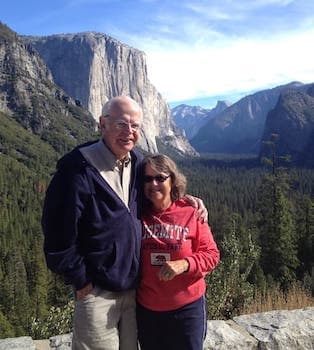
Curated with aloha by
Ted Mooney, P.E. RET
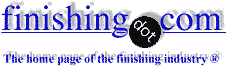
The authoritative public forum
for Metal Finishing 1989-2025
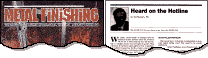
-----
Need thin corrosion resistant coating after TiN diffusion
My company diffuses Ti & N up to .005" deep into steels and other metals. We bring the surface hardness up to 72 - 74HRc with minimal size change. We are constantly being asked about is its' corrosion resistance. We do not promote this technology for corrosion resistance, but we would like to find a thin coating which could pass 1000 hrs of salt spray testing. Any suggestions.
Lou LechnerMarketing Mgr - Wheeling, Illinois, USA
September 30, 2010
Hi, Lou. 1000 hours is an awful lot to ask from a thin simple coating.
Regards,
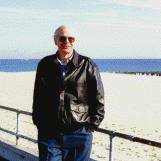
Ted Mooney, P.E.
Striving to live Aloha
finishing.com - Pine Beach, New Jersey
September 30, 2010
It is interesting to know that you diffuse Ti and N up to a depth of 0.005" into metals. Could you please explain the process and its applications briefly? What are the important properties of the diffused layer? Generally TiN is deposited as a coating ON the surface and it is only 2-4 microns. TiN is corrosion resistant. Sometimes people recommend multilayer coatings of Ti and TiN for corrosion and erosion protection.
H.R. Prabhakara - ConsultantBangalore Plasmatek - Bangalore Karnataka India
October 1, 2010
The technology is not PVD coating. We diffuse Ti & N chemically in a fluidized bed at temperatures in the range of 950f, similar to the temperature range of PVD tool coatings. The chemical reaction of the alloys and the solution transform the outer structure (up to 125 microns) of the material.
We are treating tooling and component parts to improve their performance.
Marketing Mgr - Wheeling, Illinois, USA
October 11, 2010
Hi, Lou.
I think before supplementary coatings are added, the first order of business might be to investigate the corrosion resistance of your hardening process on its own. Maybe it doesn't contribute much to the corrosion resistance, but maybe it contributes a great deal. I would think that you should find out by conducting salt spray testing. Good luck.
Regards,
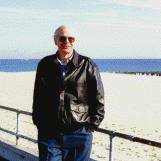
Ted Mooney, P.E.
Striving to live Aloha
finishing.com - Pine Beach, New Jersey
October , 2010
Have you tried an ultra thin, 7 to 10 mils thick, corrosion preventive compound? Do you want to remove the CPC at some point?
Larry Clark- Brunswick, Georgia
October 14, 2010
We have our in house test using a salt solution and submerge the parts for up to a week. We can usually tell if the parts will rust in 24 hours.
Lou LechnerMarketing Mgr - Wheeling, Illinois, USA
December 3, 2010
Q, A, or Comment on THIS thread -or- Start a NEW Thread