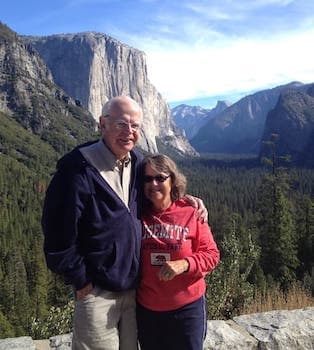
Curated with aloha by
Ted Mooney, P.E. RET
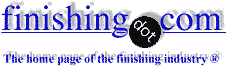
The authoritative public forum
for Metal Finishing 1989-2025
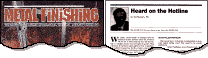
-----
Flash chroming stainless steel reflectors
I am plater and need to know how to flash chrome stainless steel reflectors. The reflectors may or may not be polished so if there are different processes, I would need both. I use a nickel strike to plate stainless that that will be copper plated and polished prior to the chroming process. Thank you. David
David Fixplating shop employee - Grand Junction, Colorado, USA
August 14, 2010
Hi, David
Different phrases can mean different things in different contexts, but to me "flash chrome" is not a decorative process and is not used on top of copper plating. Rather it is a thin coating of chrome used on, for example, circular saw blades to reduce their friction, or on stainless steel auto trim to deter tarnish.
You seem to be describing a need for decorative-copper-nickel-chrome plating, but starting with a Wood's nickel strike to gain adhesion on stainless steel. It seems highly unlikely to me that you would plate chrome directly on copper for use as a reflector.
Regards,
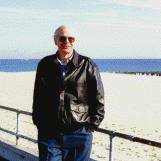
Ted Mooney, P.E.
Striving to live Aloha
finishing.com - Pine Beach, New Jersey
August 16, 2010
August 23, 2010
Recently I saw a show on TV that showed a man that casts hood ornaments in stainless steel, polished them then put them in chrome solution for ten seconds to give the parts a brighter chrome finish. Also, I have seen stainless steel for automobiles that was only chrome plated. I want to know the specifics of this process. What is the exact preparation and treatment of the stainless steel as well as the time and current density. I tried to do a reflector but only chromed about 1 inch around the outside which was not apparent until the part had set for several days. Your replies are greatly appreciated.
Thank you.
David
plating shop employee - Grand Junction, Colorado, USA
August 25, 2010
David
Could the video you saw have been electropolishing rather than chrome?
- Colorado Springs, Colorado
September 1, 2010
David
I have plated stainless steel but small pieces of tubes, easy to plate (activation required), operating conditions the same. operate as usual.
maybe your problem lies on the shape of the part, more tan other things.
- Bucaramanga, Santander
Maybe trying PVD in a vacuum chamber
Daniel Hernandez- Bucaramanga, Santander
September 1, 2010
September 1, 2010
No. It was plated in a chrome bath. I have seen stainless from the 50's on a Cadillac that only had chrome on it, no other plating. My original question was worded badly. I just need the particulars on chroming directly over polished stainless steel. Thank you for your response.
David
plating shop employee - Grand Junction, CO, USA
Hi, David.
From one point of view "chrome is chrome", and will not deposit at a low current density whether the substrate is stainless steel or anything else. An absolute minimum current density is 1 amp per square inch at 110 °F, and that may not really be quite enough. The fact that you achieved plating only on the high current density rim area says your current isn't high enough. But, depending on the details of these reflectors, you may not be able to plate the LCD area without burning the HCD area unless you use auxiiary anodes. 10 seconds sounds minimal; I think 20 seconds would be safer.
I have seen this "flash chroming" done on high carbon steel components, but haven't seen it done on stainless steel. I suspect that, because it's so thin and only for anti-tarnish purposes, that you may be able to do the plating by preceeding it with your normal electroclean and acid dip without doing a Wood's nickel strike or a special chromic acid etch, but I don't have the experience to say for sure. You might consult Guffie's book which includes advice for hard chroming directly on stainless steel -- but again I'm not sure that an etch is needed for such a thin chrome flash as opposed to a heavy hard chrome deposit. Good luck.
Regards,
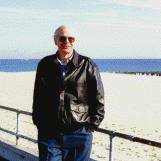
Ted Mooney, P.E.
Striving to live Aloha
finishing.com - Pine Beach, New Jersey
September 2, 2010
Thank you. I will try again.
David Fixplating shop employee - Grand Junction, Colorado
First of three simultaneous responses -- September 3, 2010
Second of three simultaneous responses -- September 3, 2010
Many millions of automobile parts are stainless steel with flash chrome. Think of wheel covers and trim rings, door and window moldings, wiper arms, light bezels, etc.
The stainless is polished mirror bright and then chrome flashed (usually one minute or so) exactly like any other chrome plating.
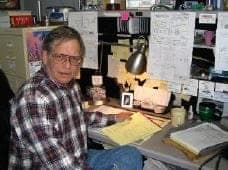
Jeffrey Holmes, CEF
Spartanburg, South Carolina
Third of three simultaneous responses -- September 6, 2010
you have two problem to solve
1)activation
2)current distribution.
so
1) Activation :
there are anodic and cathodic treatments to activate stainless steels. but do you have time and money to do it? if you have them do it that way.
if not immersion treatment is as follows...
immersion in 20%-50% sulfuric acid for at least one
Temp 150 - 180¶»¦
minute AFTER gassing starts.
the literature says that if the gassing does not start within a minute, you must touch the part with an iron rod. (sounds like witchery) I don't know why is it.
I have done it before nickel plating, sometimes a dark smut is formed but is removed in the nickel bath.
also you must be careful because sometimes the surface lost brilliance.
there is also another procedure
sulfuric acid......1%
hydrochloric acid...0.1%
Time ..............1/2 minute
and finally also with smaller pieces (small tubes of on three inches long by 1 inch diameter) I polish them to a high gloss and then clean them very quickly and activate with the second method and plate them.
2)current distribution
I have no experience chroming reflectors, but I am sure that the operating conditions are the same as usual auxiliary anodes maybe required due to the concave shapes of this pieces.
1.5 to 3 amps/inch2 - 13 amps/dm2
- Bucaramanga Santander
The activation step does not need to be complicated. A normal processing sequence would be: cathodic clean, rinse, activate(there are proprietary and generic processes which are a simple dip), rinse, chrome plate.
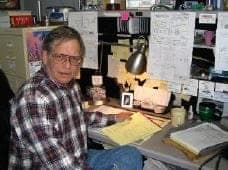
Jeffrey Holmes, CEF
Spartanburg, South Carolina
September 7, 2010
Q, A, or Comment on THIS thread -or- Start a NEW Thread