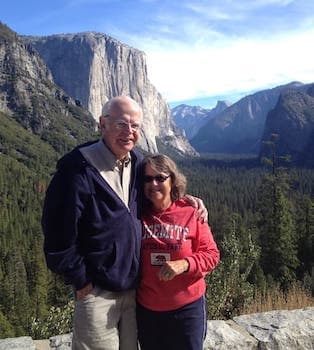
Curated with aloha by
Ted Mooney, P.E. RET
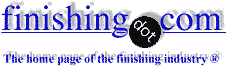
The authoritative public forum
for Metal Finishing 1989-2025
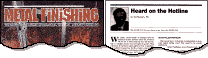
-----
Recovering contaminated silver plating tank to start fresh?
Q. We have 150 gallon 999 silver and silver strike tanks that are too old (carbonate too high). I would rather reclaim the silver (chem analysis at 45 pounds in the silver tank) and start fresh.
I am seeking any help you might offer on the fastest, cleanest, and easiest methods. Or, even a company that might offer the service at reasonable rate.
It appears to me that Electro-weaning by use of an electrolytic metal recovery unit might be the best solution but they are expensive and I wouldn't see using it again for 5 or more years unless I could possibly rent one or buy one and rent it out when finished.
Open to any and all suggestions!
thanks
Zachary Gibson
plating shop owner - Dallas, Texas
A. Here's how I would do it.
I would first transfer the solution to a treatment tank or several 55 gal plastic drums with the tops cut out. I actually would prefer working in drums. If you use drums, leave about 5 or 6 inches of space at the top. It will be much easier if the drums are first elevated high enough, before filling, so their contents can eventually be siphoned. You should have some way to stir the solution while treating. If using drums, the solution can be stirred with a plunger type stirrer using a SLOW up and down motion. The stirrer can easily be made with a 6" plastic disk, with a hole in the center, mounted on the end of a piece of 1" plastic pipe, using plastic pipe fittings. A 6" disk can be cut from the top of the drum.
If necessary, add enough sodium hydroxide to raise the pH to between 11.5 and 12.
While stirring, add 325 mesh zinc dust
⇦ this on
eBay or
Amazon [affil links]
tends to clump while in storage and should be broken up before adding. You can use a large squeeze-type flour sifter to break up the zinc and add it at the same time. It should take somewhere between .6 oz and 1.2 oz of zinc to precipitate 1 oz of silver, although more may be needed. Analyze the silver in the solution several times, on a filtered sample, to determine when enough zinc has been added to precipitate all of the silver and no more silver remains in solution. It's best to not add a great excess of zinc. Try to hit the zinc as close as you can.
When all the silver has been precipitated, hang several zinc bars in the solution to prevent re-dissolution of the silver. Allow the silver/zinc sludge to settle overnight. Siphon off the solution without disturbing the sludge. Filter the sludge and rinse it several times to remove as much cyanide solution as possible. Transfer the sludge to several plastic 5 gallon buckets. I wouldn't add more than 1 to 1.5 gallons of sludge to each bucket. Add enough water to cover the sludge. UNDER A FUME HOOD, with gentle stirring, carefully add some 20% sulfuric acid (battery acid
⇦ this on
eBay
or
Amazon [affil links]
diluted 50/50 with water will work well for this) to dissolve the excess zinc away from the silver. Add the sulfuric acid in increments. You should see a reaction. When the action subsides, add a little more sulfuric. At some point, an addition of sulfuric will produce no reaction. At that point, the silver powder remaining should be about 98-99% pure. NOTE: You must use a FUME HOOD for this, just in case you didn't rinse out 100% of the cyanide (which is difficult to do). The combination of the cyanide and the acid will produce hydrogen cyanide gas. This is the same gas used to execute criminals in our prisons.
With the right equipment and vessels, I could easily do the whole thing in 2 days, with only a 3 or 4 hours of labor.
Before processing the entire amount, I would strongly suggest going through the entire procedure, at least a couple of times, using 1 or 2 liter samples. This will give you a feel for how this works and will help establish the quantities of chemicals needed.
- Nevada, Missouri, USA
September 24, 2010
Hi, Chris. Thanks for the detailed instructions!
I especially appreciate your closing paragraph. Experienced people tend to run test batches and do "jar tests" rather than rely on highly theoretical calculations, but the people asking for advice sometimes might not realize that it's implied.
Regards,
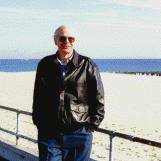
Ted Mooney, P.E.
Striving to live Aloha
finishing.com - Pine Beach, New Jersey
September 27, 2010
A. You could transfer the silver solutions to a spare tank ( open to plastic drums would be fine), then use a stainless steel anode and plate the silver out onto stainless steel sheet or screen. If you plate out slowly, say 3-5 ASF on the cathode you will get a reasonably sound deposit, and if you plate long enough, possibly one to two weeks, you can reduce the silver concentration to very low levels. The plated-up cathodes can then be used as anodes in your regular plating operation, thereby recovering the full value of silver at silver anode prices.
If you use multiple recovery tanks or drums, only one small rectifier is needed as they can be connected in series.
Much of the cyanide will be destroyed by the use of insoluble stainless anodes and the remaining cyanide solution can be disposed through one of the hazardous waste treatment companies.
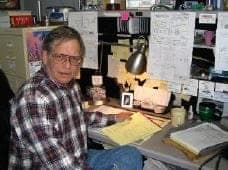
Jeffrey Holmes, CEF
Spartanburg, South Carolina
September 27, 2010
Q. Hello,
We rack electroplate silver over copper for industrial use (cosmetic appearance isn't critical), normally between 1-5 mil thickness. Typical maintenance includes treating to reduce carbonates and measuring the solution levels of potassium CN, silver CN, and potassium hydroxide. Occasionally the potassium hydroxide needs to be replenished, along with silver bars. Other than that, the solution is mostly trouble-free.
Over the course of about 2 days, our plating speed dropped by 50% for equal coating thickness. In other words, the racks are now submerged twice as long. There is a belief in the factory that the silver solution "expires" over time, even though all measurements appear to be within our typical range.
Is it true that silver solution expires with age? Are there any other likely causes to the such a dramatic drop?
Thank you,
Engineer - Pittsburgh, Pennsylvania, USA
May 30, 2013
A. Hi. Brad. Electricity must go somewhere, and I tend to doubt that highly experienced platers like in your shop could lose 50% of your efficiency and not immediately notice dramatic gassing or issues like that, and the defects that it would probably produce. So I suspect the rectifier has developed a defect that is indicating that it is producing full current when it isn't.
Regards,
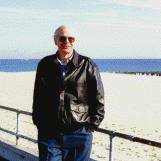
Ted Mooney, P.E.
Striving to live Aloha
finishing.com - Pine Beach, New Jersey
June 2, 2013
A. Hello Brad,
I agree with Ted's answer. If all the bath components are in range, there is sufficient anode area, anode bags are not blocked, connections all good, the problem would point to the rectifier. A clamp meter check (DC Amp setting) on cathode and anode bars under load will tell you if the amperage applied is accurate. Silver plating solutions don't have a given shelf life. If maintained correctly they can last for many years.
Process Engineer - Mesa, Arizona, USA
June 5, 2013
A. I suspect your free cyanide is too low and the anodes have passivated.
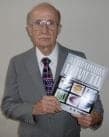
Robert H Probert
Robert H Probert Technical Services

Garner, North Carolina
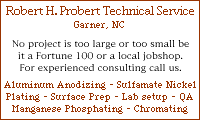
June 6, 2013
Q, A, or Comment on THIS thread -or- Start a NEW Thread