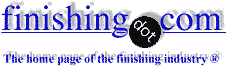
-----
Does anodizing screws uniformly increase electrical resistance over threads and shaft?
We use electrical stimulation to assess proper screw installation where a screw inserted properly will be in an insulated medium and a circuit made by stimulating the screw will be of high resistance. A poorly inserted screw that breaches the insulation conducts current more readily. The question is how do anodized screws behave in this situation? If anodization increases resistance, with the more anodization the higher the resistance, does anodizing screws equally coat the screw throughout? Do threads get more or less coated than the shaft?
Robert SmithStudent - Washington, DC, USA
October 8, 2010
My guess is that it does not make much difference as the anodize is going to crush as soon as you put a nut on it.
True, anodize is an insulator to a variable extent and it is hard. But, it is not particularly crush resistant.
- Navarre, Florida
October 8, 2010
It is true that you can crush the anodize, and a nut on the end of the screw - tightened sufficiently - would do it, but if you are going into threaded plastic, it would be fine.
So, to answer your question - they'll be close, but they are unlikely to be dead identical: The coating is non-conductive and therefor self-limiting, as it builds up in one area it becomes harder to anodize that area, making it other areas anodize more preferentially. The process isn't perfect though and other variables factor in - if the threads are deep enough and close enough it is hard to get new solution in between them, which would increase the resistance all by itself, which would result in a SLIGHTLY thinner coating at the bottom of the thread than at the top. On the flip side, if you have a very thick coating, there could be cracking at the tip of the thread (a hard coat, for example, would probably do this. A type 2, less so). And, of course, to anodize the screws they had to be in electrical contact with each other, which means that in at least one point somewhere on the screw there must be a small (sometimes - often - very very small, you may not be able to find it) unanodized contact spot.
It really comes down to how sensitive your test is - given that anodized fasteners have to stand up to corrosion tests the anodize has to be pretty consistent everywhere. Dependent on the amount of current your using, what you are tightening to the screws, how good the anodize was, and how sensitive your test is - it might work.
Compton, California, USA
November 2, 2010
Q, A, or Comment on THIS thread -or- Start a NEW Thread