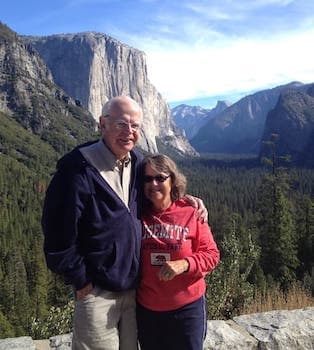
Curated with aloha by
Ted Mooney, P.E. RET
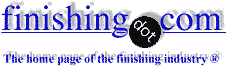
The authoritative public forum
for Metal Finishing 1989-2025
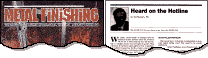
-----
Satin Finish Solution for High Density S/S Towel rails
Q. Hi all,
I work for a company manufacturing handmade stainless steel heated towel rails, we have an excellent reputation for producing high quality MIRROR FINISH rails, but are increasingly being asked to Produce more SATIN Rails.
Currently our Satin Rails are Pre Bushed before assembly using a 120-grit belt which is way too course, then the rail is immersed in the Nitric Acid and rinsed before packaging.
We would like to eliminate pre brushing and start our process after the rail is assembled, and so doing to order. This however poses various problems, the worst of which being finishing between the cross bars. The outer tube 'scratch' is horizontal and the cross bars being vertical so trying to clean the rail between using conventional grinders has been fruitless as the gaps are sometimes too small to keep the scratch marks in the same direction and we always end up chasing the marks when the machines catch on the opposing tube.
We have tried, various abrasives, Tizacht, Scotch Pad, Resealable belts, non woven, none of which has given us the uniform consistent finish we desire and caused constant problems between the cross bars and around the welds.
We have also tried sandblasting which we didn't consider consistent,
And due to the size of the rails vibratory is not financially viable,
I am now all out of ideas and definitely open to suggestion?
Technical Manager - South Africa
October 7, 2010
⇦ this on eBay or Amazon [affil links]
A. Hi, Mark.
I think skillful glass bead blasting, although labor intensive and perhaps eventually replaced by automated glass bead blasting, will give a great finish, close to what you are envisioning.
Regards,
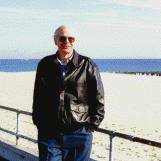
Ted Mooney, P.E.
Striving to live Aloha
finishing.com - Pine Beach, New Jersey
A. It is ALWAYS more efficient to pre finish as much as possible prior to fab. the answer to the clean up after is to use a Dyna File after to clean it up. There are various types depending on the project. You can use it either by contact or slack belt to achieve whatever finish you want.
Robin Thedemetal finishing - Toronto, Ontario, Canada
Q, A, or Comment on THIS thread -or- Start a NEW Thread