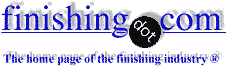
-----
Q&A on Gold Plating of Aluminum
Q. I'm looking into the possibility of Gold Plating aluminum plates which will be in constant contact with salt water and fresh water while being subjected to 217 degree heat.
This application must not produce any leaching of hazardous chemicals into the water and the use of Gold is being considered with the intent to prevent scaling.
The amount of plating which will be needed if this application works will be enormous and will continue for many years.
Thanks For Any Help!
Dave
David D [last name deleted for privacy by Editor]- San Clemente, California
2002
A. Hi...
I am not sure how practical your idea is. While it is feasible to gold plate aluminum (after a few steps), I don't expect the lifetime under the conditions you propose would be very long at all, and would ultimately fail.
I am wondering if your purpose would not be better attained by anodizing the aluminum. Is electrical conductivity a necessity? If not, I suspect hard- anodizing might be more to the point.
Vincent Summers- Charlottesville, Virginia
2003
2003
A. Depending on how much erosion the item would be exposed to, it seems like it could be made of electroless nickel plated aluminum followed by gold plating. It would be a research project, but it could perhaps also be gold plated after phosphoric acid anodizing.
I could be misunderstanding, but I think a non-ablative coating which prevents marine scaling without being toxic to marine scale life forms may be an oxymoron.
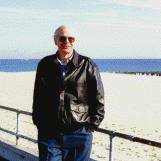
Ted Mooney, P.E.
Striving to live Aloha
finishing.com - Pine Beach, New Jersey
The issue with gold plating has been resolved and we have gone another direction which we believe is more cost saving in this venture.
Thanks
- San Clemente, California
March 24, 2009
Multiple threads merged: please forgive chronology errors and repetition 🙂
I am trying to gold plate a piece of aluminum, but have had no success. I tried the process first on steel to get a good voltage, and had no problems. On the aluminum, however, the gold is applied discolored and is not adhered to the work -- it easy wipes off.
I am using a cyanide solution; is there a better solution to use, or is aluminum just not an option to plate. Thanks for any light you can shed on the situation.
Thomas Reese- Gainesville, Florida
2002
A. Hi Thomas. You didn't tell us much about yourself and your projects yet, but it sounds like you may be a private individual doing hobby or art work. Plating on aluminum is a multi-step process involving proper aluminum pretreatment followed by zincating, then copper or electroless nickel, and nickel plating, all before the gold.
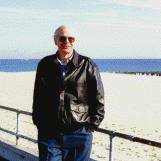
Ted Mooney, P.E.
Striving to live Aloha
finishing.com - Pine Beach, New Jersey
2002
Multiple threads merged: please forgive chronology errors and repetition 🙂
Q. I need to gold plate aluminum and have this plating withstand noxious chemicals CO and N+O compounds, elevated temperatures 200-300 F and electrical discharge of about 1-100amp/cm^2(with out sputter, loss of material). Thermal cycling can not be a problem. The material has to carry current with no galvanic corrosion. If I were to do the plating the chemicals involved would have to be environmentally safe and relatively cheap. The closest post to my application was on gold plating motorcycle parts the gold plating can withstand the temperatures but can it withstand the electric current and noxious compounds in my application?
Bradley Edward Bridgham- Daytona Beach, FL, U.S.A.
2002
I don't really understand the electrical requirement as phrased. Gold is quite a good electrical conductor, so the current doesn't sound excessive; but if there is some kind of contact making and breaking, rhodium plating on top of the gold would be appropriate.
The chemical environment sounds okay to me as long as the gold is thick enough to be pore-free. That raises the question of 'relatively cheap', which generally is not an adjective used to describe gold.
As for 'environmentally safe', unfortunately that's a buzz phrase that's popular, but actually meaningless :-)
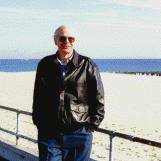
Ted Mooney, P.E.
