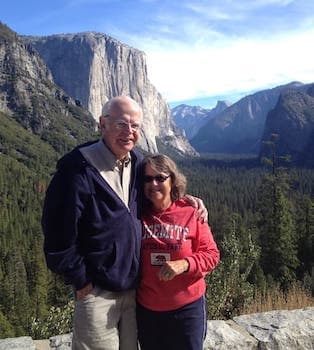
Curated with aloha by
Ted Mooney, P.E. RET
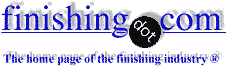
The authoritative public forum
for Metal Finishing 1989-2025
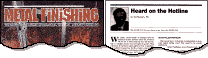
-----
Has AMS-QQ-P-35 Been Superseded by AMS 2700?
Q. Which is Which?! Has AMSQQP35 [canceled] been superseded by AMS2700? I have mil-spec hardware that calls out for passivation per AMSQQP35 [canceled], Type 6 or 7. The test reports from my supplier reflect the passivation was performed per AMS2700 B(AMS-QQ-35)Method-1-, Type-2- Do I have a problem here? And where can I obtain objective evidence to back it up?
John ClausenDefense Contractor - Anniston, Alabama, USA
September 23, 2010
A. Mil spec QQ-P-35 for stainless steel passivation was replaced by both ASTM A967 and AMSQQP35
[canceled] (the latter for aerospace applications). The notice for this is available from https://assist.daps.dla.mil/quicksearch/ ⇩
AMSQQP35
[canceled] was really just a temporary measure, a direct carryover of the mil QQ-P-35, to give SAE more time to prepare their replacement, which is AMS 2700. SAE's own website will tell you this: http://standards.sae.org/amsqqp35a
I've also got a scanned copy of the AMSQQP35
[canceled] cancellation notice from 2005 on the web at: http://www.citrisurf.com/amsqqp35_cancel.pdf
AMS 2700 Method 1 is the nitric baths, essentially unchanged from QQ-P-35. Type 2 is fine for any grade that type 6 or 7 would be used on.
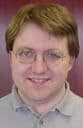
Ray Kremer
Stellar Solutions, Inc.

McHenry, Illinois
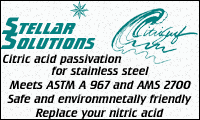
October 21, 2010
Ed. note Feb. 2025: That MIL specs site is currently https://quicksearch.dla.mil/qsSearch.aspx
A. QQ-P-35 was superseded by AMS-QQ-P-35 for aerospace products and AMSQQP35
[canceled] was cancelled and superseded by AMS2700, which has a class 4 which is supposed to be used when QQ-P-35 or AMSQQP35
[canceled] are specified. The difference is sample size for verification testing. You need to talk to your customer. Some customers require certifications to old specs even if they have been cancelled.
There can be a problem with using Type 2 when type 6 or 7 is required. All of the different types will yield satisfactory results with sufficient cleaning, passivation, and verification. The problem is that you will not have provided what the customer required. It can be argued that it is demonstrable that the parts have been passivated but that may not be good enough especially when types 6 and 7 are straight nitric acid at different concentrations and temperatures. Type 2, however, is nitric acid with sodium dichromate at a moderate temperature. Hope this helps.
- Torrance, California, USA
November 11, 2010
Q. I am a mechanical engineer working at a company that manufactures ordnance devices for military usage.
We have a part constructed from 304 SST, and our manufacturing procedure calls out for a Type II solution. I did some research, and found that we really should be using a Type VI or VII solution.
We are in the middle of dealing with our customer reviewing in detail all of our manufacturing steps for this product. The parts have already been made, but they were passivated using the Type II solution.
Is this an issue that I need to bring to their attention as a potential problem, or does the Type II work just as well as VI or VII? Can the sodium dichromate damage the 304 SST in any way?
If there is not a problem, then why would there be a separate callout depending on whether you are passivating 303 vs 304 SST?
Thank you,
- Hollister, California USA
May 23, 2013
A. Hi Jamie. We found a thread which appears to answer your question, and appended your inquiry to it. If I am misreading your question and you feel it is not answered, or you wish to follow up, get back to us. Thanks.
Regards,
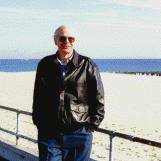
Ted Mooney, P.E.
Striving to live Aloha
finishing.com - Pine Beach, New Jersey
May 23, 2013
A. Jamie,
Given the notation you're using I assume you are still working off QQ-P-35. It's true that the process table in that document assigns 304 to Types VI and VII only. However, if the parts came out of the Type II bath with an acceptable appearance and there were no other difficulties, then they should be fine to use.
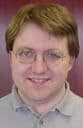
Ray Kremer
Stellar Solutions, Inc.

