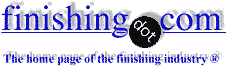
-----
"SMACK" Chrome Plating of Stainless Wheel Covers
I am involved in the restoration of old corvettes and one of the most enduring areas of myth and legend is related to the chrome plating of stainless trim such as wheel covers. the story goes that GM in looking to cut the high labor cost of mirror polishing wheel covers used a process called SMACK plating which used a reverse polarity process to make the chrome adhere to the nickel in the stainless.
My skeptical side tells me that chrome will only flow from the anode to the wheel cover at the correct polarity, so the whole idea of reverse polarity does not ring true. could they have used a reverse polarity process to bring the nickel to the surface of the stainless and then used conventional chrome plating processes? The claim is made by those who judge corvettes that once you buff through the factory plating to remove scratches and defects that the cover is forever marked as non-original since a standard nickel strike coat followed by chrome will yield a different appearance.
Anyone with knowledge of the process who can direct me to any published technical data on the process or any comments as to why a standard nickel/chrome process would yield a different look would be greatly appreciated.
- Austin, Texas USA
2000
It is a common practice to activate metal in a chromium etch tank and to some degree in the chrome plating tank by application of a proper reverse voltage and amperage. Further, the caps might have been electropolished and then chrome plated. The chrome will stick better for most people if it has a nickel strike, but it can be done without it with a lot more development time and effort.
James Watts- Navarre, Florida
2000
2000
Interesting conditions, why doesn't the water boil off? Is it pressurised? De-ionised water, at high temp' with lots of micro waves bouncing around, sounds like corrosion city.
1. Chromate conversion coatings fail at lower temperatures
(forgotten the actual temp') because the chromates form a gel coat and this dehydrates (most of this information I've picked up from finishing.com check around previous postings). As the aluminium is under water this won't happen, however I can't see why it wouldn't simply dissolve. Why not anodize? Oh right sorry you need to maintain conductivity.
2. the blackening of the tin on copper could be tin oxidising (my tin anodes blacken in acid conditions). I Couldn't say how easy plating tin on to aluminium is but tin is very good at adhering to surfaces once plated.
3. If it is tin oxidising it should just wash or wipe off, if it needs the chemicals you speak of then maybe it is silver (I haven't worked with silver so can't say more).
4. Tin is not normally sacrificial (mostly a barrier protection), but it is more active than copper and so will corrode to protect it. Silver I think wouldn't being more noble than copper.
I do have a suggestion, I think you use de-ionised water to guarantee purity for experimental purposes. So use distilled water, this is pure and is no more corrosive than tap-water (depending on your local supply). Good luck!
university - Glasgow, Scotland
Q, A, or Comment on THIS thread -or- Start a NEW Thread