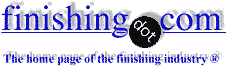
-----
Galvanizing Kettle Dust Collector - Bags Get Oily & Wet

Q. How toxic is this dust? Just wondering for PPE when changing the bags.
Aaron EzekielEmployee - Ontario
May 11, 2024
A. Hi Aaron,
No dust belongs in people's lungs, regardless of its constitution ... so dust masks are required regardless of what the bags have collected. As for other PPE, sorry I haven't seen the operation of bag changing that you are describing.
Luck & Regards,
Ted Mooney, P.E. RET
Striving to live Aloha
finishing.com - Pine Beach, New Jersey
⇩ Related postings, oldest first ⇩
for Engineers, Shops, Specifiers
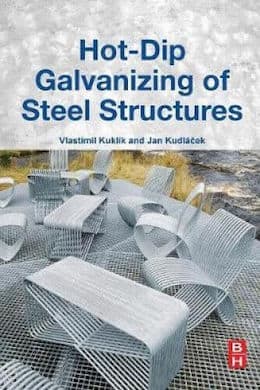
avail from eBay, AbeBooks, or Amazon
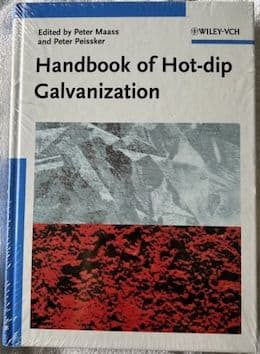
avail from eBay, AbeBooks, or Amazon
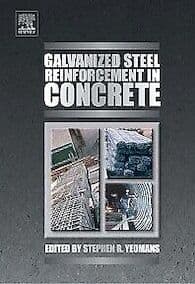
avail from eBay, AbeBooks, or Amazon
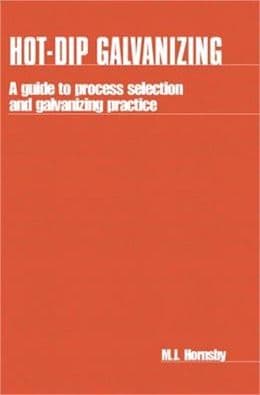
avail from eBay, AbeBooks, or Amazon
avail from Amazon
"User's Guide to Hot Dip Galvanizing for Corrosion Protection in Atmospheric Service" by NACE (1997 only rarely avail.)
avail from AbeBooks, or Amazon
(as an Amazon Associate & eBay Partner, we earn from qualifying purchases)
Q. Dear Sirs,
Good day.
I am from a Galvanizing Plant in Malaysia.
Recently, we have installed a dust collector over our zinc bath.
We are facing a problem where the filter bags become wet and appear oily,
thus rendering the dust collector inefficient.
Is this a common problem faced by Galvanizers?
My colleague had recently visited a plant in China, who has the same prob.
Does anyone know the cause of this?
And perhaps some advice on prevention method?
Thanks!
Galvanizing Plant - Employee - Selangor, Malaysia
October 25, 2010
A. The dust you are collecting is hygroscopic, so unless you prevent it, it will absorb moisture from wherever it can.
Ways to prevent it:
Do not let steam get into your extraction system. (if a moveable collection canopy for example, don't park it over wet tanks).
Do not let it suck moist air or even cool air when not extracting smoke from your process.
Have the whole filter lagged and trace heated.
Watch for dewpoint, do not allow the filter to go below dewpoint temp.
If filter is outside in rain, ensure there are no leaks allowing rain in. Remember it's under negative pressure, so will suck in any water at those leaks.
Don't dip wet steel. That steam goes straight into the filter and combining with the dust, forms mud which blocks the bags.
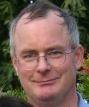
Geoff Crowley
Crithwood Ltd.
