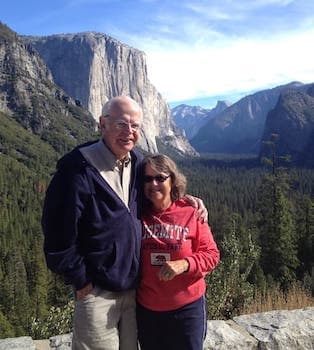
Curated with aloha by
Ted Mooney, P.E. RET
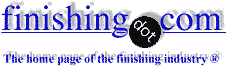
The authoritative public forum
for Metal Finishing 1989-2025
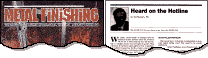
-----
Avoiding rusting screws in oceanfront construction
I construct high end residential homes on the ocean. I need to find a source to obtain screws in various assortments that will not rust. Is the black oxide over stainless the way to go?
Jeff GagliottiContractor - LI, New York, USA
October 17, 2010
October 18, 2010
Hi, Jeff. Black oxide is the finish on rifle barrels; it requires frequent cleaning and oiling to avoid rust even in benign environments. To completely avoid rust, you would need either very expensive stainless like type 347, or a clear coat on the stainless. Even 316 stainless will get surface rust.
Nickel-chrome plated screws would not rust at all for some period of time, depending on the quality of the plating; but an ocean front home isn't a Harley and I don't think I'd like the bling. Preferable might be to talk the homeowners into the fact that surface rusting in an oceanfront environment is acceptable and warm looking :-)
I love the not-quite-stainless stainless steel railings at the Lewes ferry landing.
Regards,
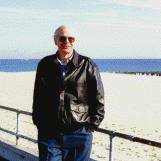
Ted Mooney, P.E.
Striving to live Aloha
finishing.com - Pine Beach, New Jersey
I suggest investigating stainless steel fasteners that are inherently corrosion resistant. Bufab Stainless is one manufacturer that specializes in stainless steel fasteners, and it offers a number of grades that are suitable for salt spray applications, including a high molybdenum version of Type 316, as well as duplex 2205 or even superaustenitic 254 SMO. Black oxide coatings for stainless steels do improve performance, namely delaying the onset of SCC, but when applied over Type 304 (A2 ISO 3506-1) they are more of a temporary measure rather than a permanent solution.
Toby Padfield- Michigan, USA
October 19, 2010
The dip spin exterior screws work quite well. I am on the water and have used 18-8 SS and the dip spin screws and both have worked well for 12 years.
James Watts- Navarre, Florida
October 20, 2010
Thank for your answers. The key the problem is the end product needs to be black in finish. I have had no luck with powder coated screws - or painted zinc. I'm trying to blacken stainless as I figure the stainless as the material under the black finish would be the way to go. I also have had no luck spray painting the stainless. Any suggestions on a material that will hold up and black in finish to the sea salt and weather? Thank You
Jeff Gagliotti- Southampton, New York
October 20, 2010
Hard TiAlN coating by PVD process has blackish colour and should give corrosion protection. But it could be expensive.
H.R. Prabhakara - ConsultantBangalore Plasmatek - Bangalore Karnataka India
October 21, 2010
I don't know if it would be an option for your particular needs, but there have been lots of posts in the past regarding the use of anodized and powdercoated aluminum fasteners in ocean front environments. If you go with BOTH, the chance of corrosion is very low, and aluminum fasteners come in pretty strong varieties.
Good luck.
Compton, California, USA
November 2, 2010
Jeff,
If the fasteners must be black, then Type 316 (A4 ISO 3606) with black oxide is probably your best bet. Paint or other coatings on stainless steel don't work very well.
Automotive module & component supplier - Michigan
November 3, 2010
I would try E-coat. It's thin, black, and extremely corrosion resistant. Usually superior to plating. E-coat is typically an epoxy, or the heads could succumb to UV degradation if they are in direct UV.
Adam AdkissonOperations - custom coater - S. Texas
November 5, 2010
To say that E-coat is superior to plating, one needs to identify the use and conditions of each. Black and cost are major factors for, but not the only ones.
A plater.
- Navarre, Florida
November 5, 2010
I WOULD SUGGEST Cadmium PLATING BUT I AM UNSURE IF THIS IS PERMITTED IN YOUR AREA.
MAHENDRA GARGATTI- BELGAUM, KARNATAKA, India
November 13, 2010
Q, A, or Comment on THIS thread -or- Start a NEW Thread