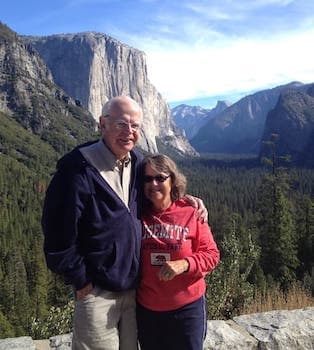
Curated with aloha by
Ted Mooney, P.E. RET
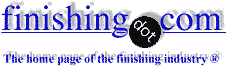
The authoritative public forum
for Metal Finishing 1989-2025
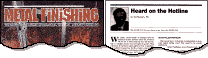
-----
Copper & Nickel Plating Thickness vs. Salt spray Resistance
Q. Reduce plating time?
Hello!
I'm a (soon to be) chemical engineer working in charge of a plating line in an industry that makes chrome door locks in Brazil.
We work with ZAMAC as a substrate for a decorative chrome finishing. Our process consists of:
1 - Cyanide alcaline copper (10 minutes, 3.5 A/dm2)
2 - Bright Watts Nickel (8 minutes, 4.0 A/dm2)
3 - Hexavalent Chrome (~1.2 minutes, ~13 A/dm2)
I believe our plating time in the copper and nickel bath is excessive, although I'm not aware of other manufacturers' plating times.
I've been conducting salt-spray tests with decreasing plating time. According to Brazilian norm, the parts should resist 48 hours in salt spray without corrosion, and I've had good results with up to 6 minutes of copper and 5 minutes of nickel (haven't tried lower times yet). I'm sending photos of the parts before and after the salt-spray test with the reduced time.
The reduced time didn't affect the aesthetic factor of the parts.
As for the layer thickness, we had 6 microns of copper with 10 minutes, then 4 microns with 6 minutes. With nickel we had 12 microns with 8 minutes, then 5 microns with 5 minutes.
I know for a fact that one of the main objectives of this copper layer is to protect the nickel bath from contamination of the zinc in the ZAMAC substrate, so I'm thinking about monitoring this through Hull Cell tests.
I'm fairly new in this area, have been working with plating for about a year now and I'd like to have the opinion of more experienced international people. Do you think it's safe to reduce plating time considering the above conditions? I think I'll try reducing the plating time to 8 min copper + 7 min nickel for a few weeks to feel the change, check the results and the contamination in the nickel bath. If it looks promising I'll keep reducing it.
I don't know why the last person in charge kept these long plating times and never tried reducing it.
Are there any other variables I should account for?
Any and all suggestions are more than welcome!
- Nova Friburgo, Rio de Janeiro, Brazil
March 24, 2022
A. Hi Pedro. I don't know exactly where these "chrome door locks" are used. If on interior doors, that is one thing -- environmental conditions are good and consumers frankly don't expect much. For a shed door, even if outside, again not much might be expected -- visitors don't knock on the door of a shed. But if this is part of, or to go alongside, decorative exterior locksets for fashionable front doors, it is a very different matter --
In my opinion "Brazilian norm" will offer your company no protection against a bad reputation if customers become dissatisfied, and "designing to salt spray hours" won't either -- designing to the actual application is what is important. 10 microns of nickel or below that minimum spec is for "Mild" service conditions. If you are doing exterior decorative items to go in or alongside of locksets such as offered by Schlage and Baldwin, and you feel that the service life has proved acceptable, count yourself lucky, and keep on doing what you've been doing rather than reducing the plating thickness.
Luck & Regards,
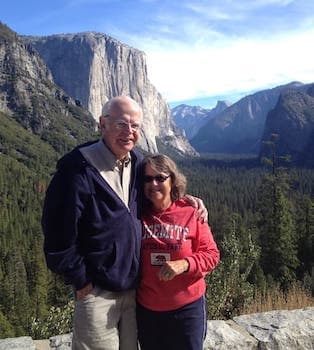
Ted Mooney, P.E. RET
Striving to live Aloha
finishing.com - Pine Beach, New Jersey
Q. Hi, Ted,
Thank you for your answer!
I see what you mean, it makes sense to design for the application.
These are door locks for glass doors, so it's mostly indoor use, although I've seen it in some balconies, but I don't think it's a very harsh environment.
I understand the importance of the nickel thickness and I agree with you. I'm hesitating in changing the nickel time, so I'll keep it at 8 minutes for now, so as not to take any risks.
However, I believe I can still gain some production by reducing the copper time, which is the longest right now and the limiting step of the process. If I reduce it from 10 to 8 minutes, it's a 25% increase, and I don't see many risks involved.
As far as I know, the importance of this copper layer is to avoid contamination of the nickel bath with zinc from the ZAMAK, since it doesn't give much protection against corrosion, and I can easily monitor the contamination level through Hull cell tests, do you agree with me?
Regards,
Chemical Engineer - Nova Friburgo, Rio de Janeiro, Brazil
April 7, 2022
A. Hi again Pedro. Yes I agree. Most specs and most people do not consider the copper plating as offering any corrosion resistance ... only the nickel counts, so enough time to prevent the zamac from being exposed to the nickel should be enough.
Luck & Regards,
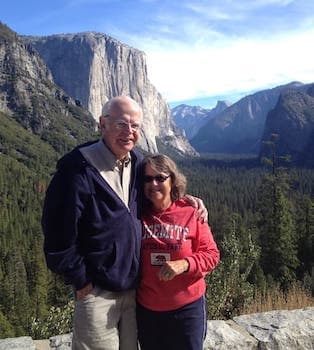
Ted Mooney, P.E. RET
Striving to live Aloha
finishing.com - Pine Beach, New Jersey
⇩ Related postings, oldest first ⇩
NSS = neutral salt spray
Is there is any specified standards for NSS for Cu-Ni plating to be coated. For example If we coat about 8 to 9 microns of Cu - 10 microns of Ni on spring steel how long it will withstand for the NSS Test. For getting 48 Hrs NSS what should be the thickness specification?
Prasad Kalamkaremployee - Aurangabad, Maharashtra, India
November 13, 2010
A. Hi Prasad.
Accelerated corrosion testing is a QA test intended to give the user an early warning that a process is getting out of control and running downhill. None are really good indicators of actual service life, and NSS is probably the least indicative of any of them. So you are not supposed to use NSS as a design parameter. Rather, you should probably design your parts for mild, moderate, severe, or extra severe service conditions ... and if you do that, yes, there are ASTM and other standards to guide you.
Luck & Regards,
Ted Mooney, P.E.
Striving to live Aloha
finishing.com - Pine Beach, New Jersey
Q, A, or Comment on THIS thread -or- Start a NEW Thread