Striving to live Aloha
finishing.com - Pine Beach, New Jersey
2002
Q. I need to have an electrical arc across two gold plated aluminum electrodes. I am going to be using about 400V DC at 100amp/cm^2 or more, current density is unpredictable but I have it reasonably controlled, and I can't have sputter (gold being lifted off the surface from ions leaving the surface).
Is Al from the hardware store anodized or does it have a small layer of corrosion that would need to be removed before zincating? If so how do I do it? The next step is copper plating, then sufficient nickel plating to stop copper migration finally gold plating on top of nickel plating. I read the copper nickel gold combination is used in electrical applications. Then it should work for my application right? How thick do you recommend each layer to be and what does that correspond to in current voltage and time required to plate? What is sufficient gold thickness in order to eliminate porosity? I have some gold 14-18 k jewelry I got REALLY cheap ( I got two sets) I would like to use one so I don't have buy gold. Would I get the results I am looking for if I use the jewelry? Should I just buy gold solution? I could always get two girl friends to give the jewelry away too:)
What products do you recommend? Would brush plating work? You're right, 'environmentally friendly' is a big buzz word. I was looking for something (if possible and cheap enough) that was biodegradable and non toxic. It's those darn cyanide rashes:-)
Thanks
Brad Bridgham- Daytona Beach Florida USA
2002
2002
A. I can't tell you the amount of arcing that gold can withstand, but I doubt that it's much. If there is to be arcing, rhodium is a more suitable final finish. So now the sequence is zincate, cyanide copper, nickel, gold, rhodium. Alternately you could consider zincate, electroless nickel, reactivation, gold, rhodium.
But you have to go to an electronic plating shop to get this done. The idea that you could do a complex plating procedure onto aluminum yourself from old scrap materials with no experience is beyond a stretch. As a minimum you need non-etch cleaning, etching, desmutting, zincating, cyanide copper plating, Watts or sulfamate nickel plating, hard acid gold plating, rhodium plating.
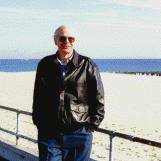
Ted Mooney, P.E.
Striving to live Aloha
finishing.com - Pine Beach, New Jersey
Q. If I were to use rhodium instead of gold what then would be the most direct sequence for rhodium plating on aluminum?
Brad Bridgham- Daytona Beach Florida USA
2002
A. Just rhodium instead of gold.
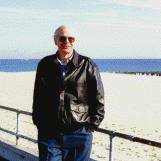
Ted Mooney, P.E.
Striving to live Aloha
finishing.com - Pine Beach, New Jersey
2002
Multiple threads merged: please forgive chronology errors and repetition 🙂
Q. Hi,
Can you please tell me (or point me to a reference) if you know whether gold plating (Gold plate Per MIL-G-45204 [link is to free spec spec at Defense Logistics Agency, dla.mil]C/TYPE II/GRADE A/CLASS 1) on aluminum would be able to withstand coming in contact with these chemicals without corroding (~temp 60 °C, 40%RH)?
(1) Betain (organic solver)
(2) Salts such as Ammonium Chloride NH4CL, Ammonium sulphate (NH4)2SO4, Magnesium sulphate Mg2SO4
(3) Ethylene Glycol,C2H6O2
If you don't think this type of plating is resistant enough to these chemicals can you propose a different type?
In your answer, can you please tell me if you're basing your response on intuition/experience etc or it's knowledge that is documented and readily available (or both).
