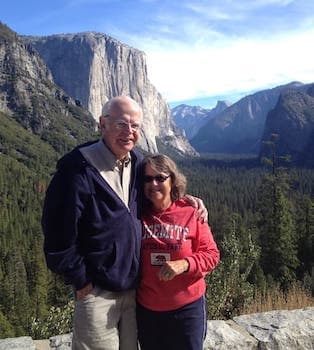
Curated with aloha by
Ted Mooney, P.E. RET
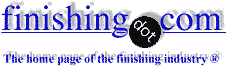
The authoritative public forum
for Metal Finishing 1989-2025
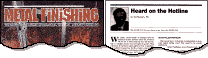
-----
Rapid White Rust in Flex Beam
Dear Sir,
I have a very concerned question regarding white rust. We started galvanizing flexbeam,
after galvanized, we have it quench, then let it air dry, after 30 minutes, the brightness faded and some cloudy white color form and after overnight storage under well ventilated roofed storage, formation of white rust started and while we tested one flexbeam after galvanized, we did not quench it and let it cool, after 30 minutes, the brightness is retain. May we know what is wrong with our process? and how can we avoid such thing to happen?
Technical Sales Manager - Dasmarinas City, Philippines
November 13, 2010
If you "quenched" your steel in plain water than it is not surprising to get white rust quickly.
To prevent white rust you will need a passivator in your quench liquor. One such is chromic acid.
Some people don't like chromate, but no-one has an effective alternative yet, despite claiming they do.
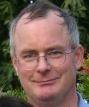
Geoff Crowley
Crithwood Ltd.
Westfield, Scotland, UK
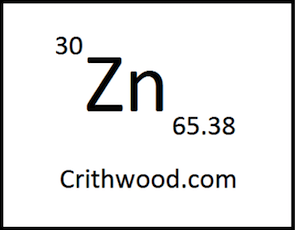
November 15, 2010
November 15, 2010
Sirs:
If you are going to use hex chrome, I recommend sodium dichromate rather than chromic acid. This avoids discoloration of the product.
To help avoid white rust my major tool is low aluminum in the zinc. Thus during the rainy season I recommend 0.0005% aluminum and for the dry season I recommend 0.001% aluminum. There are ways to make the coating brighter without high aluminum levels.
I am currently working on the true causes of white rust and I think I will succeed. I believe the real answer is the composition of the zinc.
Galvanizing Consultant - Hot Springs, South Dakota, USA
Dear Mr. Cook,
Thank you for the suggestion. Next question is, can you give us an idea of what percentage of al, ni, and zn combination, right now we are using a 98.999 zinc ingot, we also put pure al wire and ni tablet. And do flux really need to be heated? we don't have dryer.
- Dasmarinas Cavite
November 17, 2010
November 17, 2010
Sir,
As I have said, I like 0.0005% Al in wet season and 0.001% Al in dry season (to hopefully reduce white rust). Most galvanizers in the USA run nickel between 0.02% to 0.05% and most of these are closer to the 0.05%.
I have some concern that nickel pills may put nickel into the air. I expect to do some in-plant testing on this early next year.
For double salt a drying oven is used in Europe. For triple salt or quadraflux the flux is normally heated to 71C and a drying oven is not used.
Regards,
Galvanizing Consultant - Hot Springs, South Dakota, USA
November 22, 2010
It seems to me that a collaboration between The Yankee Doctor & Geoff Crowley could assist us all to understand the formation of White Rust and the degassing problems for Powdercoaters.
Get on with it guys and please keep us informed.
Regards,
Bill
Trainer - Salamander Bay, Australia
November 28, 2010
Sir:
It seems to me that if a galvanized product was NOT quenched in an aqueous medium, then there would be no out-gasing during powder coating. That is, the 450 °C molten zinc bath would have already out-gased the coating.
Regards,
Galvanizing Consultant - Hot Springs, South Dakota, USA
Q, A, or Comment on THIS thread -or- Start a NEW Thread