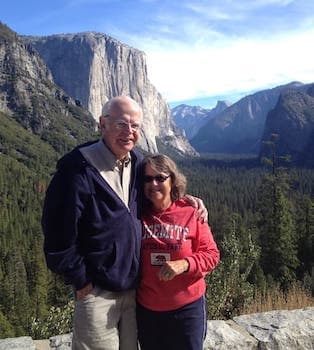
Curated with aloha by
Ted Mooney, P.E. RET
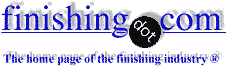
The authoritative public forum
for Metal Finishing 1989-2025
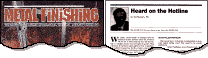
-----
Tin as addition agent in galvanizing
I am working as production manager at continuous galvanizing line. We are facing a problem of surface brightness which imparts after a few months when exposed to atmosphere. It is suggested to add Tin as bath additive in addition to Zinc, Aluminum and Lead.
Let me know,
a) usefulness of Tin addition in a Continuous Galvanizing line having Air Knife system especially in terms of permanent brightness as well as spangle formation.
b)Optimum %age of Tin as well as other additives i.e Aluminum and Lead.
ENGINEER - KARACHI, PAKISTAN
October 25, 2010
November 15, 2010
Sir:
If you read the book "Hot Dip Galvanizing" by Heinz Bablik (about 1940) you will find that Tin at about 0.35% causes potable galvanized water tanks to have a lifetime of about 1 to 2 years. Without the tin these potable water tanks have a lifetime of about 25 years. Also tin above 0.3% is now known to cause cracks in stressed steel galvanized structures.
I am doing some limited testing with 0.1% tin but because of past problems, there are not too many USA galvanizers wanting to use tin.
Regards,
Galvanizing Consultant - Hot Springs, South Dakota, USA
I am working as a production manager at a continuous galvanizing line. We are also facing the problem of surface brightness same as Mr. Musharraf Hussain of Pakistan. Surface brightness of GI sheets (color of GI sheets) are changed to dull or dark gray color after a few months when kept in warehouse.
Our line is hot dip galvanizing dry process. We use lead and zinc-aluminum alloy ingots in zinc bath. Production temperature of zinc bath was about 470 C. We use HCl in pickling tank and use double salt flux and preheating before galvanizing.
I would like to know what is the main cause of color changing and how can we avoid such thing to happen.
Production Manager - Yangon, Union of Myanmar
November 17, 2010
Thank you for reply but unfortunately it did not resolve my issue. I need a specific technical procedure or action required to retain surface brightness even on exposure to open atmosphere. Neither I could approach the book mentioned in reply nor any other literature is available.
Regards.
- KARACHI, PAKISTAN
November 19, 2010
Q, A, or Comment on THIS thread -or- Start a NEW Thread