Thanks,
MG
engineer - San Diego, California, USA
August 11, 2010
![]() |
A. Pure gold, electroplated non-porously, WILL withstand that list of chemicals, however, if the zinc from the zincate diffuses up to the top of the gold (with time and/or temperature) then those chemicals will definitely tarnish the appearance of the gold, so put a diffusion barrier of nickel between the zincate and the gold, a 10 minute strike of alkaline electroless nickel should do the trick. ![]() Robert H Probert Robert H Probert Technical Services ![]() Garner, North Carolina ![]() August 13, 2010 A. Aluminum is not a good choice as base metal for parts in contact with strong chemicals like chlorides. If you cannot switch to a safer metal, make sure the coating remains absolutely impervious during the expected life of the component. Gold is absolutely resistant but is too soft and not necessarily pore free. Keep in mind that if, for whatever reason (pore, crack, wear, dent, scratch, etc.), the chemical reaches the substrate, catastrophic destruction will proceed fast. The best way of avoiding this would to use a multi-layer coating as thick as affordable. Consider your proposed gold adding other resistant top coats. Monterrey, NL, Mexico August 14, 2010 |
Robert is quite right in that pure gold - or the cobalt or nickel hardened golds will easily withstand your stated chemicals.
However there are other considerations. Thin gold layers can be porous and allow attack of the substrate and aluminium is particularly vulnerable to this. For many years, the electronics industry has considered 5 microns of gold as the minimum to avoid porosity. Pore-free gold can be achieved at a lower thickness but this depends principally on the smoothness of the substrate. Hence the undercoat of bright nickel usually specified which also prevents diffusion of the base material degrading the gold.
The tone of your question suggests that the application may be safety critical so you should also consider acceptance testing for porosity. This should include certified thickness and porosity testing eg. dimethyl glyoxeme for a nickel sub layer.
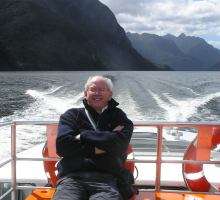
Geoff Smith
Hampshire, England
Gold Plating Aluminum diecast
I am interested in gold/black chrome plating aluminum die-cast, I understand the difficulty of plating aluminum but I am wondering if aluminum die-cast has the same characteristics. Thanks
Anthony AndersonHobbyist - Salisbury, Maryland, USA
August 12, 2011
August 12, 2011
Plating wrought aluminum requires a good set up and a bit of knowledge about the process, but it can be done by some shops with very few rejects.
Extruded is much more difficult.
Superior plating on cast requires great skill or special processes or lots of luck.
- Navarre, Florida
I agree with James but you still have chances to succeed as long as it is die casting. If it was sand casting you would absolutely have the odds against you all the time. Make sure your parts are produced under the strictest casting and finishing practices and go to a top ranked plater with solid experience in aluminum. Good luck. G. Marrufo
Guillermo MarrufoMonterrey, NL, Mexico
August 23, 2011
August 23, 2011
Hi, Anthony.
Years ago I was involved in a high production copper-nickel-chrome plating on aluminum diecasting project for consumer power tools. This was a real product, sold in volume. The tool company took one component that was normally powder coated, and chrome plated it instead, to differentiate the product line from competitors and their less expensive tools.
The first thing discovered was that the castings that had been fine for powder coating were no longer good enough. While they didn't have to actually make changes to the die casting process, they did have to go to 100% inspection because the tiniest barely-visible pinhead-size cold-shut was unplateable. As long as they continued offering powder coating as an alternative, this only involved sorting the castings rather than throwing half of them away; I don't know if you would have this flexibility. Then they had to add vibratory finishing on top of their hand finishing, and more losses and inspection cost at this step. Then they plated them with a typical cycle including zincate followed by cyanide copper; I don't think they did double zincating if I recall correctly.
The real kicker was they reduced what they called the "A" surface (in other words they reduced the quality standard) to try to maintain production -- and they were shipping and selling parts that had small blisters on the "B" surface, constantly talking themselves into "it's good enough".
Please believe James and Guillermo that it's not easy; and cast your QA rules in stone before you start :-)
Regards,
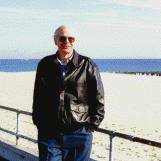
Ted Mooney, P.E.
Striving to live Aloha
finishing.com - Pine Beach, New Jersey
Q, A, or Comment on THIS thread -or- Start a NEW Thread