Westfield, Scotland, UK
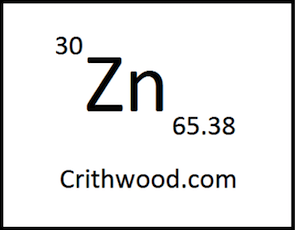
(1994)
by Miles L. Croom
on AbeBooks
or eBay
or Amazon
(affil link)
Q. Dear Geoff,
Thanks for your reply!
The hygroscopic dust you mentioned, is it Zinc Chloride from flux?
Unfortunately here in Malaysia, it is humid and rains throughout the year.
When hot air is sucked from the kettle into the dust collector chamber, I'm suspecting a drop in temperature which can result in condensation of water vapour (high relative humidity.) Maybe can consider adding a heater into the chamber.
Perhaps I should get another set of filter bags,
so that I can run the dust collector while washing & drying the previous set of filter bags.
Is it normal to clean the filter bags once every week or 2 weeks?
It certainly uses up a lot of man power & time
- Selangor, Malaysia
A. Part of the dust is ammonium chloride, but there's zinc oxide and other stuff there too, perhaps even residues of burnt oils, depending on how clean your steel is before immersion.
A good bag filter will come with a self cleaning system. This is often by using a shot of compressed air into the bags to flex them and break off the accumulated dust, provided the dust was kept dry. It will fall off into a hopper under the compartment of bags, for later removal.
If the bags get wet though, this won't really work, and washing them sometimes works, but the bags deteriorate, and often a single wash is all you will get before the material disintegrates beyond further use.
The actual humidity and temperatures need to be studied throughout the system to ensure that you don't get below dew point. This might require heating somewhere in your system, but that fact that you have a humid climate doesn't prevent engineering a solution. The humidity is high where I live too, (though temperatures far lower!), but the system can be made to work.
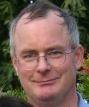
Geoff Crowley
Crithwood Ltd.
Westfield, Scotland, UK
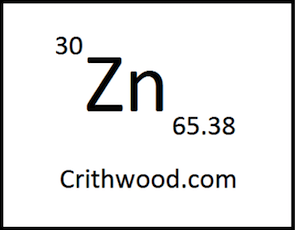
Q. Yes, we do have a self cleaning system using pulse of compressed air, however it is not working well as the filter bags often get wet.
Guess we have to consider some add-on for the dust collector since washing the filter is not a good option. What options can I consider?
i) Using heater
ii) Using desiccant
Any other options you would recommend? Thanks!
- Selangor, Malaysia
November 1, 2010
A. It doesn't matter how you keep the dust dry, just that you DO keep it dry.
I have no experience using a desiccant, but if you work out that this is a cost effective option, then try it.
Its more likely that heat, enough to keep the dust and gasses above dew-point, is going to work.
Good insulation of all ducting and the filter and its dust collection hoppers will help a lot, by retaining any heat applied. If you use electric trace heating, it can be thermostatically controlled to minimise energy use.
Do as much as you can to prevent sucking cold moisture laden air into the filter. What happens when there is no fume evolution at the zinc? (during a dipping cycle there's only a few minutes when fume is produced).
There's no requirement for extraction during all other periods, so what do you do? If you leave the filter running on normal extraction volume, then change that. Either fit a switch and turn it off, or an inverter and have it run at low revolutions until next part of the cycle that needs extraction. This way you will eliminate a lot of the moisture from entering.
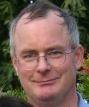
Geoff Crowley
Crithwood Ltd.