McHenry, Illinois
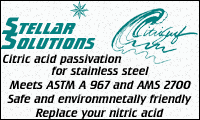
June 10, 2013
Q. We are Nadcap accredited for Chemical Processing, specifically passivation, and as such we follow AMS 2700 to the letter. The more I read that document and the document it superceded, QQ-P-35, the more I am confounded.
AMS 2700 gives requirements for Nitric Acid concentration in volume percent. In researching this it seems that no one ever does volume percent, everything is in weight percent. I have spent days with my old college chemistry textbooks looking for a conversion from weight percent to volume percent. We had this formula we have been using since way before I got here but I don't know where it came from (It seems to have come from the Electroplaters Process Control Handbook circa 1963). But here is one of the many things that drives me crazy. AMS 2700 section 3.3.6 says type VI nitric shall be 24-45% by volume in accordance with O-N-350. Well, O-N-350 is all in weight percent, as is A-A-59105 which superceded it.
And QQ-P-35's definition of Lot is strange. Three sentences that don't necessarily agree with each other and which AMS 2700 broke up into three options? I would appreciate others thoughts on this.
Metallurgist - Wrentham Massachusetts USA
April 1, 2014
A. Tino,
I have never seen a nitric acid concentration for a passivation bath expressed in weight percent, always volume percent. This includes QQ-P-35 and ASTM A380
, the "old boys" in terms of passivation standards. I expect that this is for ease of use, as the volume of concentrated nitric acid is much easier for shop workers to measure out than the weight.
Looking at O-N-350, it describes the weight percent of HNO3 (as a range, 61.0-68.2%) expected to be present in concentrated nitric acid to be used in various dilutions in other standards. All you're really expected to do is source nitric acid that is labeled as compliant to O-N-350, and then mix it in the volume percent specified.
For the non-chemist, this is really the simpler way to do it. If I say make a 25 weight % solution of nitric acid, am I talking about 25% HNO3 or 25% of 65% HNO3 solution? Calling for 25 volume percent of O-N-350 compliant nitric solution is easier for shop workers to manage.
Now, all that aside, AMS 2700 does have some issues with confusing or contradictory statements and overly complex or unclear requirements. I am attempting to bring them to the attention of the committee governing it for consideration for the next revision. If you can point out for me specific text or section numbers that you find confusing, I can present that to the committee as evidence that things should be reworded for clarity.
QQ-P-35 can't be helped, really. Copies still exist for historical reference but it's a dead standard.
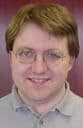
Ray Kremer
Stellar Solutions, Inc.

McHenry, Illinois
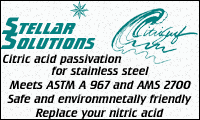
April 22, 2014
Q. ASTM A967 Type 2 and QQP-35C, type 2 are the same?
J zachariah- irving Texas
May 20, 2014
A. Hi J. Two different things are never really "quite the same" of course, J; please add a few more sentences so we can more clearly understand your question and not mislead. Alternately, I'd say get a copy of ASTM A967 and use that. Good luck.
Regards,
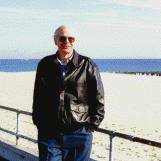
Ted Mooney, P.E.
Striving to live Aloha
finishing.com - Pine Beach, New Jersey
May 2014
May 22, 2014
J,
ASTM renumbered the nitric baths from QQ-P-35 to be sequential:
QQ-P-35 Type II -> A967 Nitric 1
QQ-P-35 Type VI -> A967 Nitric 2
QQ-P-35 Type VII -> A967 Nitric 3
QQ-P-35 Type VIII -> A967 Nitric 4
Some of you may note that AMS 2700 not only did not renumber the baths, it brought back the baths that had been removed during the revisions of QQ-P-35 (Types I, III, IV, and V).
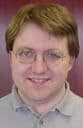
Ray Kremer
Stellar Solutions, Inc.

McHenry, Illinois
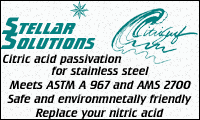
Q. What is the difference between QQ-P-35B Type II finish and Type VI finish and is there an advantage of one over the other for parts that will be sitting in semi-conductor cleanroom environment?
Louie Diep- Santa Clara, California
July 28, 2015
A. Hi Louie. QQ-P-35C is a "dead spec" cancelled 17 years ago, and QQ-P-35B was superceded by Rev. C almost 27 years ago. The reason people mention this as a potential problem is because even if it becomes widely known that there is a problem with a dead spec, there's nothing anyone can do about it ... so you really want to try to get updated to a current spec.
You can follow this link to QQ-P-35C (canceled) [link is to free spec at Defense Logistics Agency, dla.mil] and you will see that which types are applicable depends on the kind of stainless you are using -- so readers would need to know that before they can address your question. Good luck.
Regards,
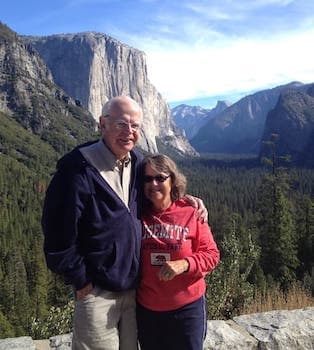
Ted Mooney, P.E. RET
Striving to live Aloha
finishing.com - Pine Beach, New Jersey
July 2015
Q, A, or Comment on THIS thread -or- Start a NEW Thread