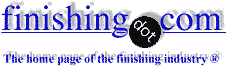
-----
Coloring non-anodized threaded holes
at work we are anodizing aluminum breadboards but our customer does not want them racked on the edge so we rack them in the threaded holes. after anodizing we can't seem to find a way to permanently color the "rack holes" without changing the size of the them. they either clog up and are too tight for the thread gauge or it wipes off after a few tests
Jonathan Donholtanodizing employee - Binghamton, New York, USA
November 10, 2010
Jonathan
I would check to see if the customer would machine some tooling holes for you on the backside. I have not found a suitable 'touch-up' either.
- Colorado Springs, Colorado
November 15, 2010
OK, I've got to ask....why does it matter if the threads are colored if obviously a screw/bolt will be inserted in them and the won't be visible?
However, if this is a totally necessary requirement, I seem to recall there is chromate treatment available in a black color, but I may be mistaken.
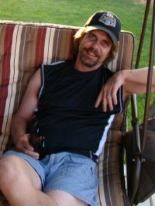
Marc Green
anodizer - Boise, Idaho
November 16, 2010
Mark
Breadboard is a plate with a grid of tapped holes used for mounting various devices at fixed locations, i.e. lasers, mirrors, lenses, etc. Only a small percentage of the holes are used at any one time. The balance are exposed for all to see.
- Colorado Springs, Colorado
November 17, 2010
Missing is the size of the holes, area of the board and thickness (weight).
Option 1, use an appropriately colored "sharpie". This will not add any corrosion or abrasion resistance to the board, will not wear off that bad and will not block the holes.
Option 2, If possible use a smaller pinch wire contact. This could be just the tip so there will not be too much electrical loss. It probably would need to be replaceable and be of aluminum. The customer should pay for these racks since his requirements are not reasonable (unless your firm is doing a poor job because of using multi purpose racks)
Option 3, Have management work with the customer. Could 4 of the holes be untapped for contact points and then use helicoils after the anodizing. Could 4 extra larger holes be added and not tapped for the contact points. Could Stainless screws be added to block / cover the holes?
Option 4, Could the customer stand small rack marks on the ends or sides?
You have to have contact marks somewhere, and the smaller the hole, the worse the problem, particularly if the hole is also threaded.
- Navarre, Florida
First of two simultaneous responses -- November 18, 2010
OK, I feel pretty darned silly right now...for some reason I interpreted that as a "bread cutting board".
My solution would be to ask the customer if they could add a couple of tapped holes, perhaps on the backside where it's not readily visible, as a rack point for you.
(rant)I wish all engineers that design products to be anodized, or plated, would take the time to become familiar with the coating processes that their products require. And then proceed to design their parts accordingly. Too many folks don't know to think "finish first". It sure would save a lot of headaches for us on the coating end of things, and in the end, we'd have more satisfied customers.
I don't know about the rest of you, but at times I feel like we are asked to do the impossible by those that have very limited, or non existent knowledge of what we do on a daily basis (end of rant).
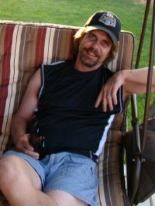
Marc Green
anodizer - Boise, Idaho
Second of two simultaneous responses -- November 18, 2010
Q, A, or Comment on THIS thread -or- Start a NEW Thread