Westfield, Scotland, UK
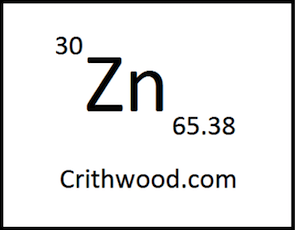
A. Sir:
I have a USA client that 20 years ago asked me why his baghouse dust was wet. I tested his flux and it had an ACN of 0.8 (double salt). I advised him to increase his ACN by adding ammonium chloride. He raised the ACN to 1.6 (quadraflux). His baghouse dust immediately became dry. This galvanizer died from lung cancer from smoking and now his son-in-law is managing the company. I recently tested his flux and the ACN was 1.2. I recommended that he raise the ACN to 1.4 which has now been done (to lower the %GZU). At no time in the last 20 years has the baghouse dust become wet. My experience is that above an ACN of about 1 the baghouse dust remains dry. In order to use triple salt or quadraflux there are some requirements.
Regards,
Galvanizing Consultant - Hot Springs, South Dakota, USA
Dear Geoff and Dr Thomas,
Thank you for your reply. Sorry for the late reply as I was away on a galvanizing conference. It seems that my previous comment was not posted in the forum.
Yes, we do plan to install an inverter to save on the electricity. Reducing moisture intake is certainly a great side benefit to it!
I have sent a sample of my flux for lab analysis, which put my ACN at 1.24. I've read that not many labs will be able to get the ZAC composition right, but since I do not have the capability to analyze the flux myself, trusting it to a lab is probably my best option at the moment. My flux baumé is around 21-24 Be.
The relative humidity in Malaysia is really high, my area with a mean of 80 - 95%. Condensation of water vapours often happens over night (since we do not do night shift) and wet our filter bags.
I've met an Indian equipment supplier during the recent conference, he was saying that this is also a very common problem with Indian Galvanizers. What he recommends is to add a heater to the flow inlet into the dust collector. Sounds logical to me.
- Selangor, Malaysia
November 25, 2010
----
Ed. note: Sorry, CS, we have found your reply of Nov. 3, which we apparently misfiled without posting.
A. Sir:
I invented ACN in the mid 1980's and it is the ratio ammonium chloride/zinc chloride and is unitless and independent of concentration.
You say your baumé is around 21 to 24 (I assume measured at room temperature). If we assume a baumé of 23 and allow 3 degrees baumé for the ammonium chloride dissolved in the flux (a good approximation) then my formula:
grams zinc chloride/L = 4.2 * baumé ^1.22
Then: grams zinc chloride/L = 4.2 * 20^1.22
Equals: 162 grams zinc chloride/L
Using the ACN formula this would be 162g/L times 1.24
Equals: 200 grams ammonium chloride/L
Does this agree with the lab results?
About 2003 I published the article: "Composition, Testing, and Control of Hot Dip Galvanizing Flux" in the journal METAL FINISHING. Table 4 in that article shows the test results for 13 USA certified labs testing a flux that I made up here on the ranch. I used exactly the same masses of zinc chloride and ammonium chloride (ACN=1.00). Results for ACN from the 13 labs ranged from 0.18 to 1.51. Two labs of the 13 labs got usable ACN's but only because they got both the zinc chloride and ammonium chloride concentrations wrong.
For your information I do not use ACN at all anymore. Rather I use ACNV in which the volatile components (only ammonium chloride in this case) is the only numerator and the denominator is the sum of the non-volatile components which include zinc chloride and iron(+2) chloride. Thus for ACNV you would have to know your iron(+2) and convert it to iron chloride. I have not "looked it up" in the Chemistry/Physics Handbook but I rather suspect that iron (2) chloride is also hygroscopic as is zinc chloride which is in your baghouse dust. Have your baghouse dust tested for chloride anion.
Even if the lab results are correct, your flux composition does NOT correspond to a European or USA type usable flux. Your ACN is too high to use a drying oven (without burning the flux) and your baumé is too high to use hot flux which would give a double layer on the product (dry outer layer and a wet mushy under layer) which would produce very excessive spatter and horrendous amounts of ash. This "highbred" flux is a mess; It is like trying to use the best of European and USA technologies, but the result is quite bad indeed.
