anodized alum?
Thanks,
Matt
- Manahawkin, New Jersey
May 25, 2016
A. You need to improve the wettability in order to get good adhesion. This can be done by exposing the part to a low temperature plasma. One option is to use a low pressure discharge. Here the parts are kept inside a vacuum chamber where a plasma is generated. The vacuum chamber has to be big enough to accommodate the parts to be treated. Alternately one can use use low temperature plasma jet/torch which is a hand held device. The flame of the torch is directed to the surface in question for a few minutes/seconds. The choice depends on various factors like the geometry of the object, number of pieces to be treated, cost and so on.
H.R. Prabhakara - ConsultantBangalore Plasmatek - Bangalore Karnataka India
May 26, 2016
Q, A, or Comment on THIS thread -or- Start a NEW Thread