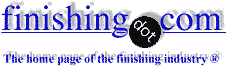
-----
"Cleanliness" requirement for passivation of stainless steel
I have a customer complaint concerning black residue on the inside diameter of a passivated part. Material is 321 sst and the basic geometry in question is a 0.720 bore x 2.375 deep into a 0.125 thru hole. Customer uses a long cotton swab rubbed on the drill angle. The swab comes off with a very minor amount of black residue, which leads me to my question-is zero residue expected from a passivated part? The spec required is PS1-5 which is an antiquated Lewis Engineering Spec, but I believe it is similar if not equivalent to QQ-P-35. Even after ultrasonic cleaning these parts, I still have a shadow of black on the swab. What is the expected result of the passivation process, and do you believe my customer is asking for cleanliness above and beyond that expectation?
Judy WilliamsQA Manager - West Winfield, New York, USA
October 12, 2010
You did not say what your ultrasonic treatment was, so it does not add much to your statement of the problem.
I will offer a wild guess that there is some cutting fluid burned into the metal when they bore the hole. This is difficult to get out.
I would try the Q-tips
⇦ on
eBay or
Amazon [affil links] bit with various solvents on a few parts prior to the passivation process. If it comes out black, then he has the option of cleaning the hole or paying you for the extra step.
I assume that you are going thru a caustic cleaning step. If you are, try adding periodic reverse and see if that will help.
Does your customer do a vapor degreasing. If so, this may cause a problem as many people will leave the part in the fumes an "extra long time" to "make sure that it is clean". This actually causes problems as it bakes some of the organics that are not quite soluble on to the part.
- Navarre, Florida
First of two simultaneous responses -- October 14, 2010
Judy
The problem is the cleaning not the subsequent passivation. If your customer wants the swab to come up clean, and you want to keep your customer, you need to come to terms with them and then meet the expectations. Change your process if it is not working. Find out if there is something the manufacturer is doing that contributes to the problem.
- Colorado Springs, Colorado
Second of two simultaneous responses -- October 14, 2010
Has anyone tried swabbing the surfaces before passivation and I do not remember if you mentioned the alloy. If it is 440C that may be the source of the problem.
I think that this question has been brought up because of the company's wish to satisfy the customer.
- Torrance, California, USA
November 11, 2010
Q, A, or Comment on THIS thread -or- Start a NEW Thread