Regards,
Galvanizing Consultant - Hot Springs, South Dakota, USA
Q. Dear Dr Thomas,
Thank you for your comments. You are right, we have very excessive zinc splatter. We are using hot flux (no dryer). Sad to say, our flux management is rather poor, therefore I'm studying on this topic currently. However, I'm rather new to this industry, therefore I really appreciate any advices from the experienced. I've also been reading up on previous letters and have gain some insights from them.
The lab result does not tally with your estimation.
i) ZnCl2 = 97.9g/litre
ii) NH4Cl = 121g/litre
Do these values seem too low for a 23 baumé Flux?
Iron content is 6.4g/litre (very high, I know...)
Are there any method you would recommend to obtain an accurate concentration of ZnCl2 and NH4Cl?
Using values from the lab result, does it mean that my ACN is 1.24, while my ACNV is 1.08?
Regards,
- Selangor, Malaysia
November 29, 2010
A. Sir:
If the 6.4 g/L Fe+2 concentration is correct (best is by dichromate titration) then FeCl2 concentration is 14.5 g/L. This is NOT a high value and corresponds to about 0.5% Fe+2. By using the lab FeCl2, my best estimate is that ACNV is about 0.1 unit lower than ACN. From knowing your FeCl2 (if it is correct) your ZnCl2 is likely about 150 grams/liter, because FeCl2 contributes to the baumé.' There is no way that I can guess at your ammonium chloride concentration. I presume your lab used a specific ion electrode or a Kjdahl distillation. Both methods are difficult to get a good result.
I do have in-plant methods to get an accurate ACNV.
What temperature is you flux solution? How long do you leave product in the flux tank? After withdrawal from the flux solution and drying for a few minutes is the flux fully dried or do you have a dry outer flux shell with a mushy wet under-coating? What is the pH of your flux? How is it measured? What type of flux do you buy? (double, triple, or quadraflux) Do you periodically add ammonium chloride to your flux? Is your fluxed steel black? white? clear? or what color? Does it turn orange, grey, or black if you do not galvanize it quickly?
Galvanizing Consultant - Hot Springs, South Dakota, USA
Q. Dear Dr Thomas & Geoff,
The Fe(II) concentration is calculated via titration by permanganate in-house, the result is similar with external lab analysis. Over the months, the Fe(II) content has risen from 6.4 g/l to 9.8 g/l. Is it not significant? I've read that most recommends a concentration of 5 g/l or less, and it's best to have a concentration of below 0.8 g/l. We are concern that the iron content will increase our zinc usage.
A re-examination of the lab analysis report shows that the 97.9g/l is actually Zinc (Zn) concentration, if we convert it to ZnCl2, it should be 17.44 g/l, which puts our flux at a mole ratio of 1 : 1.5, an ACN of 0.7. We are arranging to send another sample with known concentration to the lab for a confirmation of accuracy.
Our flux temp is around 65 - 76° C
Flux dipping duration is 1 - 3min
After flux, product seems to form a dry crystal film, but when I wipe my finger across, my finger appears to be slightly wet
pH can varies from 3.8 to 4.9 (no control atm)
we use pH meter, which we verify by testing it on standard solutions.
We use triple salt
We do not top up NH4Cl
After flux, the steel colour is clear, certain areas stained red by iron(iii)
the fluxed steel turns yellowish if we leave it for too long
our recent baumé is controlled at 20-21. What baumé would you recommend for a triple salt hot flux?
May I ask how do your client prevent over-night condensation when the dust collector is not operating?
Thanks & Regards,
- Selangor, Malaysia
December 2, 2010
A. Re Fe concentration in flux: There's a high correlation between higher Fe conc and dross formation. Higher Fe, more dross produced = higher zinc consumption.
Re condensation off operating hours:
Don't let the filter and steelwork get as low temp as dew-point. Use insulation, and if necessary, electric trace heating, thermostat controlled to keep above dewpoint.
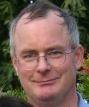
Geoff Crowley
Crithwood Ltd.
Westfield, Scotland, UK
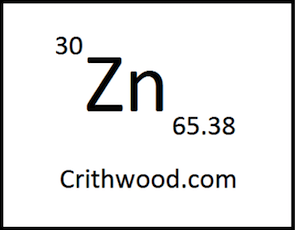
A. Leong and Geoff,
Permanganate solution is such a strong oxidizer that it degrades about 5%/month, whereas dichromate can be used as a primary standard with very long term stability.
9.8 g/L Fe+2 is about 0.86% Fe+2 and 35 years ago would have disturbed me. Now there are many, many ways to compensate for this medium level of contamination. Without knowing these ways to compensate for your iron (+2) you will get about 10% thicker zinc on the steel.
97.9 g/L Zn+2 corresponds to 204 g/L zinc chloride (ZnCl2 = (MWZnCl2/MWZn)*97.9g/L). In my previous post the estimated ZnCl2 is 150 g/L from the baumé.
ACN is a weight/weight ratio, NOT a mole ratio.
If the lab was correct for NH4Cl then your ACN is about 0.8 (121/150), and your ACNV is about 0.7. These are quite reasonable numbers because you do not add any separate make-up ammonium chloride. In other words on "day-one" your make up of new triple salt flux will have an ACN of 1.17, but as time goes by, the refluxing of the steel rejects (or previously galvanized racks) cause zinc to dissolve in the flux giving lower and lower ACN and ACNV. With ACN 0.8 or ACNV 0.7 this flux would be very hygroscopic and collect water from the air.
pH meters do NOT work in flux solution.
Clear color after fluxing is typical of low ACNV and so is the steel turning yellow.
I am currently at my client's plant in another state in the USA. He has no problems with moisture in his bag house, even though it is raining about half the time just now. Tomorrow we do ACNV in-plant testing. Much of the equipment is from Walmart.
My considerable experiences is that Fe(+3)hydroxide (orange solid) does cause more dross. It is also my considerable experience that iron(+2) chloride (green solution) does NOT cause dross (in a dry kettle), but does give thicker zinc coatings on the steel. From about 1972 until about 1980 I purified (removed Fe+2) from many, many in-plant, operating fluxes. In many cases the galvanizers said they were looking forward to less dross. It NEVER happened. Zinc coatings on the steel were decreased by about 10% to 25%.
I am here, in my client's plant, working on a direct replacement for nickel in the zinc and it is working very, very well.
Regards,
Galvanizing Consultant - Hot Springs, South Dakota, USA
Q. Dear Geoff and Thomas,
During the recent Asia Pacific General Galvanizing Conference, there are reports on flux's iron content increasing zinc consumption. One specifically mentions that it increases the zinc coating thickness.
Regarding the Permanganate, we have been using small bottles packaging. So far, the degradation has not been noticeable, as we do not store them over long period of time after unsealing the bottle.
I'm aware that the ACN is ratio by weight, I was just using the mole ratio to indicate that my current flux is no longer a "triple" (1 : 3) salt flux.
Thank you for correcting my calculation, I've made a mistake in my calculation.
Regarding the pH, guess I've no choice but to start looking into pH indicators. Anyone kind enough to point me in the right direction?
I think it would be best for me to replenish a new flux. It will be too much hassle to drain out half the tank and replenish ammonium chloride. And also, I do not know the ways to compensate for the iron content. I've worked out the economics, even a small savings of 0.2% on GZU, the payback time is easily within 2 months.
I hope that the new flux will also solve the filter bags wetting issue. We will also install an inverter. If the problem still persist, then we'll have to seriously consider insulation and heating.
May I ask that if the flux is a proper Triple Salt, what colour should the item be after fluxing? What can we tell from the item turning orange, grey or black if we do not galvanize it quickly?
Thanks!
Regards,
- Selangor, Malaysia
December 7, 2010
Q, A, or Comment on THIS thread -or- Start a NEW Thread